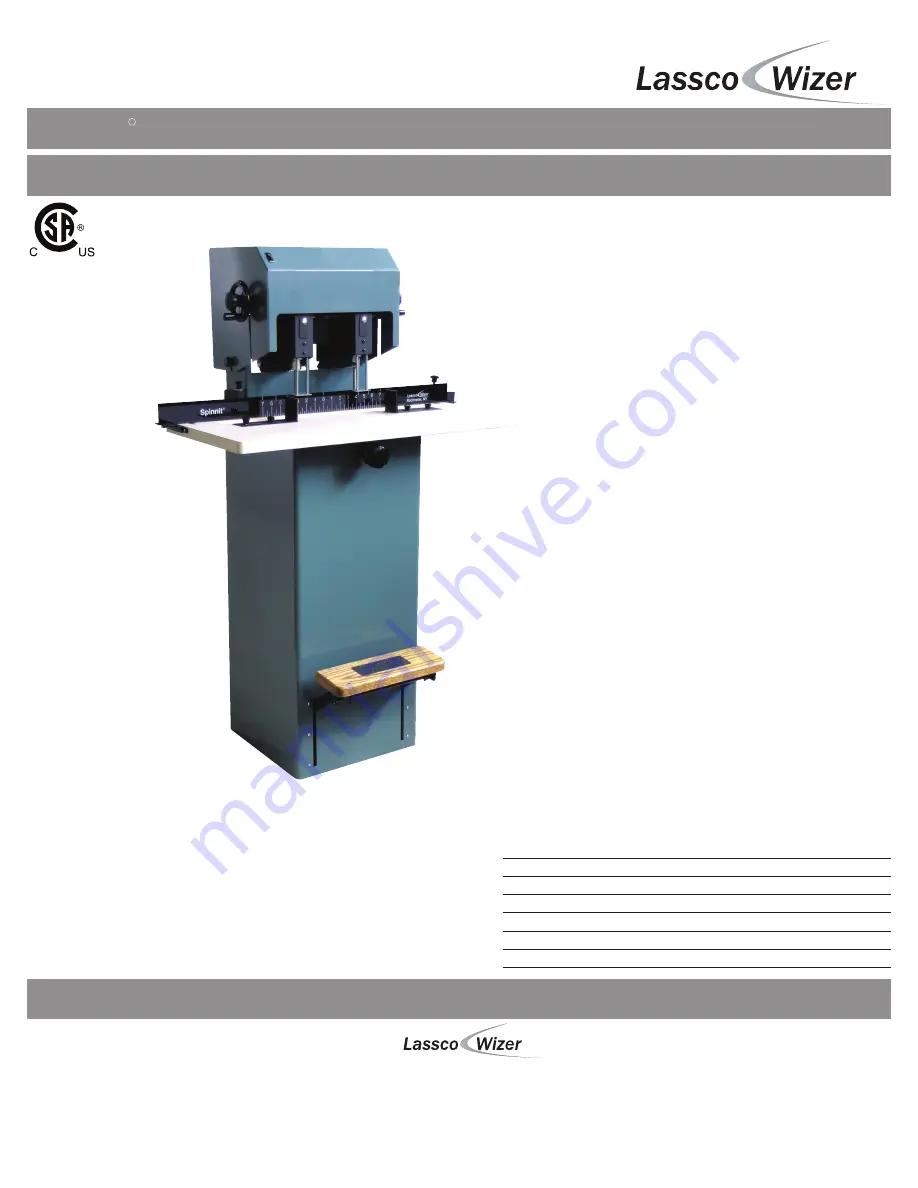
USER’S MANUAL
Spinnit
FMM
2
Manual Paper Drill
Before operating this equipment, please read these
instructions completely and keep these operating
instructions for future reference.
485 Hague Street, Rochester, NY 14606 U.S.A.
Tel: 585-436-1934
Fax: 585-464-8665
www.lasscowizer.com
Serial Number:
Date of Purchase:
Dealer:
Address:
Telephone Number:
-
R