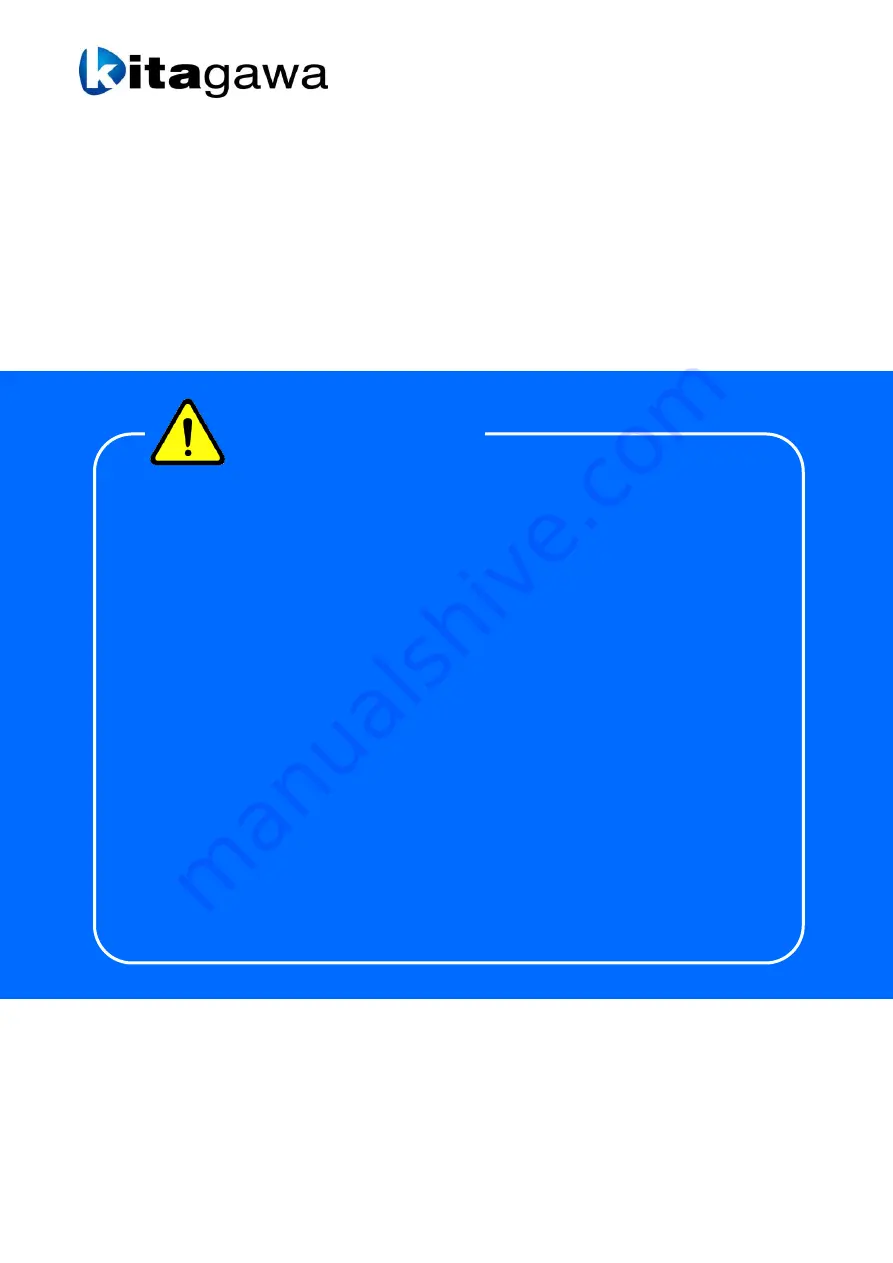
Versio n 1.0 7 (2021.08.03 )
Original instruction s
INSTRUCTION MANUAL
QB300
type
Quick Jaw-Change Chuck
Kitagawa Corporation
77-1,Motomach i,Fu chu -sh i,Hiroshima ,726-8610,Japan
TEL +81-(0)847 -40 -0561
FAX +81-(0 )847-45 -8911
・
This instruction manual is for production engineers and maintenance
personnel in charge of operation of this product. When a beginner uses
this product, receive instructions from experienced personnel, the
distributor or our company.
・
Before installing, operating or maintaining this equipment, carefully
read this manual and the safety labels attached to the equipment.
Failure to follow these instructions and safety precautions could result
in serious injury, death, or property damage.
・
Store this manual near equipment for future reference.
・
If any questions related to safety arise about this manual, please
confirm them with the distributor or our company.
DANGER
Summary of Contents for QB300
Page 22: ...21 Fig 8 ...
Page 60: ......