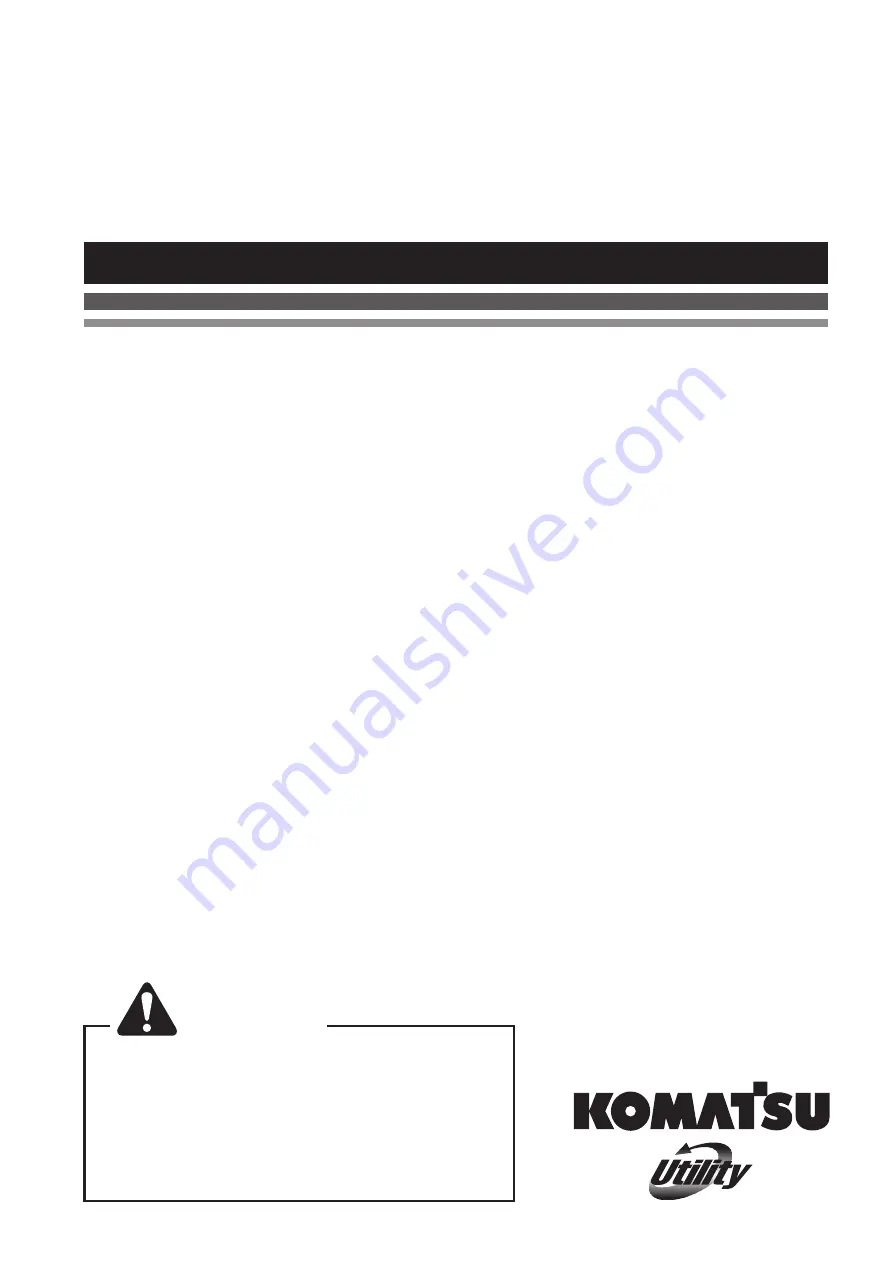
Operation & Maintenance
Manual
WEAM006000
BACKHOE-LOADER
WB93R
-5
SERIAL NUMBER
WB93R-5 F50003
and up
Unsafe use of this machine may cause serious injury
or death. Operators and maintenance personnel
must read this manual before operating or
maintaining this machine.
This manual should be kept inside the cab for
reference and periodically reviewed by all personnel
who will come into contact with the machine.
ATTENTION
Summary of Contents for F50003
Page 2: ......
Page 21: ...SAFETY AND ACCIDENT PREVENTION 19 ...
Page 23: ...SAFETY NOISE AND VIBRATION PLATES 21 SW L 1000 kg RKA13490 42N 93 11320 RKAB4740 42N 93 11310 ...
Page 64: ...62 THIS PAGE WAS INTENTIONALLY LEFT EMPTY ...
Page 65: ...THE MACHINE AND ITS OPERATIONS 63 ...
Page 166: ...164 THIS PAGE WAS INTENTIONALLY LEFT EMPTY ...
Page 167: ...MAINTENANCE 165 ...
Page 235: ...TECHNICAL SPECIFICATIONS 233 ...
Page 241: ...TECHNICAL DATA 239 5 1 3 3 LIFTING CAPACITIES TELESCOPIC ARM ...
Page 242: ...240 THIS PAGE WAS INTENTIONALLY LEFT EMPTY ...
Page 243: ...AUTHORISED OPTIONAL EQUIPMENT 241 ...
Page 283: ......
Page 284: ... 2005 KOMATSU UTILITY EUROPE S p A All Rights Reserved Printed in Europe ...