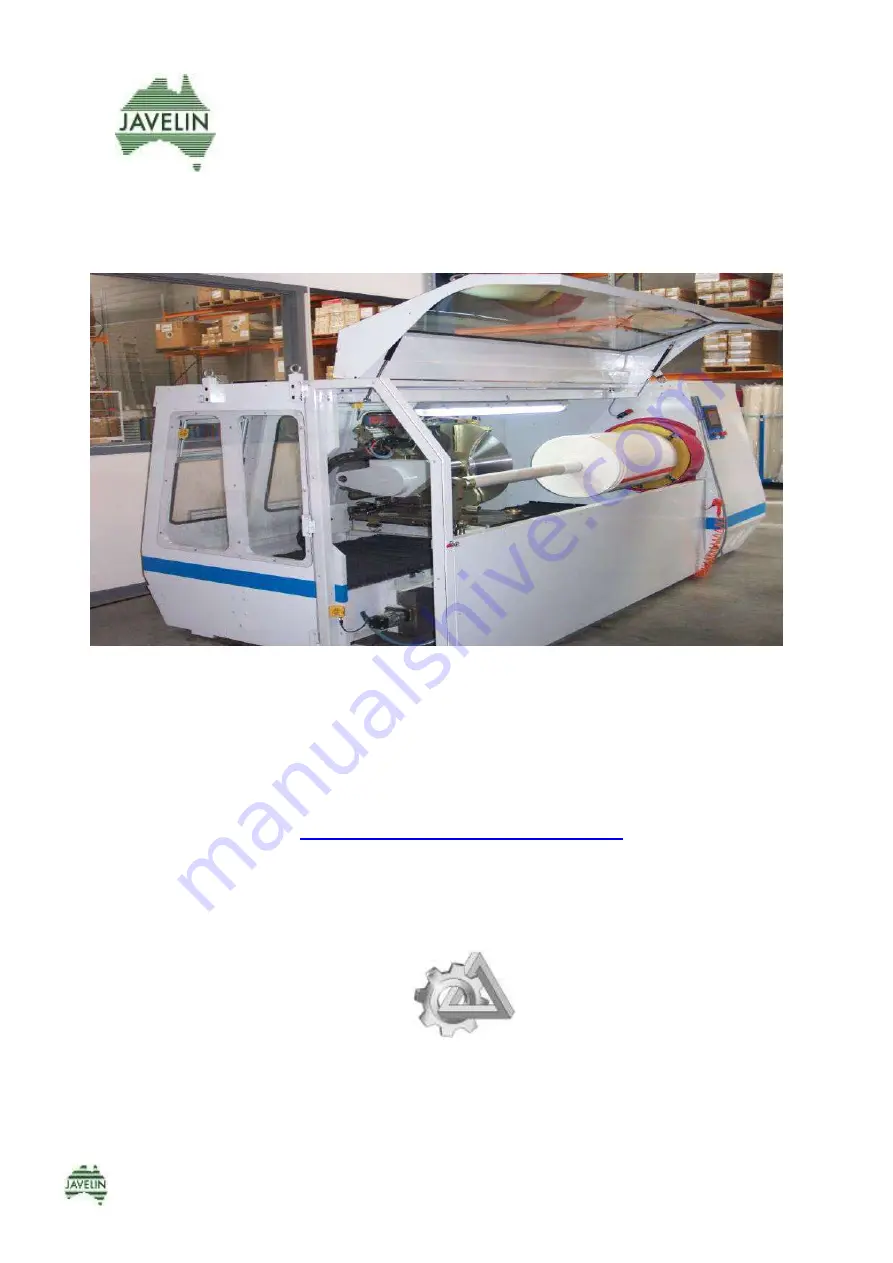
________________________________________________________________________________________________________________________________________________________________
CN3600 Setup & Operation Manual Revision : 6/2020
1
CN3600
CN3600 Setup & Operation Manual
Contents of this manual are © 2020
Javelin Machinery
by Industrial Electrical Solutions PTY LTD
18/167 Princes Hwy, Hallam, Victoria, Australia 3803
Phone 0466 232783