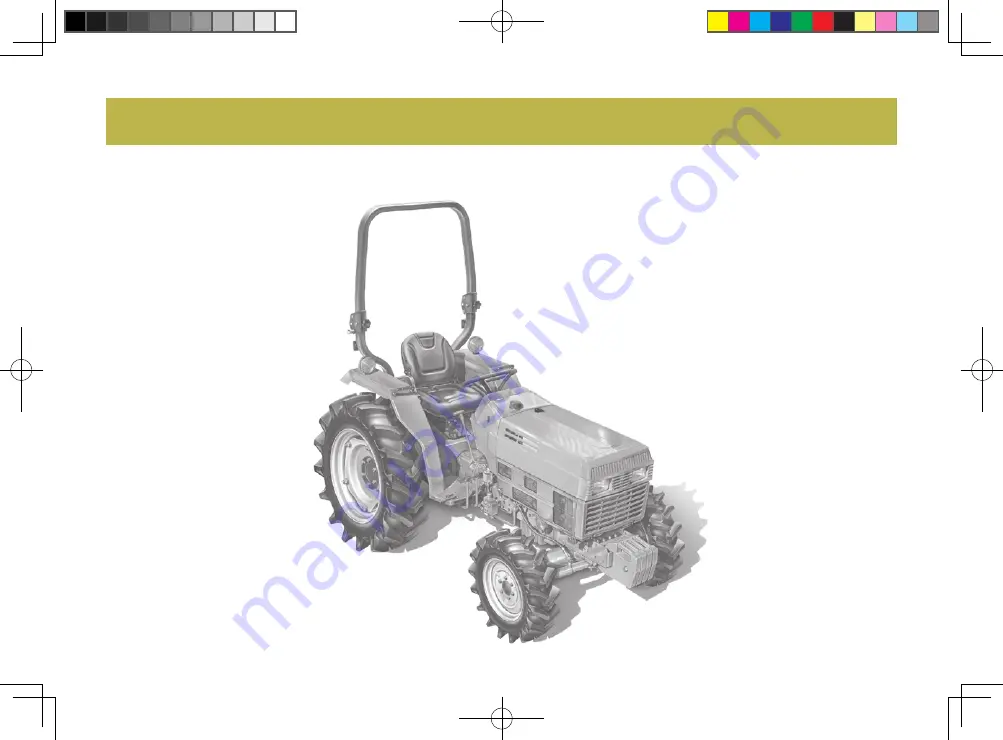
Congratulations, and welcome to the fabulous world of
LK30/LK35
ownership, where serious work is made
fun again!
This versatile tractor is a culmination of the entire tractor and diesel knowledge gained by the Daedong In-
dustrial Co.,LTD since 1947. It has been designed with the finest materials and under rigid quality control
standards set forth by the
KIOTI
Engineering Department.
Knowledge of tractor operation is essential for many years of dependable service and reliability. To help
new owner’s familiarize themselves with the
KIOTI LK30/LK35
, it is the policy of
KIOTI
tractor to provide an
owner’s manual which includes helpful information about tractor safety, operation and maintenance. If the
information you seek is not found in this manual, your
KIOTI
tractor dealer will be happy to help you.
Please feel free to contact
DAEDONG IND. CO.,LTD
with your questions/concerns.
FOREWORD
LK35-AU-00.indd 1
2010-01-20 오후 2:58:34
Summary of Contents for LK30
Page 4: ...LK35 AU 00 indd 4 2010 01 20 2 58 34...
Page 6: ...LK35 AU 00 indd 6 2010 01 20 2 59 22...
Page 8: ...LK35 AU 00 indd 8 2010 01 20 2 58 43...
Page 22: ...1 14 LK30 LK35 S41O131a TRACTOR SAFETY LABELS LK35 AU 01 indd 14 2010 01 20 3 02 55...
Page 25: ...2 servicing 2 2 SERVICING OF TRACTOR 2 LK35 AU 02 indd 1 2010 01 20 3 07 09...
Page 34: ...MEMO MEMO LK35 AU 03 indd 8 2010 01 20 3 10 11...
Page 40: ...MEMO MEMO LK35 AU 04 indd 6 2010 01 20 3 11 25...
Page 76: ...MEMO MEMO LK35 AU 07 indd 6 2010 01 20 3 15 15...
Page 82: ...MEMO MEMO LK35 AU 08 indd 6 2010 01 20 3 16 35...
Page 83: ...9 SERVICE INTERVALS 9 2 LUBRICANTS 9 4 MAINTENANCE 9 LK35 AU 09 indd 1 2010 01 20 3 17 46...
Page 116: ...MEMO MEMO LK35 AU 11 indd 4 2010 01 20 3 24 59...
Page 117: ...12 ENGINE TROUBLE SHOOTING 12 2 TROUBLE SHOOTING 12 LK35 AU 12 indd 1 2010 01 20 3 25 51...
Page 120: ...MEMO MEMO LK35 AU 12 indd 4 2010 01 20 3 25 52...
Page 121: ...13 OPTIONS 13 2 OPTIONS 13 LK35 AU 13 indd 1 2010 01 20 3 26 39...
Page 123: ...INDEX 14 2 14 INDEX 14 LK35 AU 14 indd 1 2010 01 20 3 27 26...