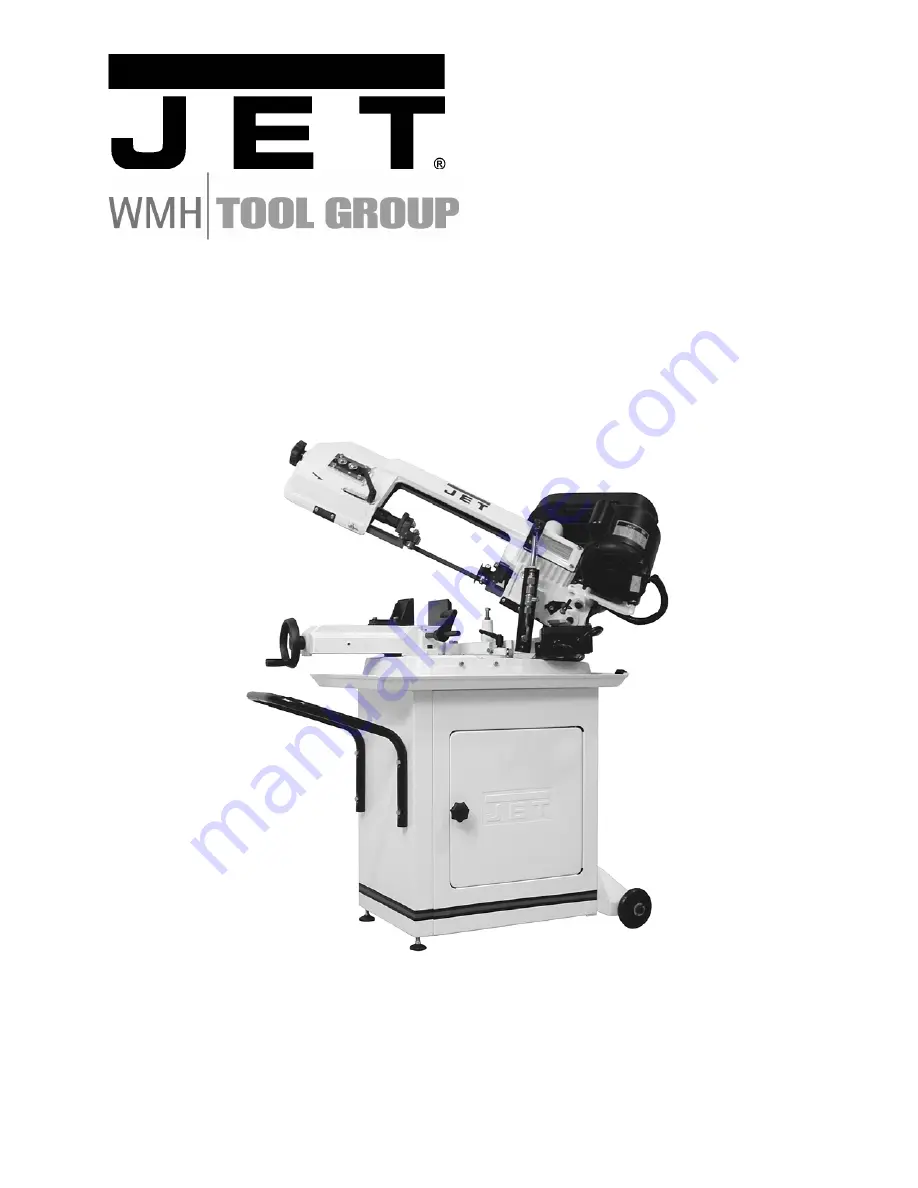
Operating Instructions and Parts Manual
5 x 6-inch Horizontal Band Saw
Model HBS-56S
For use with machines with Serial Numbers 06080307 and higher
WMH TOOL GROUP
2420 Vantage Drive
Elgin, Illinois 60124
Part No. M-414457A
Ph.: 800-274-6848
Revision B 9/06
www.wmhtoolgroup.com
Copyright © WMH Tool Group
Summary of Contents for HBS-56S
Page 25: ...25 Bow Assembly Page 2 of 3 97 1 2 ...
Page 26: ...26 Bow Assembly Page 3 of 3 ...
Page 27: ...27 Base and Cabinet Assembly ...