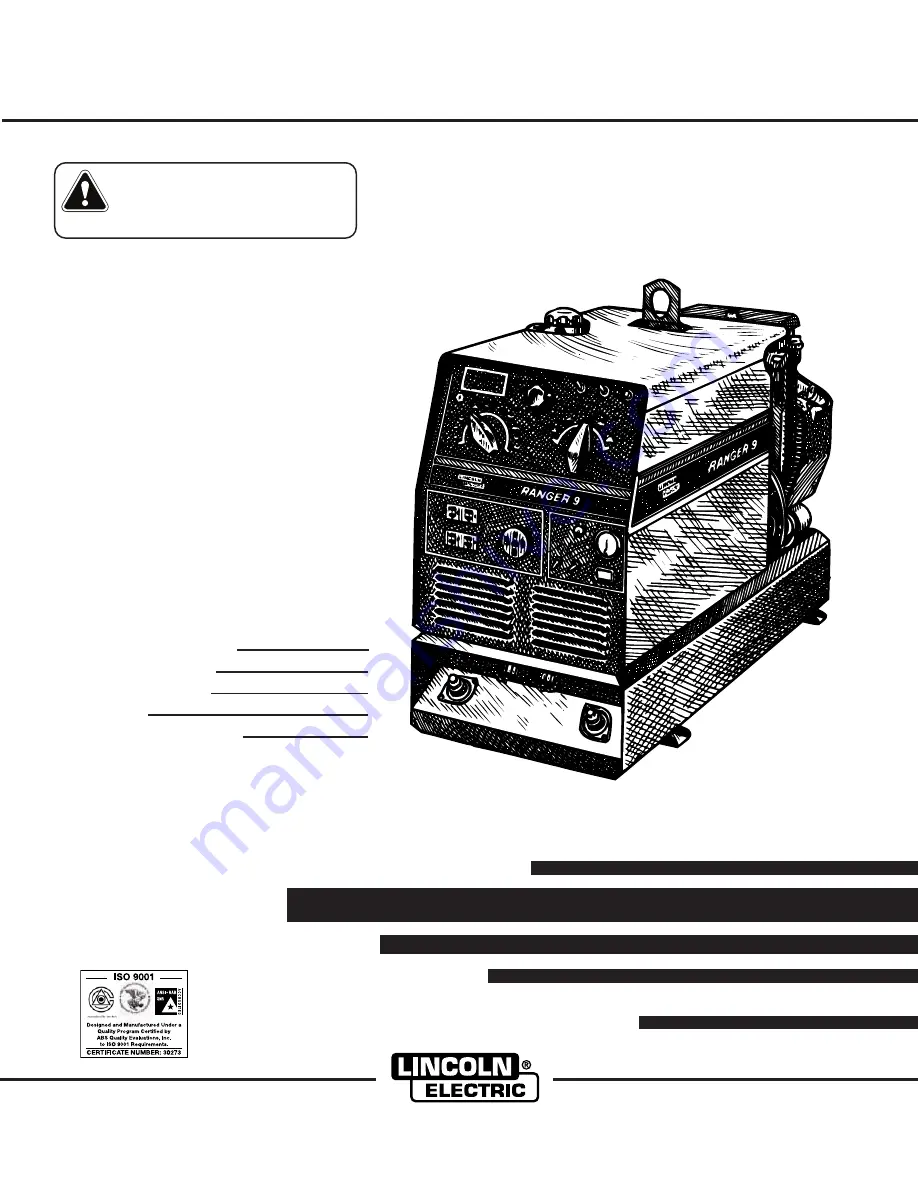
RANGER 9
Multi-Process Gasoline Engine Driven Welder and Power Generator
™
OPERATOR’S MANUAL
IM753-A
January, 2003
Safety Depends on You
Lincoln arc welding and cutting
equipment is designed and built
with safety in mind. However, your
overall safety can be increased by
proper installation ... and thought-
ful operation on your part.
DO
NOT INSTALL, OPERATE OR
REPAIR THIS EQUIPMENT
WITHOUT READING THIS
MANUAL AND THE SAFETY
PRECAUTIONS CONTAINED
THROUGHOUT.
And, most
importantly, think before you act
and be careful.
For use with machines having Code Numbers:
10909, 10939
• Sales and Service through Subsidiaries and Distributors Worldwide •
Cleveland, Ohio 44117-1199 U.S.A. TEL: 216.481.8100 FAX: 216.486.1751 WEB SITE: www.lincolnelectric.com
• World's Leader in Welding and Cutting Products •
Date of Purchase:
Serial Number:
Code Number:
Model:
Where Purchased:
Copyright © 2003 Lincoln Global Inc.
This manual covers equipment which is no
longer in production by The Lincoln Electric Co.
Specifications and availability of optional
features may have changed.
Summary of Contents for RANGER 9 IM753-A
Page 40: ...NOTES RANGER 9 ...
Page 41: ...NOTES RANGER 9 ...