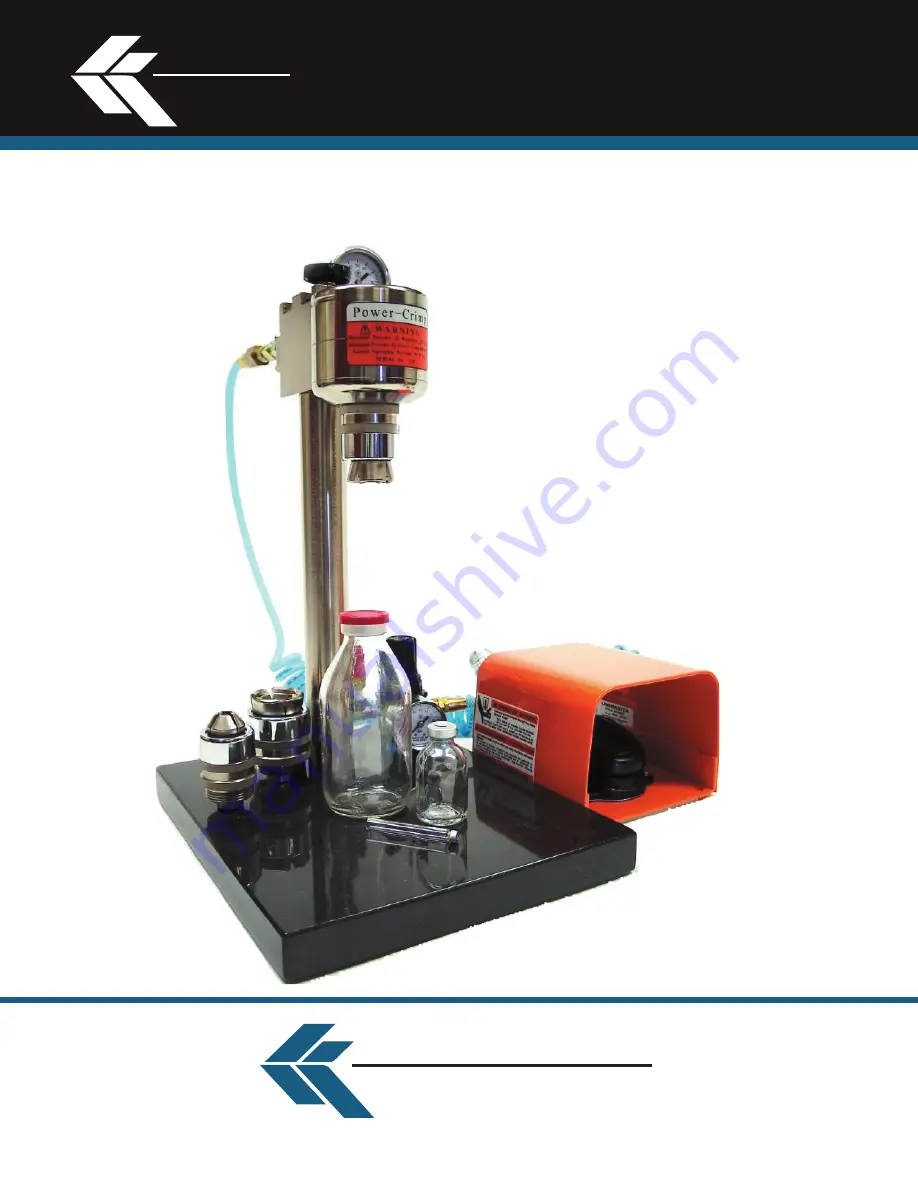
KEBBY
INDUSTRIES
Power
Crimper
& Accessories
Setup and
Operation
Manual
KEBBY INDUSTRIES
4075 Kilburn Ave., Rockford, IL 61101 U.S.A.
Phone: 815-963-1466 • Fax: 815-962-3490
Email: [email protected]
www.kebbyindustries.com
Summary of Contents for A10001
Page 2: ......