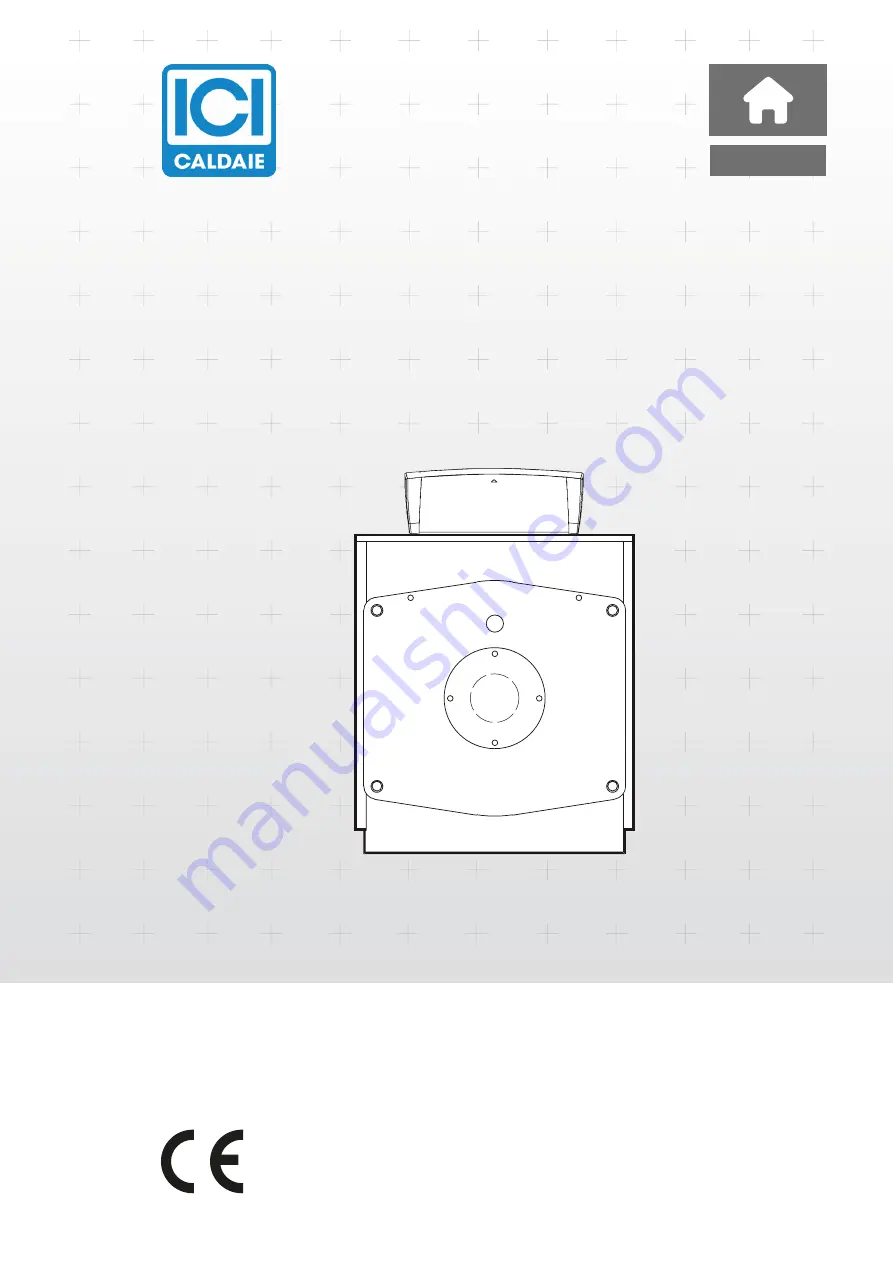
REX_7_130_en_04 - 03/2020
EN
PRESSURISED STEEL BOILERS
REX 7 ÷ 130
INSTALLATION, USE AND MAINTENANCE MANUAL
Cooke Industries - Phone: +64 9 579 2185 Email: [email protected] Web: www.cookeindustries.co.nz
REX_7_130_en_04 - 03/2020
EN
PRESSURISED STEEL BOILERS
REX 7 ÷ 130
INSTALLATION, USE AND MAINTENANCE MANUAL
Cooke Industries - Phone: +64 9 579 2185 Email: [email protected] Web: www.cookeindustries.co.nz