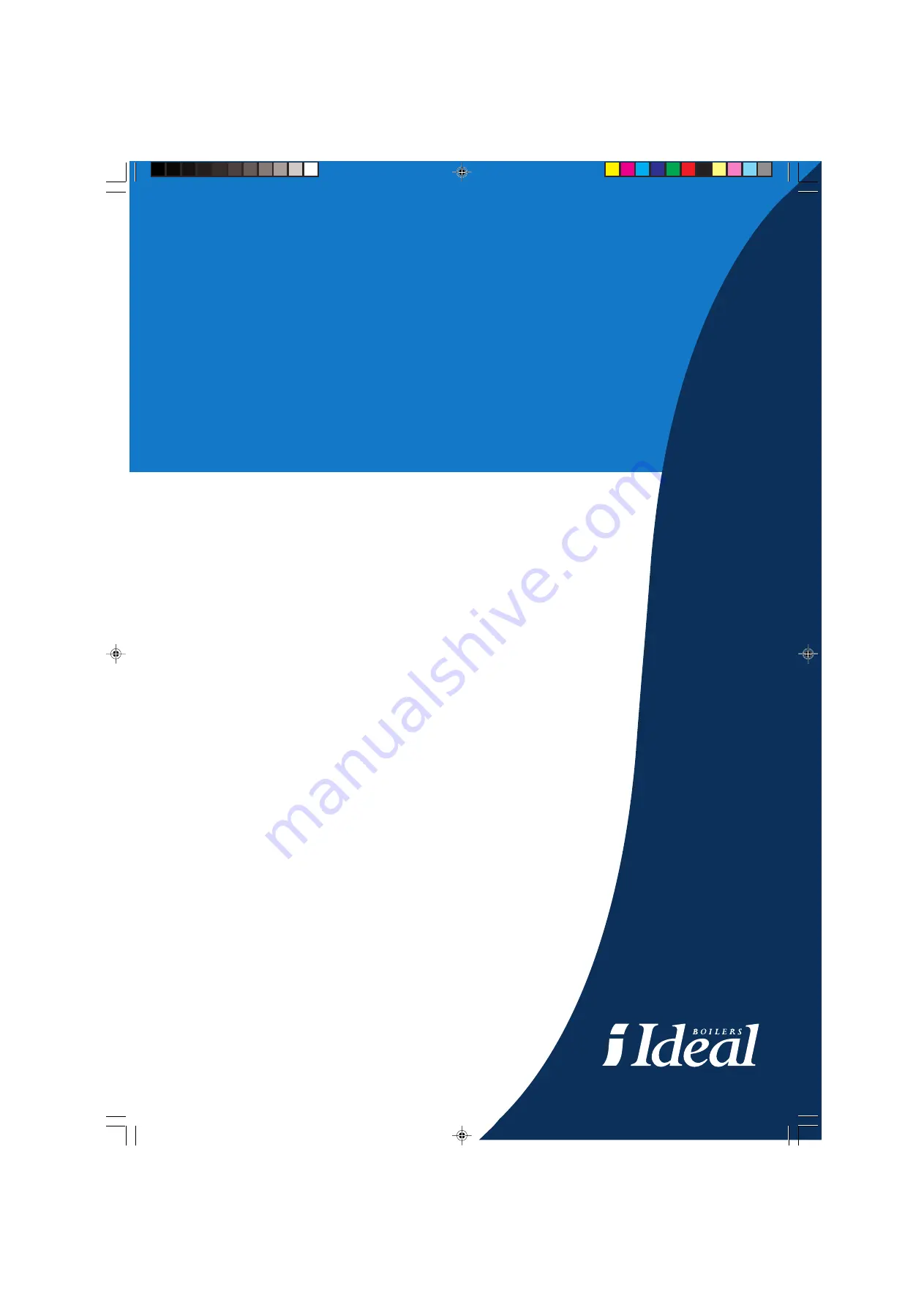
installation and
servicing
istor
Your Ideal installation and servicing guide
ENGINEERED FOR PEACE OF MIND
When replacing any part on this appliance, use only spare parts that you can be
assured conform to the safety and performance specification that we require. Do not
use reconditioned or copy parts that have not been clearly authorised by Ideal Boilers.
HE260 & HE325
For user guide see reverse of book
For the very latest copy of literature for specification purposes please visit our website
www.idealboilers.com where you will be able to download the relevant information in pdf format.
For details of document amendments, refer to page 3
July 2005 UIN 159 979 A07
159979-7.pmd
7/14/2005, 12:44 PM
1
Summary of Contents for istor HE260
Page 2: ...2 istor system store Installation and Servicing 159979 7 pmd 7 14 2005 12 44 PM 2 ...
Page 65: ...65 istor system store Installation and Servicing NOTES 159979 7 pmd 7 14 2005 12 46 PM 65 ...
Page 66: ...66 istor system store Installation and Servicing NOTES 159979 7 pmd 7 14 2005 12 46 PM 66 ...