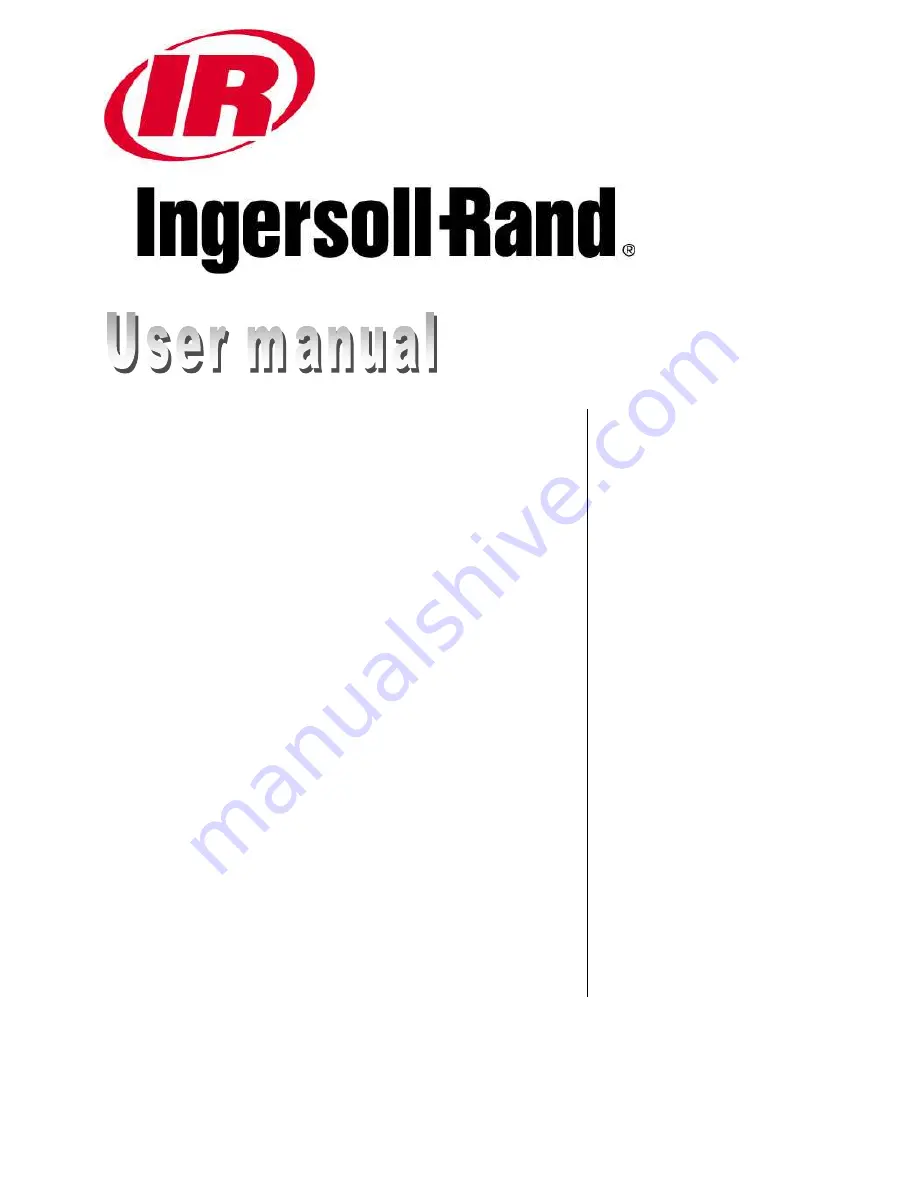
SERIES HC
Heat-of-Compression
Compressed Air Dryer
Models HC-3 – HC-239
IMPORTANT! BEFORE INSTALLING AND
OPERATING THE DRYER, IT IS
RECOMMENDED THAT THIS
MANUAL BE STUDIED AND
CLEARLY UNDERSTOOD.
THIS DRYER IS DESIGNED TO BE
USED ONLY WITH A NON-
LUBRICATED COMPRESSOR. USE
WITH A LUBRICATED
COMPRESSOR WILL VOID ALL
WARRANTIES AND MAY CAUSE
SEVERE DAMAGE.
Information
When making inquiries,
please provide the following
information:
1) Equipment Model Number
2) Equipment Serial Number
3) Equipment Operating
Pressure
4) Equipment Operating
Temperature
5) Approximate time in
service
6) Nature of Problem
For information, parts,
or service, contact your
local
I
I
n
n
g
g
e
e
r
r
s
s
o
o
l
l
l
l
-
-
R
R
a
a
n
n
d
d
Service
provider or
reach us at
www.air.irco.com