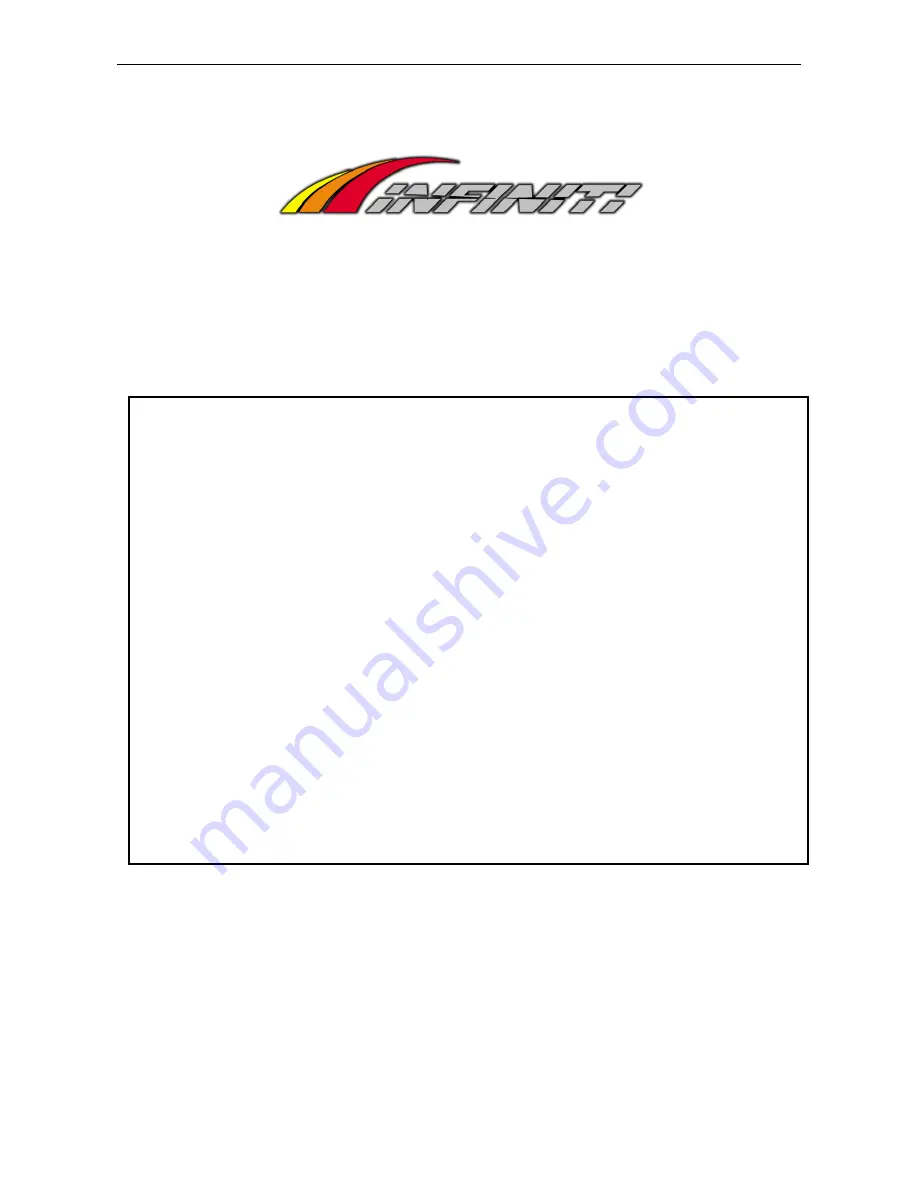
FY operation manual
- 1 -
Operation Manual
6250LQ
Thank you very much for purchasing
INFINITI
In order to use
INFINITI
correctly and safely and understand this product’s capability, please
read this manual carefully.
The manual includes equipment structure, description, technical parameters, operation manual,
safety information, application of software, etc.
Subject to change without notice.
We tried our best to edit this manual and test our machine before market; however, we do not
guaranty errors existing. Please inform us if you find any.
All copyrights are reserved. Any violation to the copyright may cause lawsuit.
Version 1.5
September 25, 2003