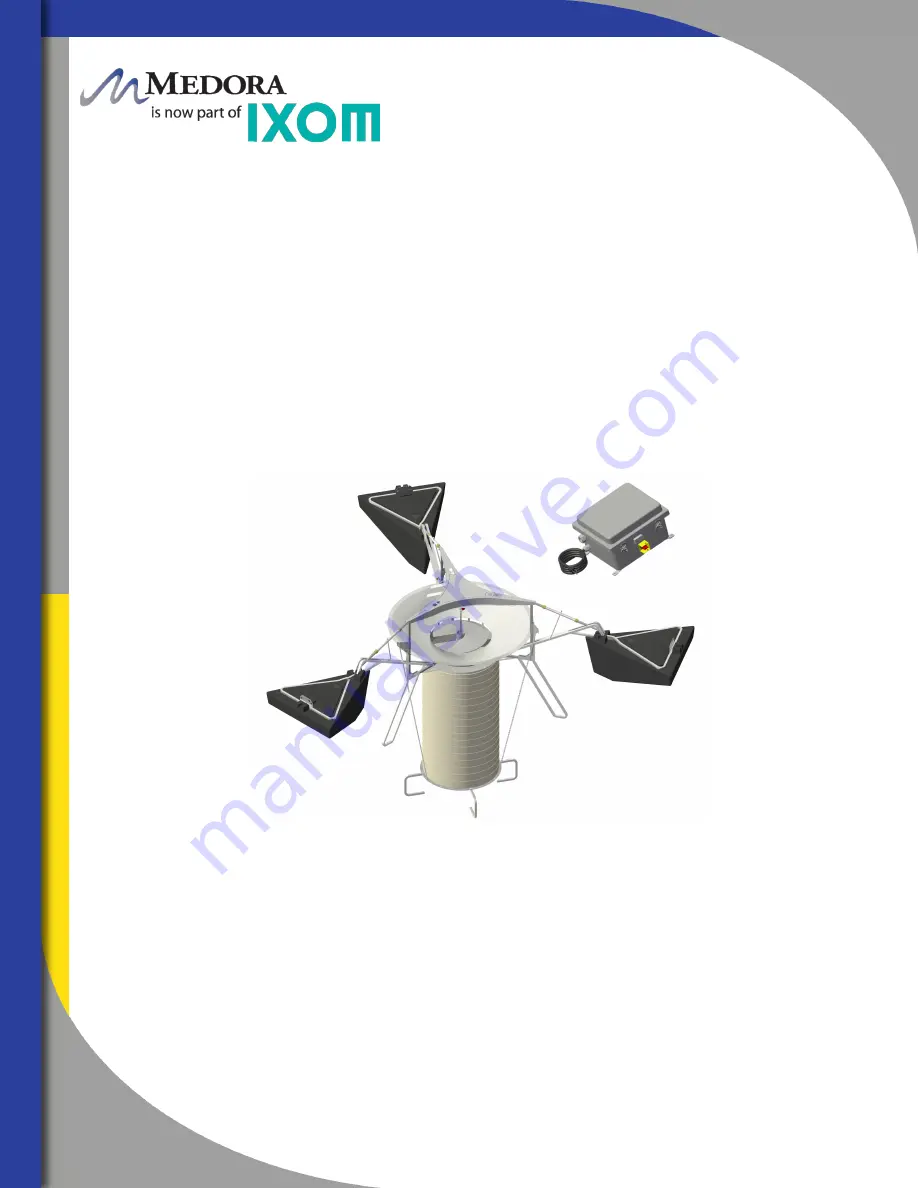
© 2020 Ixom | www.medoraco.com | 866 - 437 - 8076 | [email protected]
O&M_GF10000PW_10499_20200615
GridBee GF10000PW
Owner's Manual
© 2020 Ixom | www.medoraco.com | 866 - 437 - 8076 | [email protected]
O&M_GF10000PW_10499_20200615
GridBee GF10000PW
Owner's Manual