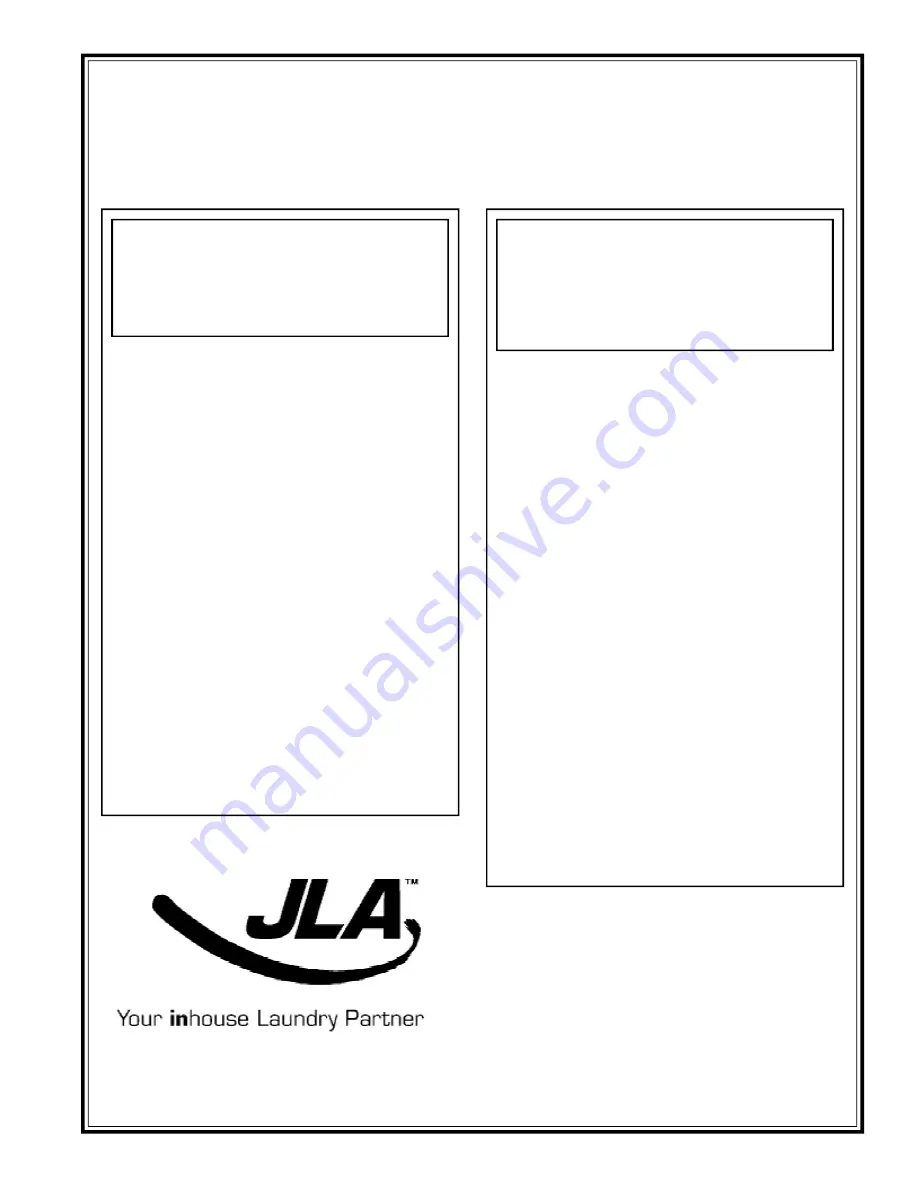
D40 Installation Manual
Phase 7 / Fire Suppression System
JLA Limited
Meadowcroft Lane, Halifax Road
Ripponden
West Yorkshire, England
HX6 4AJ
Telephone: 01422 822282 / Fax: 01422 824390
WARNING: For your safety the information
in this manual must be followed to
minimize the risk of fire or explosion or to
prevent property damage, personal injury
or death.
— Do not store or use gasoline or other
flammable vapors and liquids in the
vicinity of this or any other appliance.
— WHAT TO DO IF YOU SMELL GAS:
• Do not try to light any appliance.
• Do not touch any electrical switch;
do not use any phone in your
building.
• Clear the room, building or area of
all occupants.
• Immediately call your gas supplier
from a neighbor’s phone. Follow
the gas supplier’s instructions.
• If you cannot reach your gas
supplier, call the fire department.
— Installation and service must be
performed by a qualified installer,
service agency or the gas supplier.
AVERTISSEMENT: Assurez-vous de bien
suivre les instructions données dans cette
notice pour réduire au minimum le risque
d’incendie ou d’explosion ou pour éviter
tout dommage matériel, toute blessure ou
la mort.
— Ne pas entreposer ni utiliser d’essence
ni d’autres vapeurs ou liquides
inflammables à proximité de cet
appareil ou de tout autre appareil.
— QUE FAIRE SI VOUS SENTEZ UNE
ODEUR DE GAZ:
• Ne pas tenter d’allumer d’appareils.
• Ne touchez à aucun interrupteur.
Ne pas vous servir des téléphones
se trouvant dans le bâtiment.
• Évacuez la pièce, le bâtiment ou la
zone.
• Appelez immédiatement votre
fournisseur de gaz depuis un voisin.
Suivez les instructions du
fournisseur.
• Si vous ne pouvez rejoindre le
fournisseur de gaz, appelez le
service des incendies.
— L’installation et l’entretien doivent être
assurés par un installateur ou un service
d’entretien qualifié ou par le fournisseur
de gaz.
JLA
Part No. 113242