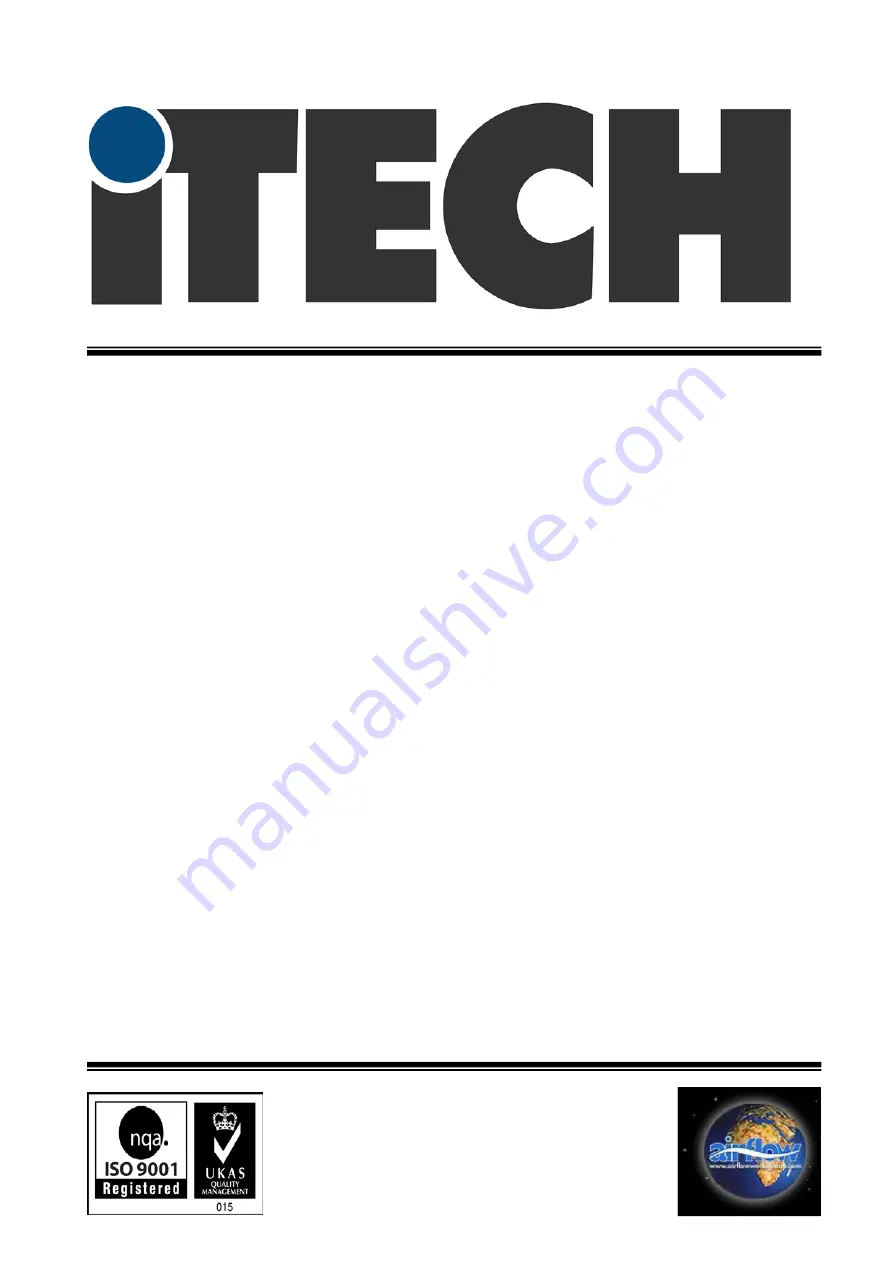
DRY FILTER
SPRAYBOOTH
INSTALLATION &
MAINTENANCE
INSTRUCTIONS
Scott+Sargeant Woodworking
Machinery Ltd
1 Blatchford Road, Horsham, West
Sussex RH13 5QR
ENGLAND
Tel +44 (0) 1403 273000
W b
DRY FILTER
SPRAYBOOTH
INSTALLATION &
MAINTENANCE
INSTRUCTIONS
Scott+Sargeant Woodworking
Machinery Ltd
1 Blatchford Road, Horsham, West
Sussex RH13 5QR
ENGLAND
Tel +44 (0) 1403 273000
W b