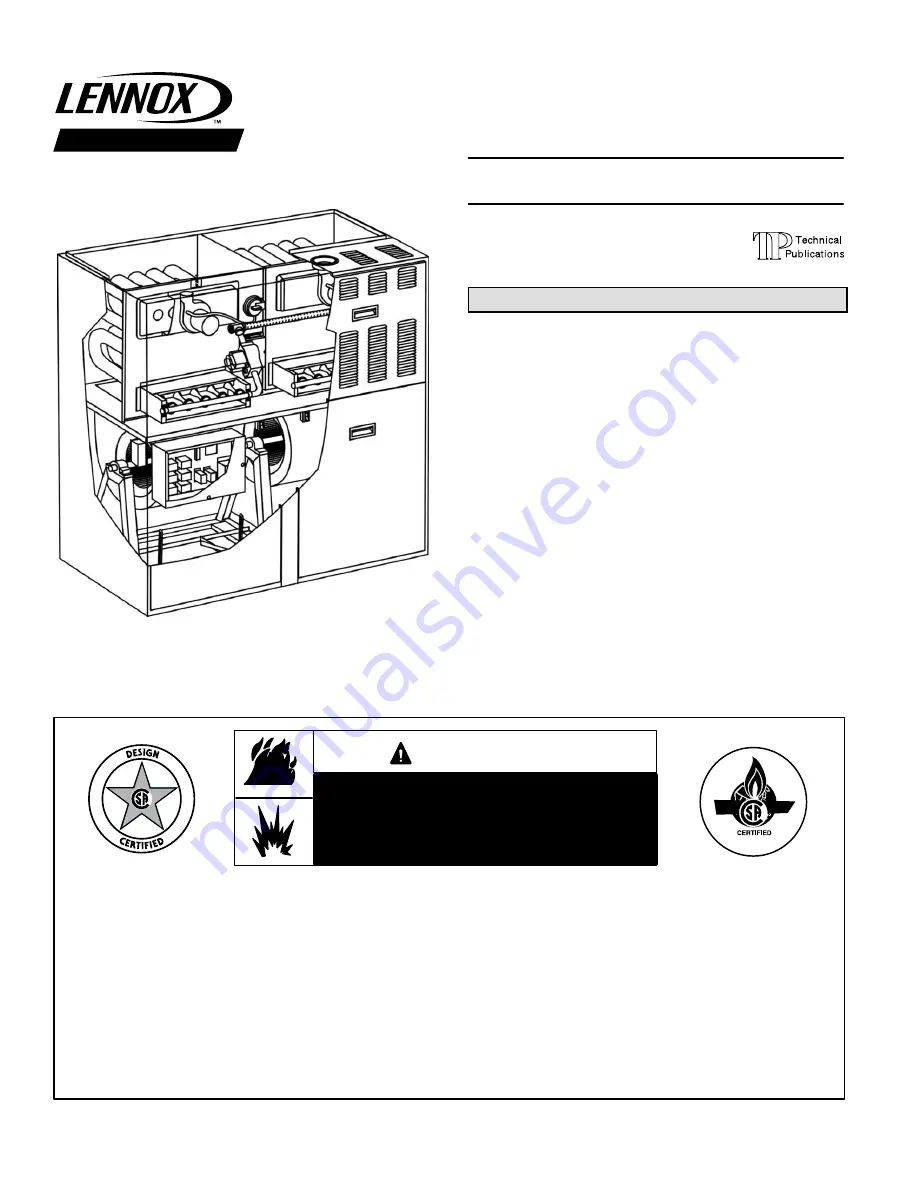
503,613M
*P504613M*
08/05
*2P0805*
PRODUCT LITERATURE
2005 Lennox Industries Inc.
Dallas, Texas
RETAIN THESE INSTRUCTIONS
FOR FUTURE REFERENCE
INSTALLATION
INSTRUCTIONS
G24-200
UPFLOW GAS FURNACE
Direct Spark Ignition
503,613M
8/2005
Supersedes 7/2003
Table of Contents
G24−200 Unit Dimensions
2
. . . . . . . . . . . . . . . . . . . . . .
G24−200 Parts Arrangement
4
. . . . . . . . . . . . . . . . . . . .
G24−200 Gas Furnace
6
. . . . . . . . . . . . . . . . . . . . . . . . .
Shipping and Packing List
6
. . . . . . . . . . . . . . . . . . . . . .
Safety
6
. . . . . . . . . . . . . . . . . . . . . . . . . . . . . . . . . . . . . . .
General
8
. . . . . . . . . . . . . . . . . . . . . . . . . . . . . . . . . . . . . .
Combustion, Dilution & Ventilation Air
8
. . . . . . . . . . . .
Setting Equipment
11
. . . . . . . . . . . . . . . . . . . . . . . . . . . .
Return Air Plenum / Filter Box Installation
11
. . . . . . . .
Duct System
13
. . . . . . . . . . . . . . . . . . . . . . . . . . . . . . . . .
Blower Motor and Drive Installation
13
. . . . . . . . . . . . .
Venting
14
. . . . . . . . . . . . . . . . . . . . . . . . . . . . . . . . . . . . .
Gas Piping
25
. . . . . . . . . . . . . . . . . . . . . . . . . . . . . . . . . .
Electrical
27
. . . . . . . . . . . . . . . . . . . . . . . . . . . . . . . . . . . .
Unit Start−up
33
. . . . . . . . . . . . . . . . . . . . . . . . . . . . . . . . .
Heating Sequence of Operation
34
. . . . . . . . . . . . . . . .
Gas Pressure Adjustment
35
. . . . . . . . . . . . . . . . . . . . .
High Altitude Information
35
. . . . . . . . . . . . . . . . . . . . . .
Other Unit Adjustments and Operation
35
. . . . . . . . . . .
Setting Blower CFM
37
. . . . . . . . . . . . . . . . . . . . . . . . . .
Repair Parts List
39
. . . . . . . . . . . . . . . . . . . . . . . . . . . . .
G24−200 Start−up & Performance Check List
39
. . . . .
Troubleshooting
40
. . . . . . . . . . . . . . . . . . . . . . . . . . . . . .
Do not store or use gasoline or other
flammable vapors and liquids in the
vicinity of this or any other appliance.
Installation and service must be per-
formed by a qualified installer, ser-
vice agency or the gas supplier.
WHAT TO DO IF YOU SMELL GAS:
Do not try to light any appliance.
Extinguish any open flame.
Do not touch any electrical switch; do not
use any phone in your building.
Immediately call your gas supplier from a
neighbor’s phone. Follow the gas suppli-
er’s instructions.
If you cannot reach your gas supplier, call
the fire department.
Leave the building immediately.
FIRE OR EXPLOSION HAZARD.
Failure to follow safety warnings exact-
ly could result in serious injury, death,
or property damage.
WARNING
Litho USA