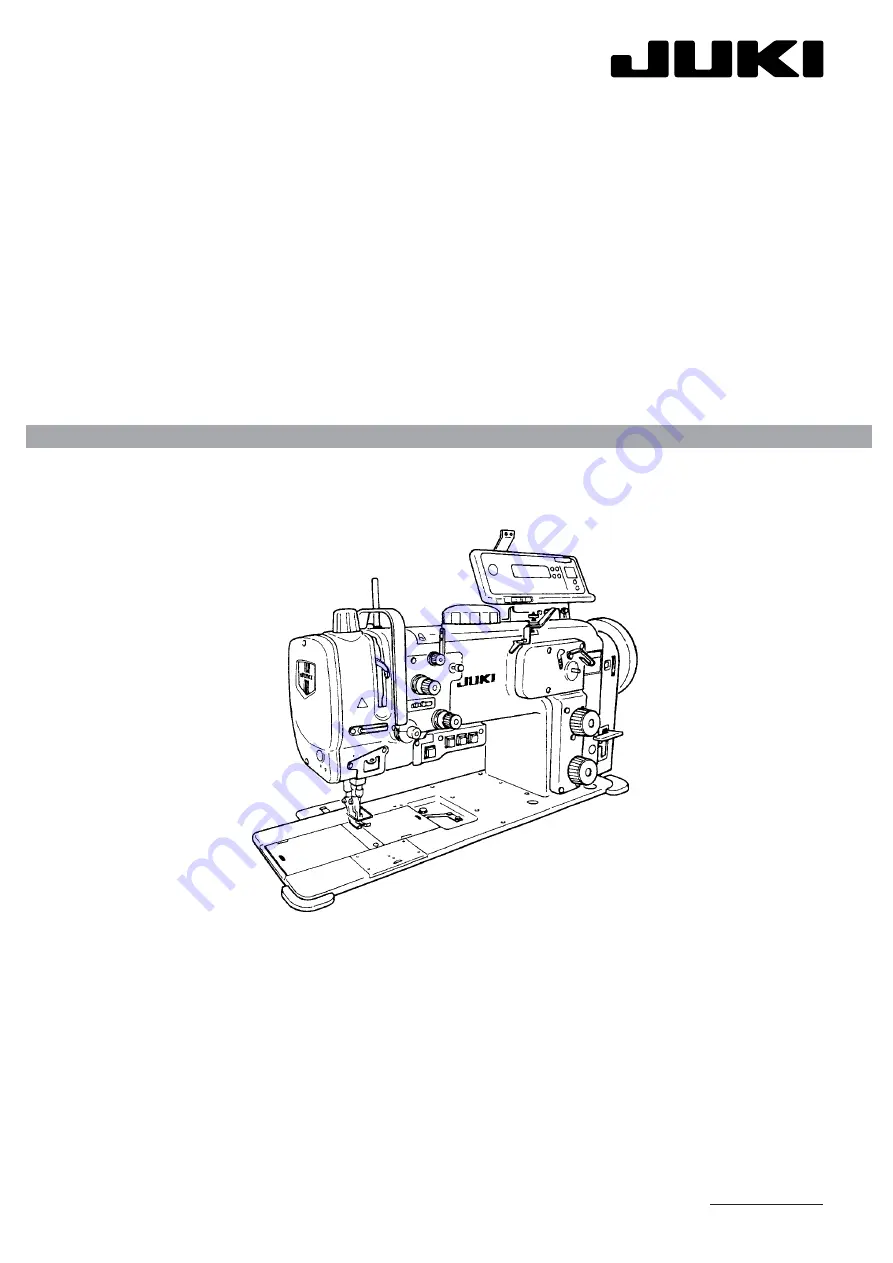
29227501
No.E306-04
ENGINEER’S MANUAL
1-NEEDLE, HIGH-SPEED, UNISON-FEED LOCKSTITCH MACHINE WITH VERTICAL-AXIS LARGE HOOK
AND AUTOMATIC THREAD TRIMMER
LU-2210N-7
LU-2210W-7
®
1- NEEDLE, HIGH-SPEED, UNISON-FEED LOCKSTITCH MACHINE WITH VERTICAL-AXIS LARGE HOOK
AND AUTOMATIC THREAD TRIMMER (2P DIAL)
LU-2212N-7
2- NEEDLE, HIGH-SPEED, UNISON-FEED LOCKSTITCH MACHINE WITH VERTICAL-AXIS LARGE HOOK
AND AUTOMATIC THREAD TRIMMER
LU-2260N-7
LU-2260W-7
1- NEEDLE, HIGH-SPEED, UNISON-FEED LOCKSTITCH MACHINE WITH VERTICAL-AXIS LARGE HOOK
AND AUTOMATIC THREAD TRIMMER (NEEDLE THREAD CLAMP DEVICE/2P DIAL)
LU-2220N-7