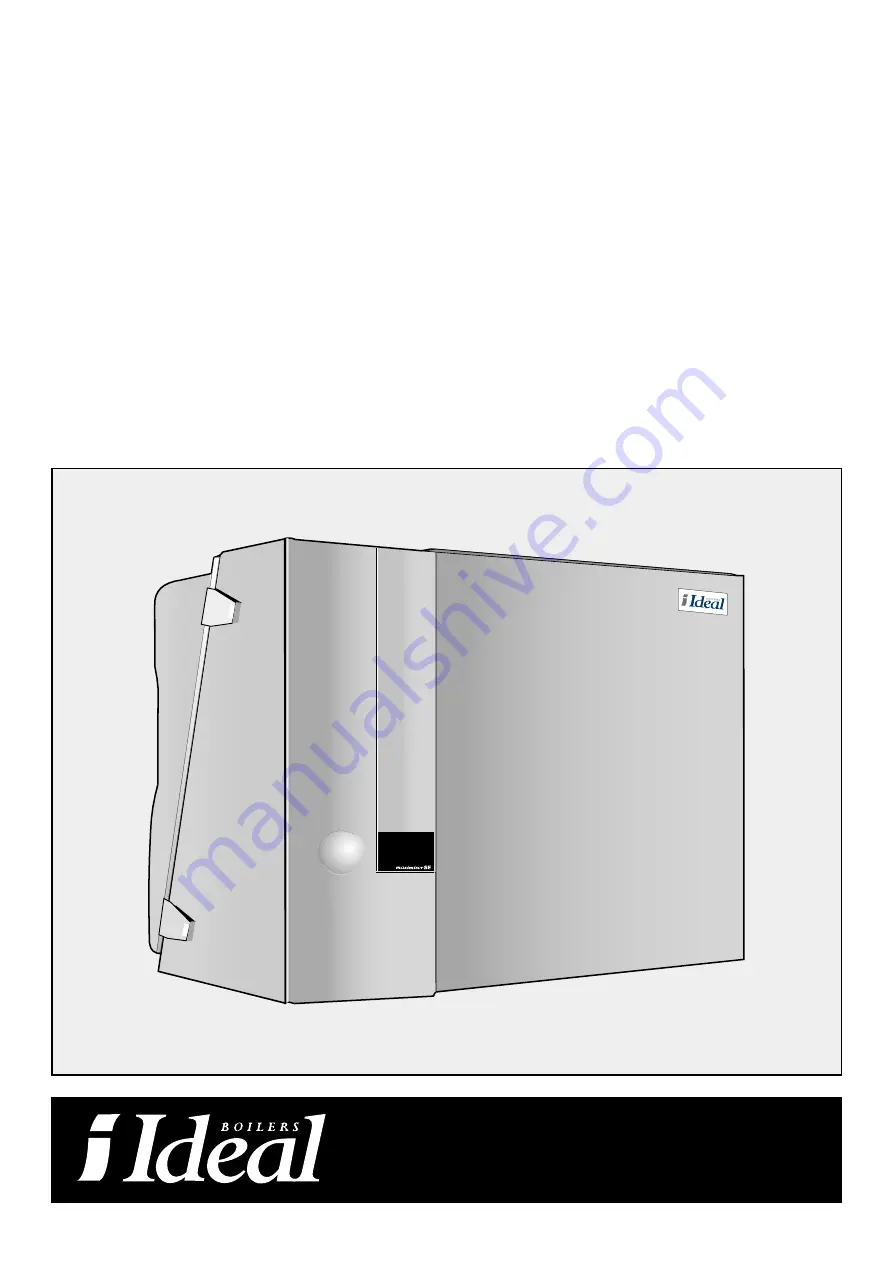
Maximiser SE 42 & SE 65
Installation & Servicing instructions
Wall Mounted, Fanned, Super Efficient Gas Boilers
Natural Gas Models Only
Maximiser SE 42
G.C. Appliance No. 41-349-85
Maximiser SE 65
G.C. Appliance No. 41-349-86
CAUTION.
To avoid the possibility of injury during the installation, servicing or cleaning of this
appliance care should be taken when handling edges of sheet steel components.