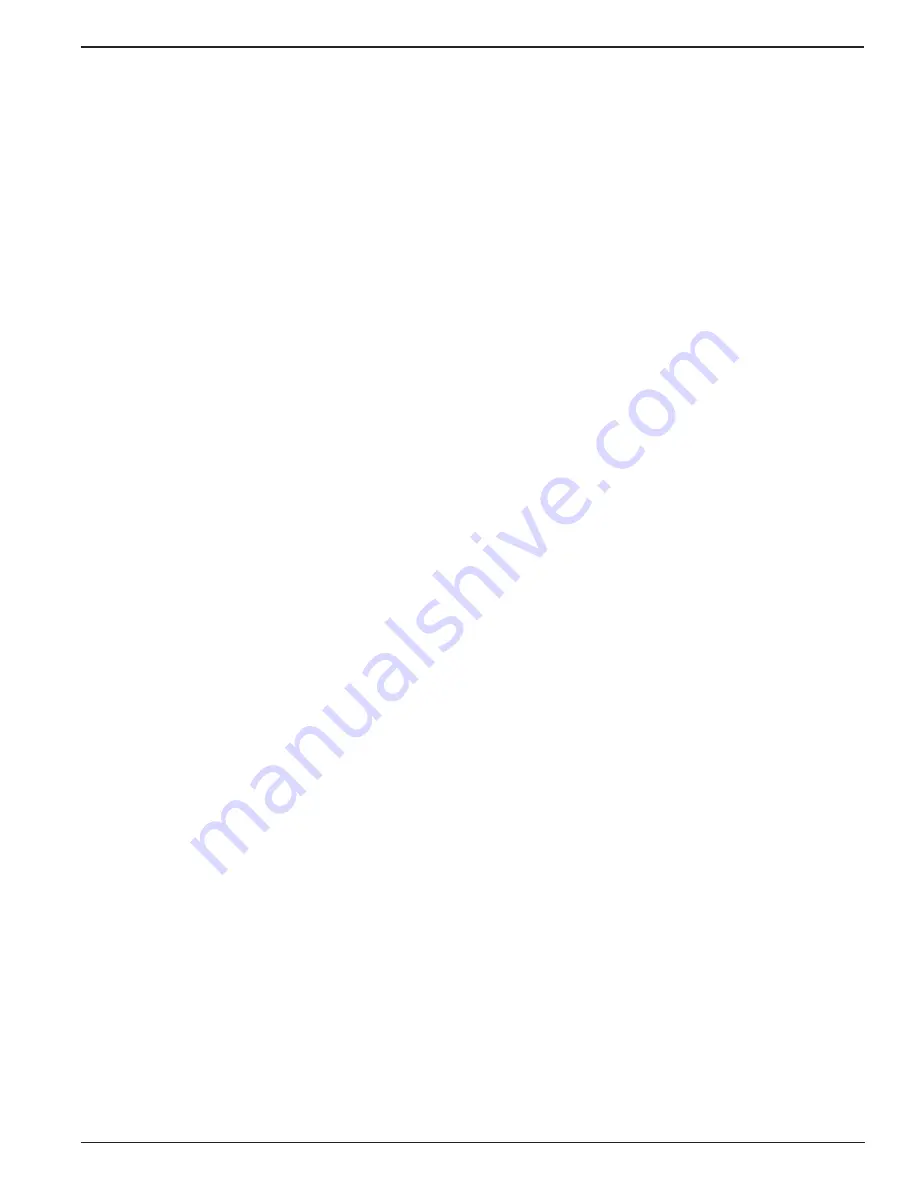
© MMXIX Kirby Morgan Dive Systems, Inc. All rights reserved. Document # 190625006
SF350-1
SuperFlow® 350 Regulator
SuperFlow® 350 Regulator & Exhaust System Post Dive Cleaning & Sanitizing
SuperFlow
®
350 Regulator
Contents
1.6.1 Precautions for Cleaning
1.1 SuperFlow
®
350 Regulator &
Exhaust System Post Dive Cleaning
& Sanitizing
Purpose
This procedure should be performed at comple-
tion of diving operations and/or whenever the
helmet is to be used by another diver.
Tools required:
•
1/4
inch Flat Blade Attachment on Torque
Screwdriver
• Small Phillips Screwdriver
• Clean Wiping Rag
• Nylon Tooth Brush
• Spray Bottle with Mild Dish Soap Solution
• Spray Bottle with Antiseptic Cleaner
1.1.1 Post Dive Disassembly
1) Remove the demand regulator clamp by re-
moving the clamp screw. Lift off the regulator
cover and diaphragm.