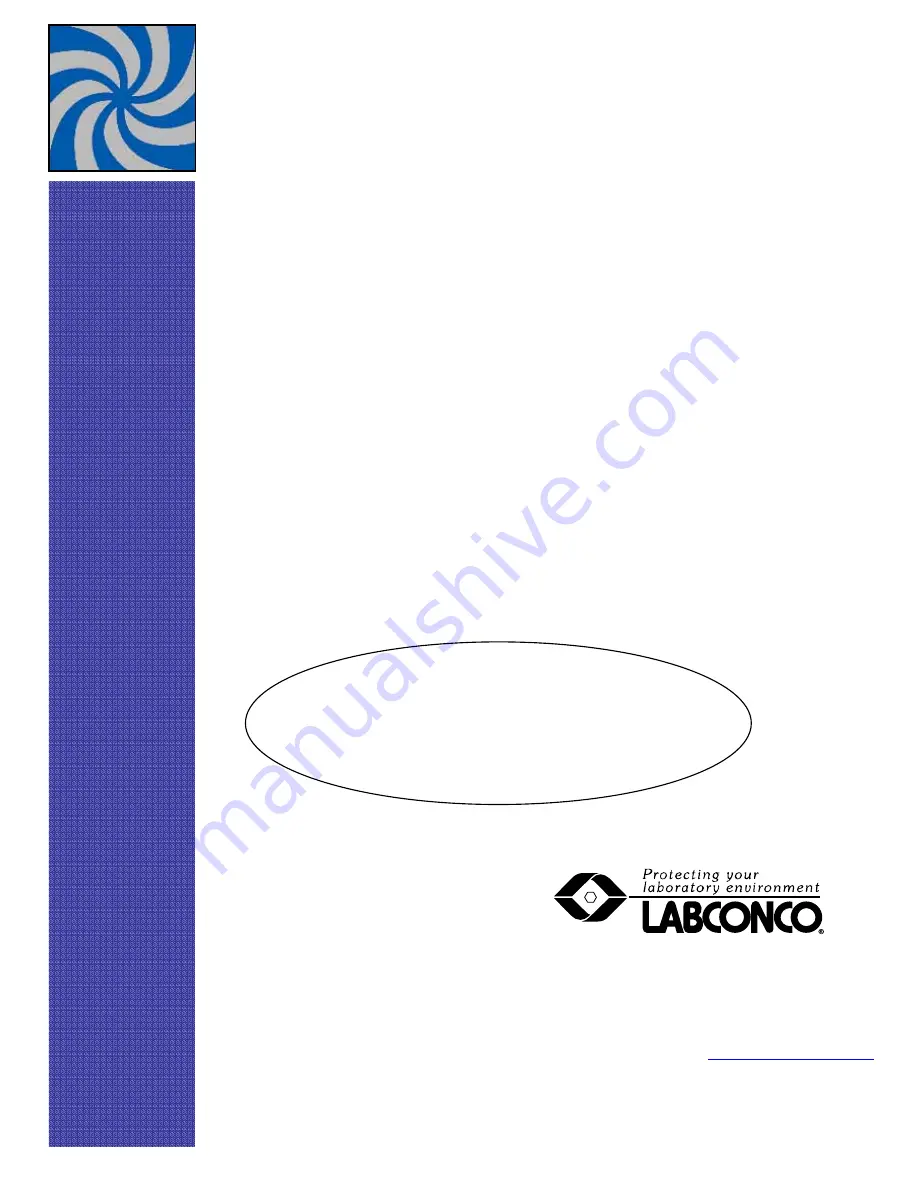
Labconco Corporation
8811 Prospect Avenue
Kansas City, MO 64132-2696
800-821-5525, 816-333-8811
FAX 816-363-0130
E-MAIL
HOME PAGE www.labconco.com
To receive important product updates,
complete your product registration card
online at register.labconco.com
User’s Manual
Purifier
®
Vertical Clean Benches
Models
3970200, 3970201, 3970203, 3970204, 3970220, 3970221,
3970223, 3970224, 3970300, 3970301, 3970303, 3970304,
3970320, 3970321, 3970323, 3970324, 3970400, 3970401,
3970403, 3970404, 3970420, 3970421, 3970423, 3970424
Please read the User’s Manual before operating the equipment
.
Summary of Contents for Purifier 3970200
Page 60: ...56 Appendix C Vertical Clean Bench Specifications Product Service 1 800 522 7658 C 1 ...
Page 61: ...57 Appendix C Vertical Clean Bench Specifications Product Service 1 800 522 7658 C 2 ...
Page 62: ...58 Appendix C Vertical Clean Bench Specifications Product Service 1 800 522 7658 C 3 ...
Page 63: ...59 Appendix C Vertical Clean Bench Specifications Product Service 1 800 522 7658 C 4 ...