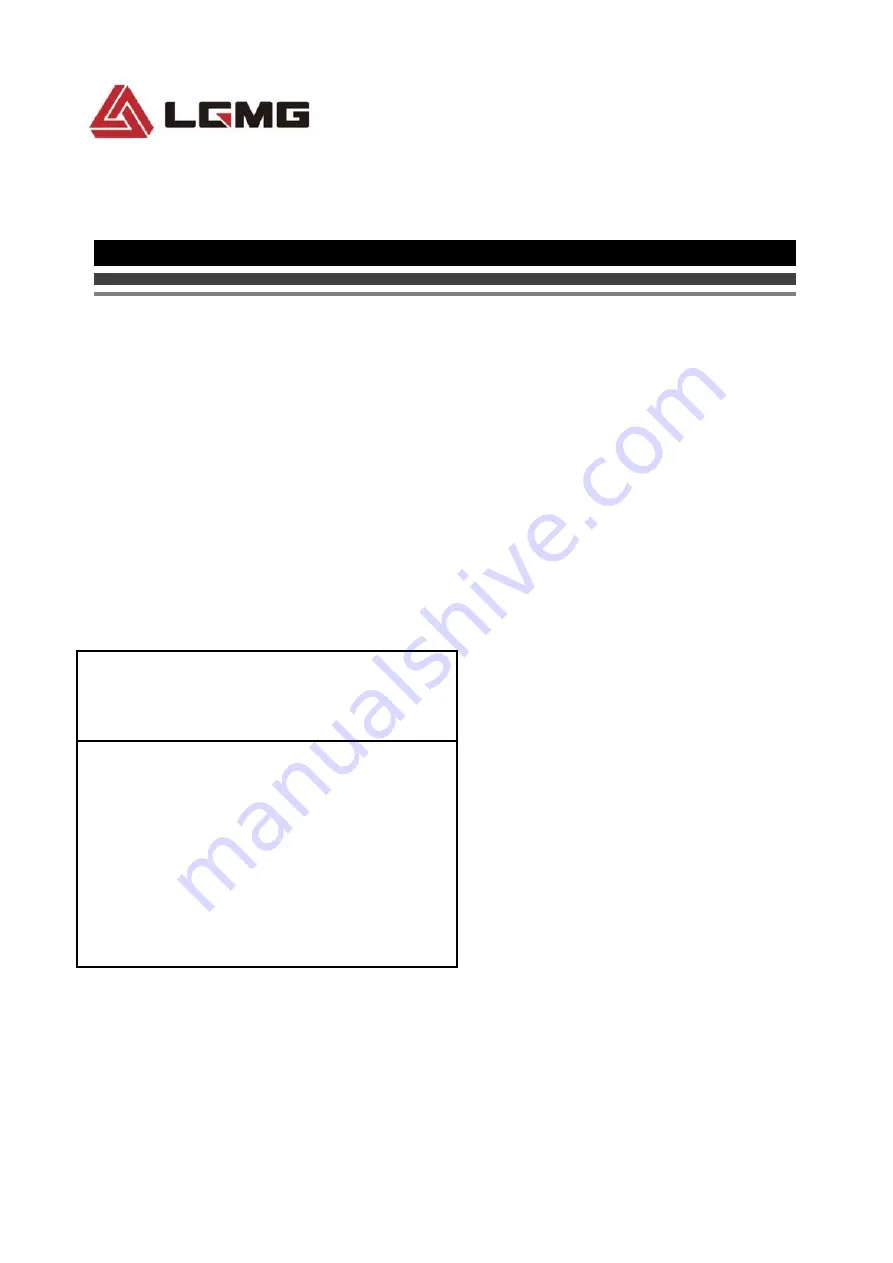
Maintenance Manual
AR16J
Mobile Elevating Work Platform
△
!
Warning
Before operation and maintenance, the
drivers and service personnel shall
always read and thoroughly understand
all information in this manual. Failure to
do so may result in, fatal accidents or
personal injury.
This manual must be kept with this
machine at all times.
.
LINGONG GROUP JINAN HEAVY MACHINERY CO., LTD.
Summary of Contents for AR16J
Page 6: ...Maintenance Manual of Elevating Work Platform 1 Chapter 1 Maintenance ...
Page 7: ...Maintenance Manual of Elevating Work Platform 2 ...
Page 28: ...Maintenance Manual of Elevating Work Platform 23 Chapter 2 Schematic Diagram ...
Page 29: ...Maintenance Manual of Elevating Work Platform 24 ...
Page 30: ...Maintenance Manual of Elevating Work Platform 25 Electrical schematic diagram ...
Page 31: ...Maintenance Manual of Elevating Work Platform 26 Hydraulic schematic diagram ...
Page 32: ...Maintenance Manual of Elevating Work Platform 27 ...