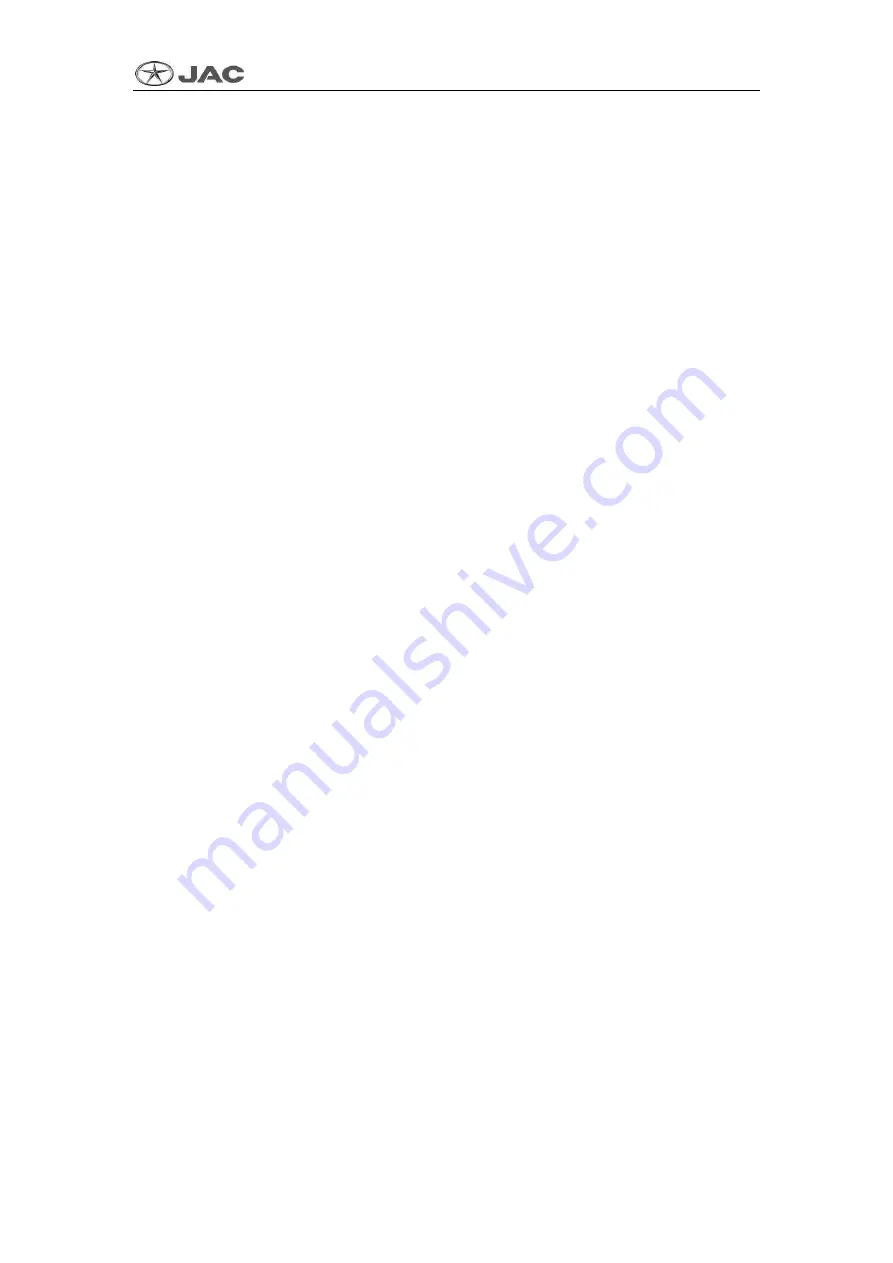
S5 Workshop Manual
Engine
EM-1
Engine
EM Engine Structure
Precautions
Precaution for Draining Engine Coolant:
■ Drain engine coolant after the engine is in cooling condition.
Precautions for Disconnecting Fuel Pipe:
■ Before starting to work
, make sure there is no article which may cause combustion
or spark in working area.
■ Before disconnecting and dismantling, first release fuel pressure. For methods to
release fuel pressure, please refer to "the release of fuel pressure in fuel pipe".
■ After disconnecting pipe, plug the opening to a
void fuel leakage.
Precaution of Dismantling and Disassembly:
■ If it is required to use special repair tools, please use special repair tools. Always
keep safe operation, and do not force to do or conduct improper operation.
■
Be careful not to damage the matching surface or sliding surface.
■ If necessary, use
adhesive tape or equivalent to seal the opening of engine system,
to avoid foreign matters from entering.
■
Methodically mark and arrange the dismantled parts, to facilitate troubleshooting
and re-assembly.
■ The basic principles for loosening bolts and nuts are to loosen the exterior first, and
then loosen the diagonal position, and so on. If the loosening sequence is specified,
please follow the specified sequence.
Precaution of Inspection, Repair and Replacement:
■ Before repairing or replacing, completely inspect parts. Use the same methods to
inspect the replaced parts. If necessary, please replace.
Precaution of Assembly and Installation:
■ The basic principles for tightening bolts and nuts are
to first tighten middle with the
same tightening torque, and then tighten exterior diagonal position. If the tightening
sequence is specified, please follow the specified sequence.
■ Cushion, oil seal or rubber sealing ring are easy to be damaged during di
smantling.
If necessary, replace them.
■ Completely flush, clean and blow each part to dry condition. Carefully inspect
whether engine oil or engine coolant pipe is blocked.
■ When refilling engine coolant after drain it out, it is necessary to release air
from
pipe.
■ After repairing, start the engine and increase engine rotation speed to inspect
whether the engine coolant, fuel, engine oil and tail gas have leakage.
www.CarGeek.ir