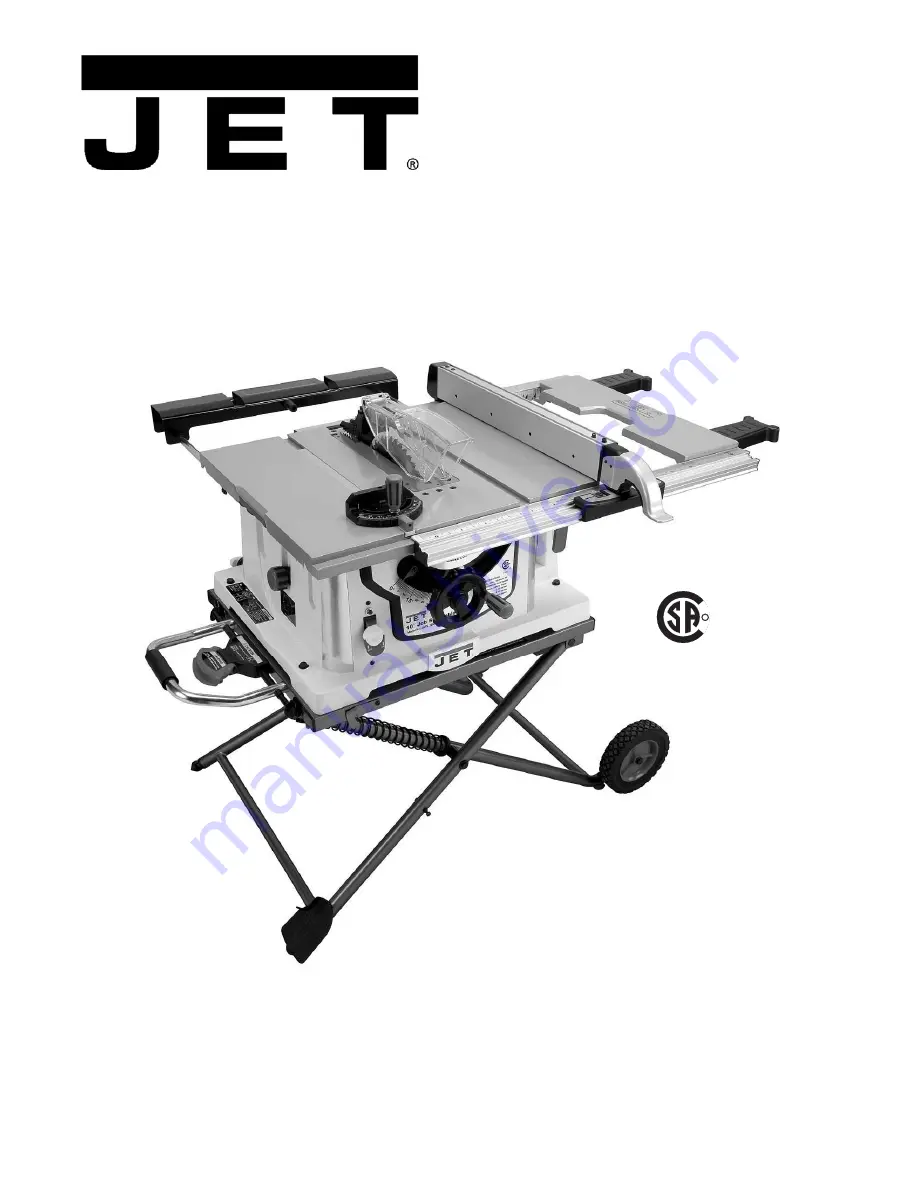
Operating Instructions and Parts Manual
10" Job Site Table Saw
Benchtop Series – Model No. JBTS-10MJS
WALTER MEIER (Manufacturing) Inc.
427 New Sanford Road
LaVergne, Tennessee 37086
Part No. M-707000
Ph.: 800-274-6848
Revision A3 10/2010
www.waltermeier.com
Copyright © 2010 Walter Meier (Manufacturing) Inc.
C
US
R
174315