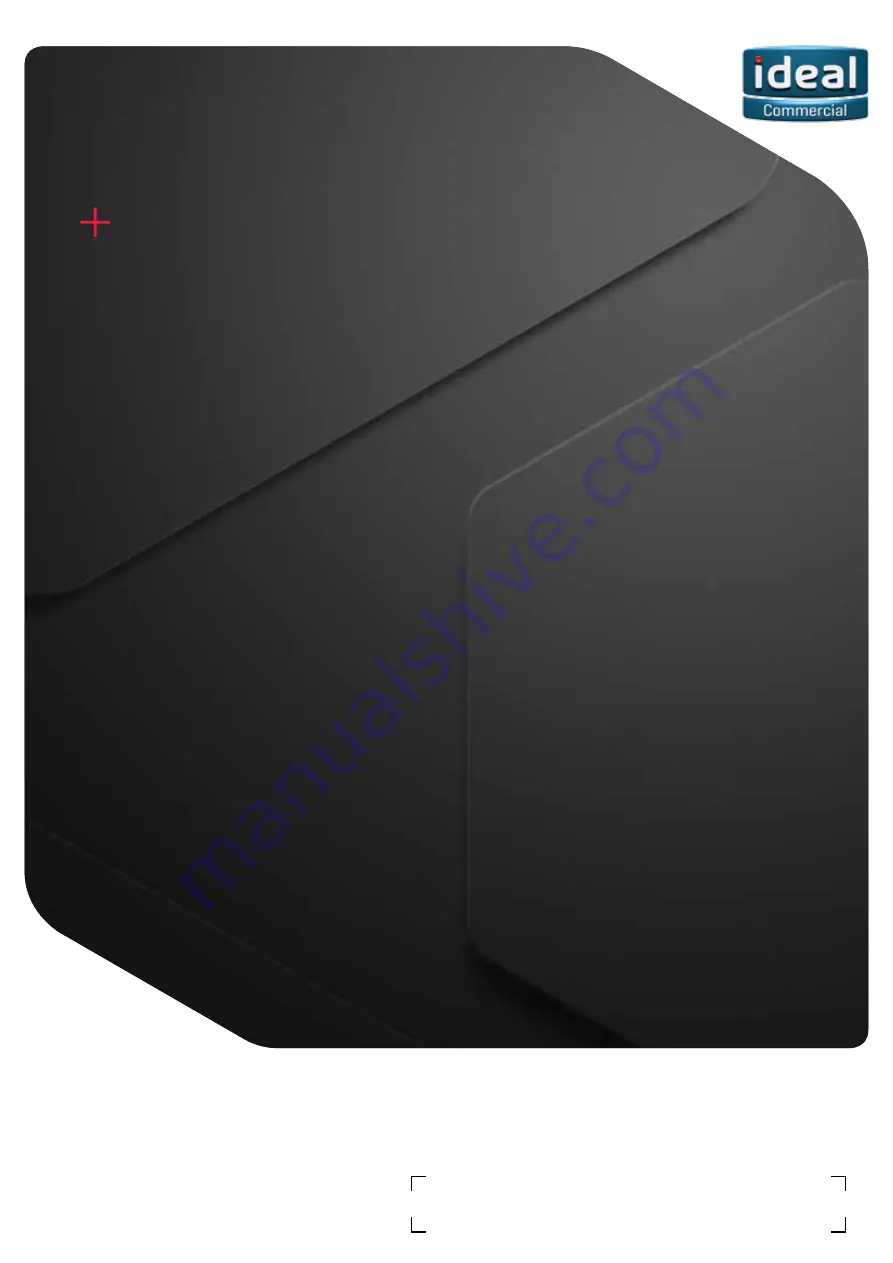
300014485-001-C
January 2016
UIN 203620 A04
INSTALLATION
AND SERVICING
HARRIER
GTS
5 - 9
When replacing any part on this appliance, use only spare parts that you can be
assured conform to the safety and performance specification that we require.
Do not use reconditioned or copy parts that have not been clearly authorised by Ideal.
For the very latest copy of literature for specification and maintenance practices visit our website
www.idealcommercialboilers.com where you can download the relevant information in PDF format.