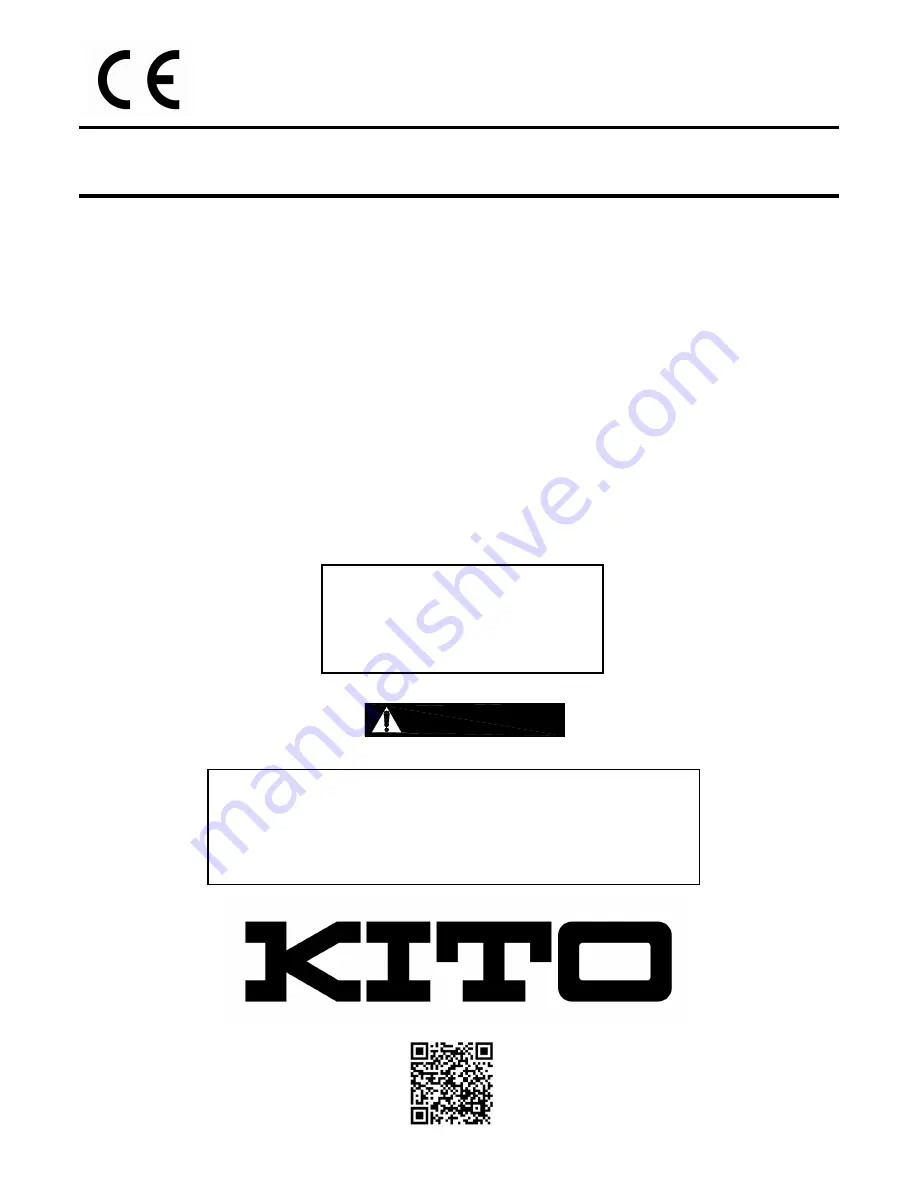
© HARRINGTON HOISTS, INC.
ALL RIGHTS RESERVED
Owner’s Manual
THEATRICAL
CHAIN HOIST
TNER
SERIES
1/2 Ton through 2 Ton Capacity
EFFECTIVE: June 28, 2022
Code, Lot and Serial Number
This equipment should not be installed, operated, or
maintained by any person who has not read and understood
all the contents of this manual. Failure to read and comply
with the contents of this manual can result in serious bodily
injury or death, and/or property damage.
Summary of Contents for TNER Series
Page 37: ...This Page Intentionally Left Blank 37...
Page 38: ...Figure 9 1 Housing and Motor Parts 38 9 1 Housing and Motor Parts...
Page 41: ...This Page Intentionally Left Blank 41...
Page 42: ...Figure 9 2 Gearing Parts 9 2 Gearing Parts 42...
Page 44: ...Figure 9 3 Hook Parts 9 3 Hook Parts 44...
Page 46: ...Figure 9 4 Chaining Parts 9 4 Chaining Parts 46...
Page 48: ...Figure 9 5 Electric Parts 9 5 Electric Parts 48...
Page 53: ...53 Appendix A Wiring Diagram...
Page 54: ...54...