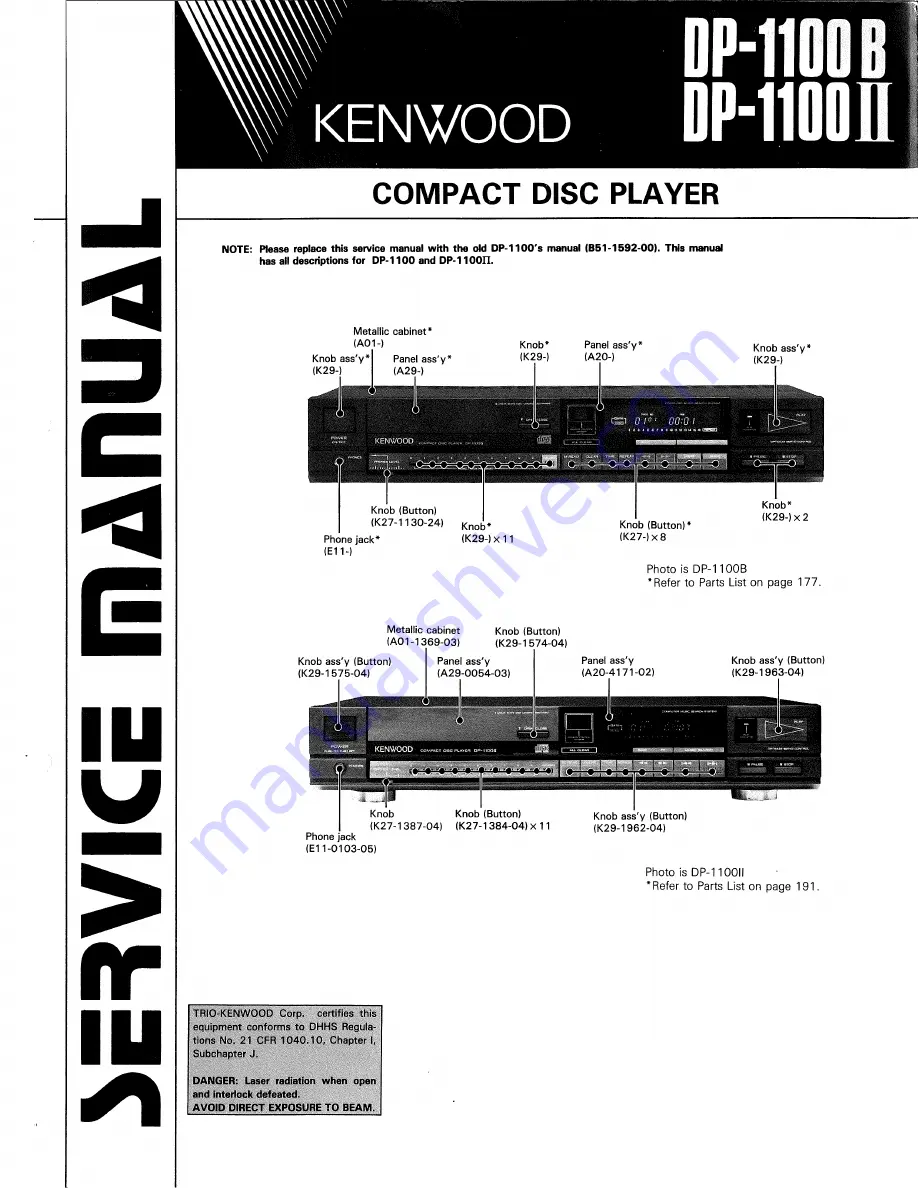
COMPACT DISC PLAYER
NOTE: Please replace this service manual with the old DP-1100's manual (B51-1592-00). This manual
has all descriptions for DP-1100 and DP-110011.
Photo is DP-110011
'Refer to Parts List on page 1 9 1 ,
TRIO-KENWOOD Corp. certifies this
equipment conforms to DHHS Regula
tions No. 21 C F R 1 0 4 0 . 1 0 , Chapter I,
Subchapter J .
DANGER: Laser radiation when open
and interlock defeated.
AVOID DIRECT EXPOSURE TO BEAM.
KENWOOD
DP-1100 B
DP-1100II
Photo is DP-1100B
•Refer to Parts List on page 177.
Summary of Contents for DP-1100 B
Page 3: ...D P 1 1 0 0 B II D P 1 1 0 0 B II I BLOCK DIAGRAM ...
Page 32: ...D P 1 1 0 0 B II 1 CIRCUIT DESCRIPTION Disc Scratch Dust RFES D C O N D O C K Fig 1 2A 3 5 ...
Page 112: ...2 IC OPERATION OF EACH CIRCUIT AND D P 1 1 0 0 B II PIN DESCRIPTION Fig 2 4 1 G 1 ...
Page 117: ...DP 1100B II I OPERATION OF MAIN MICROPROCESSOR Fig 3 1D Q data reading flow chart ...