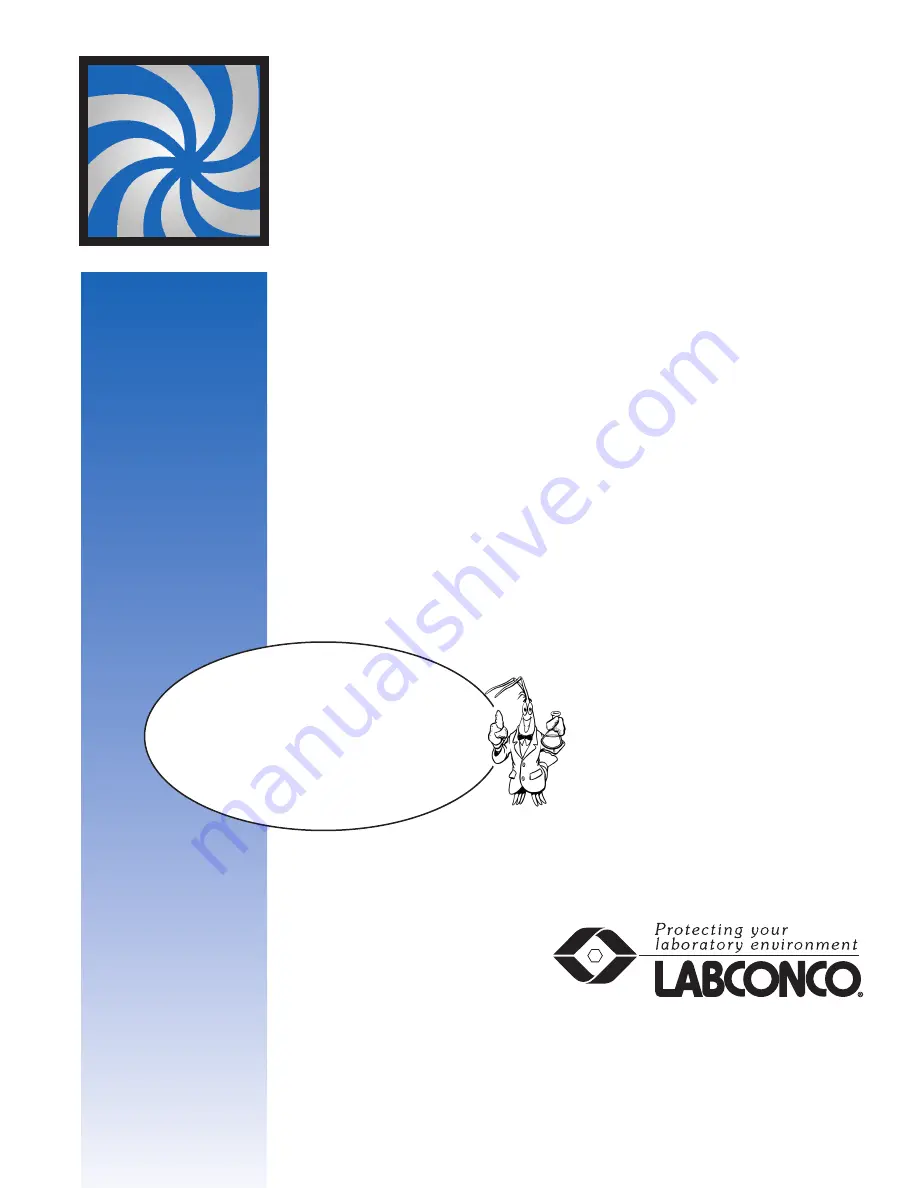
Purifier
®
HEPA Filtered Enclosures
& Purifier
®
Class I Filtered
Enclosures
User’s Manual
Labconco’s Mascot,
Labby the LABster
Register your product online at
www.labconco.com/productreg.html
or return the attached card and
receive
FREE LabbyWear
™
!
Models
3980200, 3980201, 3980202, 3980203, 3980220,
3980221, 3980222, 3980223, 3980300, 3980301,
3980302, 3980303, 3980320, 3980321, 3980322,
3980323, 3980400, 3980401, 3980402, 3980403,
3980420, 3980421, 3980422, 3980423
Summary of Contents for 3980200
Page 2: ......
Page 13: ...8 Chapter 2 Prerequisites ...
Page 17: ...12 Chapter 3 Getting Started Figure 3 1 Filtered Enclosure Installation ...
Page 67: ...62 Chapter 7 Accessorizing and Modifying Your Filtered Enclosure ...
Page 82: ...77 Appendix C Filtered Enclosure Specifications C 1 ...
Page 83: ...78 Appendix C Filtered Enclosure Specifications C 2 ...
Page 84: ...79 Appendix C Filtered Enclosure Specifications C 3 ...
Page 85: ...80 Appendix C Filtered Enclosure Specifications C 4 ...
Page 92: ...87 ...
Page 93: ......