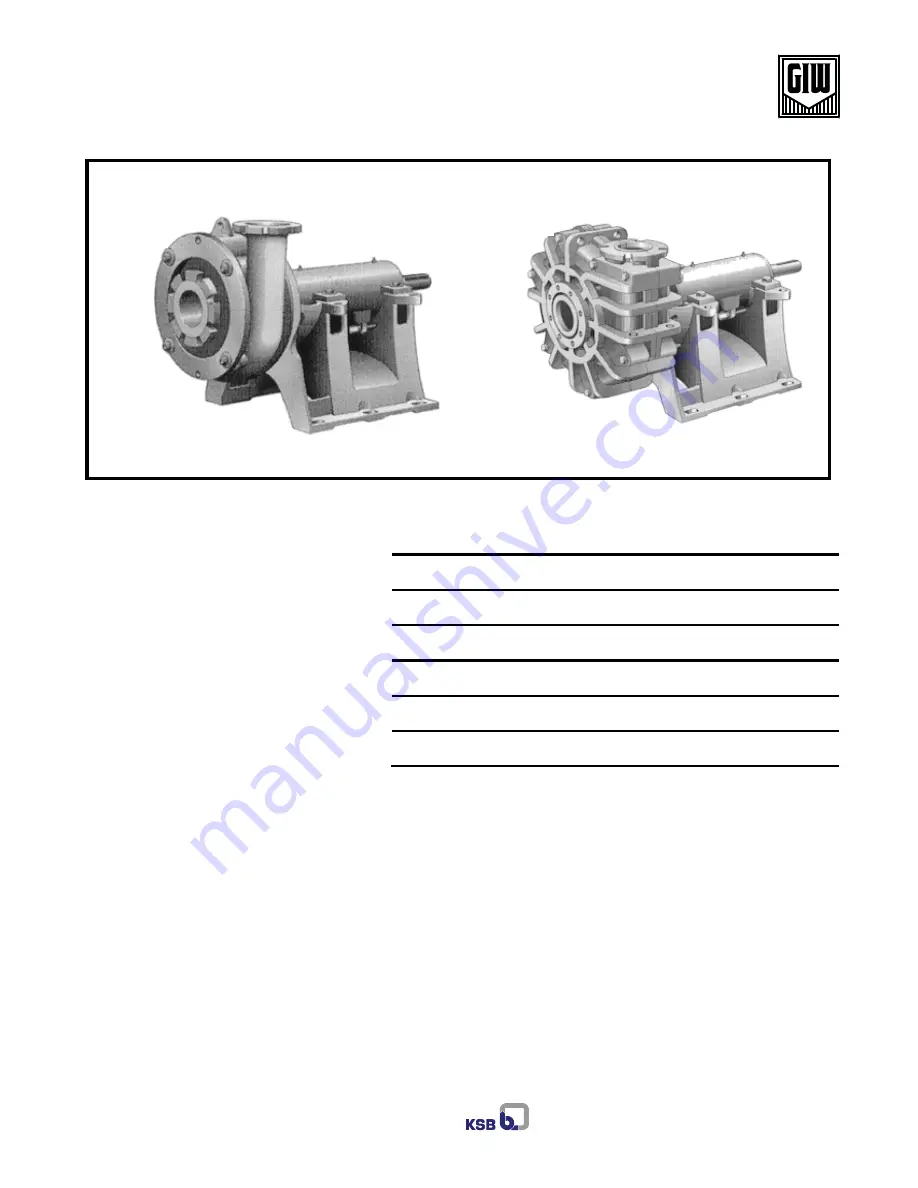
Maintenance Manual
2368.8000/A11-14 G2 (02/20/08)
LCC
A KSB Company
x
13-Mar-08
Pump Type:
LCC – H200-610.5M AM1
Pump Serial Number:
5012-13012 through 13015
Date:
March 13, 2008
Purchaser:
Metso
Minerals
Purchaser’s Order Number
P162737
GIW Sales Order Number:
G-150234
Shipped To:
Constellation Energy
Include the pump’s serial number when ordering replacement parts.
This manual may not be reproduced without written consent of GIW Industries. Additional copies
may be purchased. Please contact your sales representative for details.
GIW INDUSTRIES, INC.
KSB AG
KSB S.A.
5000 Wrightsboro Road
Bahnhofplatz 1
10/14, rue de la Gare
Grovetown, Georgia 30813 USA
D-91257 Pegnitz, GERMANY
F-76250 Déville-lès-Rouen, FRANCE
(706)
863-1011
(0 92 41) 71-0
32 82-32 00
FAX
(706 855-5151
FAX
(0 92 41) 71-17 91
FAX
32 82-3290
Slurry Pumps
LCC - Metal
LCC - Rubber
Summary of Contents for GIW LCC 100-400
Page 27: ...LCC 27 NOTES ...
Page 34: ......