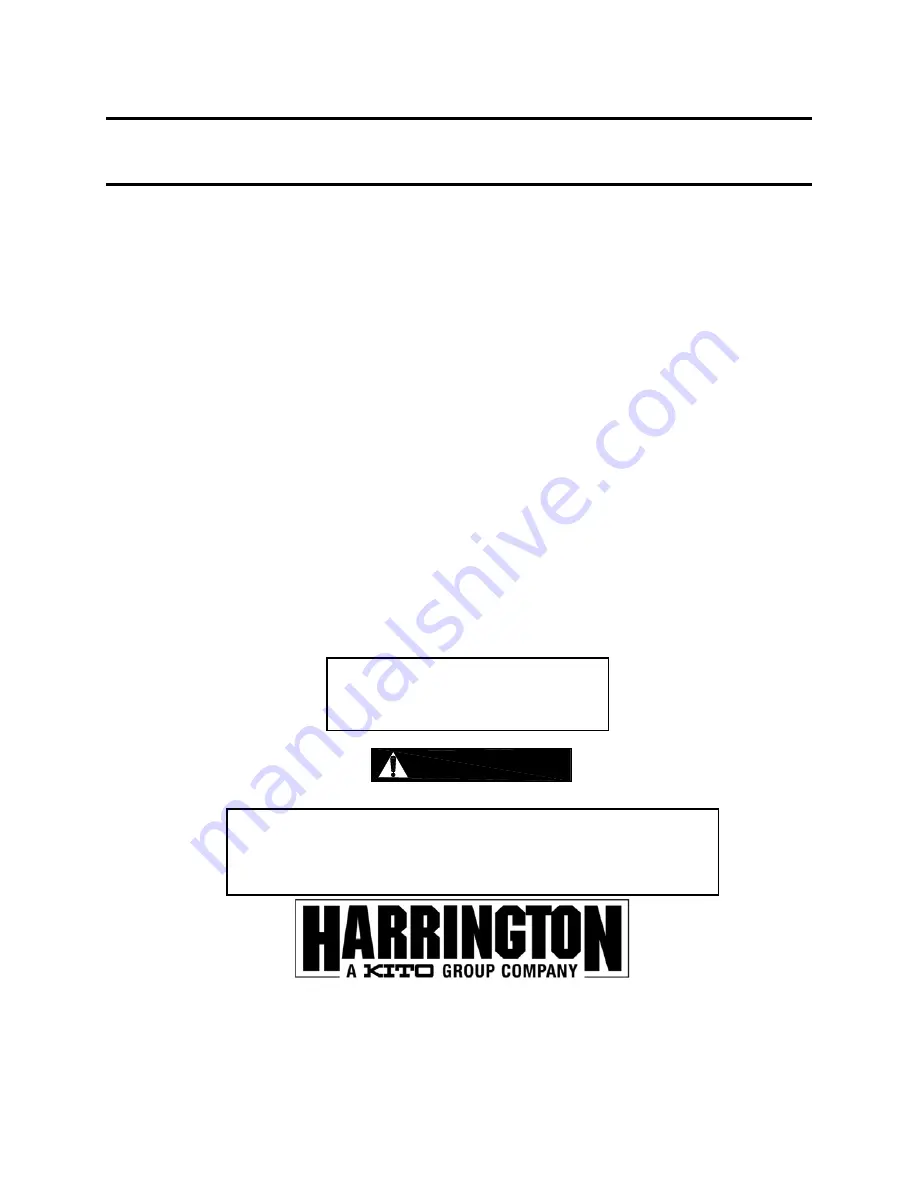
END
TRUCKS
Top
Running &
Underhung
SERIES 3
1 Ton through 10 Ton Capacity
Model and Serial Number
EFFECTIVE: August 18, 2021
This equipment should not be installed, operated, or maintained by
any person who has not read and understood all the contents of this
manual. Failure to read and comply with the contents of this manual
can result in serious bodily injury or death, and/or property damage.