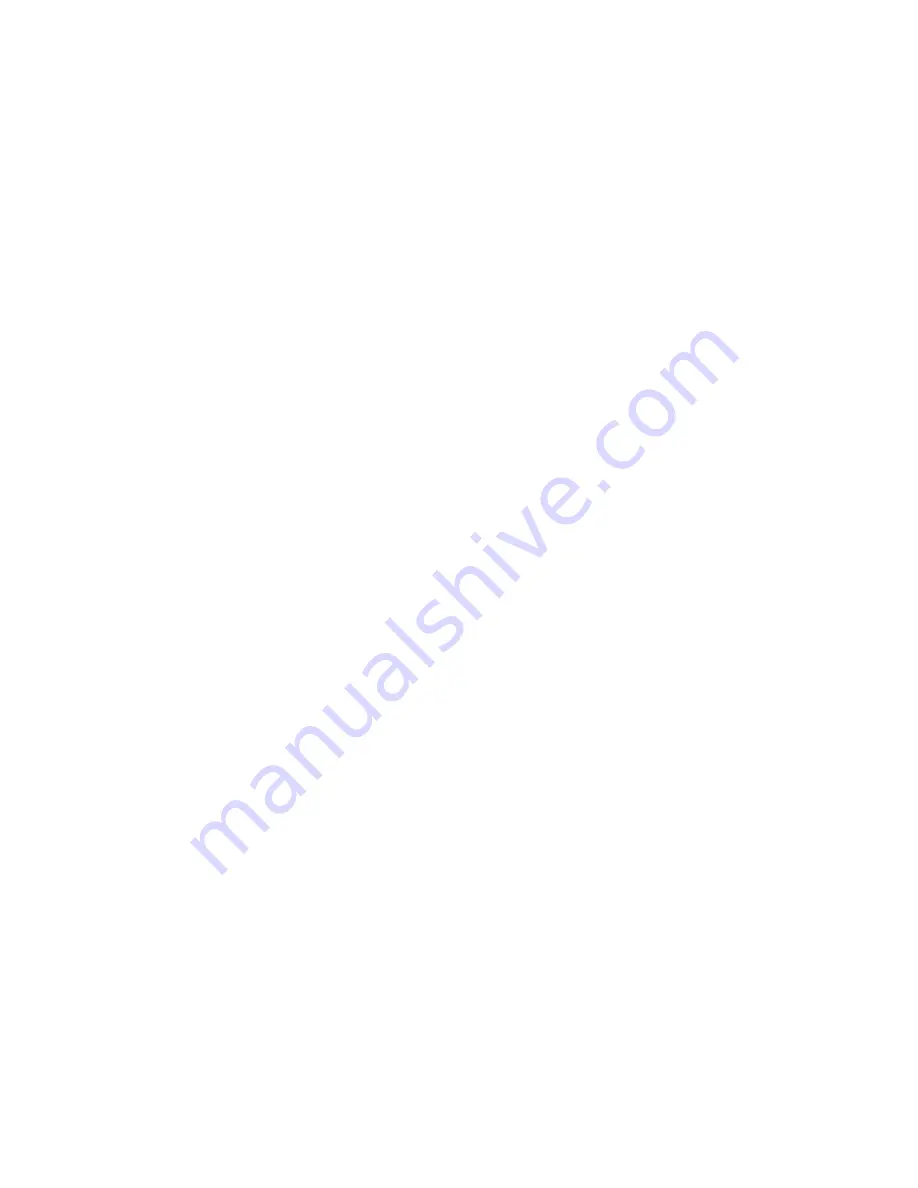
QMP16SU Service Manual
| 1
Contents
About the Janome QMP16SU .............................................................................................................2
About This Manual ..................................................................................................................................... 2
Service Manual Guidelines..................................................................................................................... 2
1. General Specifications
....................................................................................................................4
Assembly Torque Specifications ................................................................................................................. 5
3. Preparing to Service ........................................................................................................................6
Electrostatic Discharge (ESD) Precautions.............................................................................................. 6
Remove the Front Cover, Control board, and Power Supply ..................................................................7
Reassemble the Machine Following Service .......................................................................................... 9
Control Board Connections .................................................................................................................. 10
Main Shaft Encoder, Motor Driver Board, and Motor Connections .....................................................11
QMP16Su Cables...................................................................................................................................12
4. Lubrication
................................................................................................................................... 16
5. General Checks and Adjustments
.................................................................................................. 19
Thread Mast ......................................................................................................................................... 20
Hand Wheel ......................................................................................................................................... 20
Thread Guides ...................................................................................................................................... 20
Top Tension Assembly .......................................................................................................................... 21
Check and Secure Flats and Screws..................................................................................................... 24
Brass Counterweight Timing.................................................................................................................26
Check and Adjust Axial Play ................................................................................................................. 27
Check the Base-Plate Wheels............................................................................................................... 29
Check Motor Drive/Timing Belt Tension .............................................................................................. 30
Adjusting the Hopping Foot Adapter ................................................................................................... 32
Adjusting the Presser Bar Height (Internal Adjustment) ......................................................................33
Needle Position, Check, and Adjustment ............................................................................................. 34
6. Timing Adjustments
...................................................................................................................... 36
Visual Timing Check..............................................................................................................................36
Loop Lift and Needle distance Adjustment .......................................................................................... 39
Adjusting the Needle Height ................................................................................................................ 44
Stop-Finger Adjustment ....................................................................................................................... 46
Adjusting the Needle Height with Cylinder Tool .................................................................................. 47
7. Machine Electronics
...................................................................................................................... 50
Speed/Needle Position Sensor..............................................................................................................50
Indications of Speed/Needle Position Sensor Failure ..........................................................................51
Fuse and Power Supply ........................................................................................................................ 52
Power Supply “Chirping” ..................................................................................................................... 53
LED Identification ................................................................................................................................. 54
Control Pod Power LED ........................................................................................................................ 55
Display Communications LEDs ............................................................................................................. 56
LED Light Ring Information .................................................................................................................. 57
Round Tooth (RT) Belt .......................................................................................................................... 58
Electrical Notes Janome QMP16SU ..................................................................................................... 59
8. Janome QMP16SU Screens
...................................................................................................... .62
Diagnostics
.
...........................................................................................................................................63