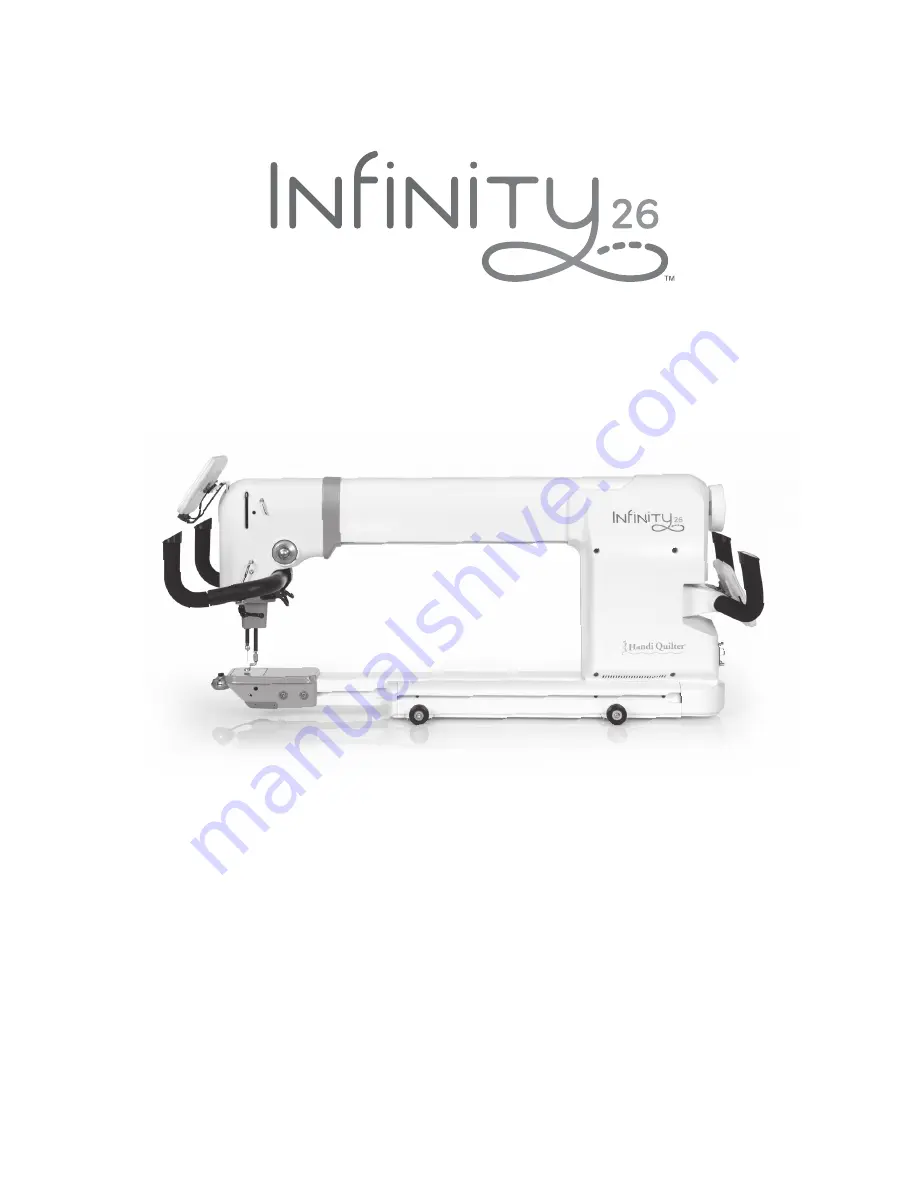
© 2015 Handi Quilter, Inc. All rights reserved.
The information contained in this document is subject to change without notice. If you find any problems
in the manual, please report them to us in writing. This document is not warranted to be error-free.
Handi Quilter, Inc. assumes no responsibility or liability for any errors or inaccuracies that may appear in
the informational content contained in this manual.
Handi Quilter, HQ Infinity, HQ Avanté, HQ Fusion, HQ Sixteen, HQ Sweet Sixteen, HQ Pro-Stitcher, and
TruStitch are either trademarks or registered trademarks of Handi Quilter, Inc.
Printed in the United States of America.
Part number: QM40275
04/01/2015
SERVICE MANUAL
QM40275 • APRIL 1, 2015