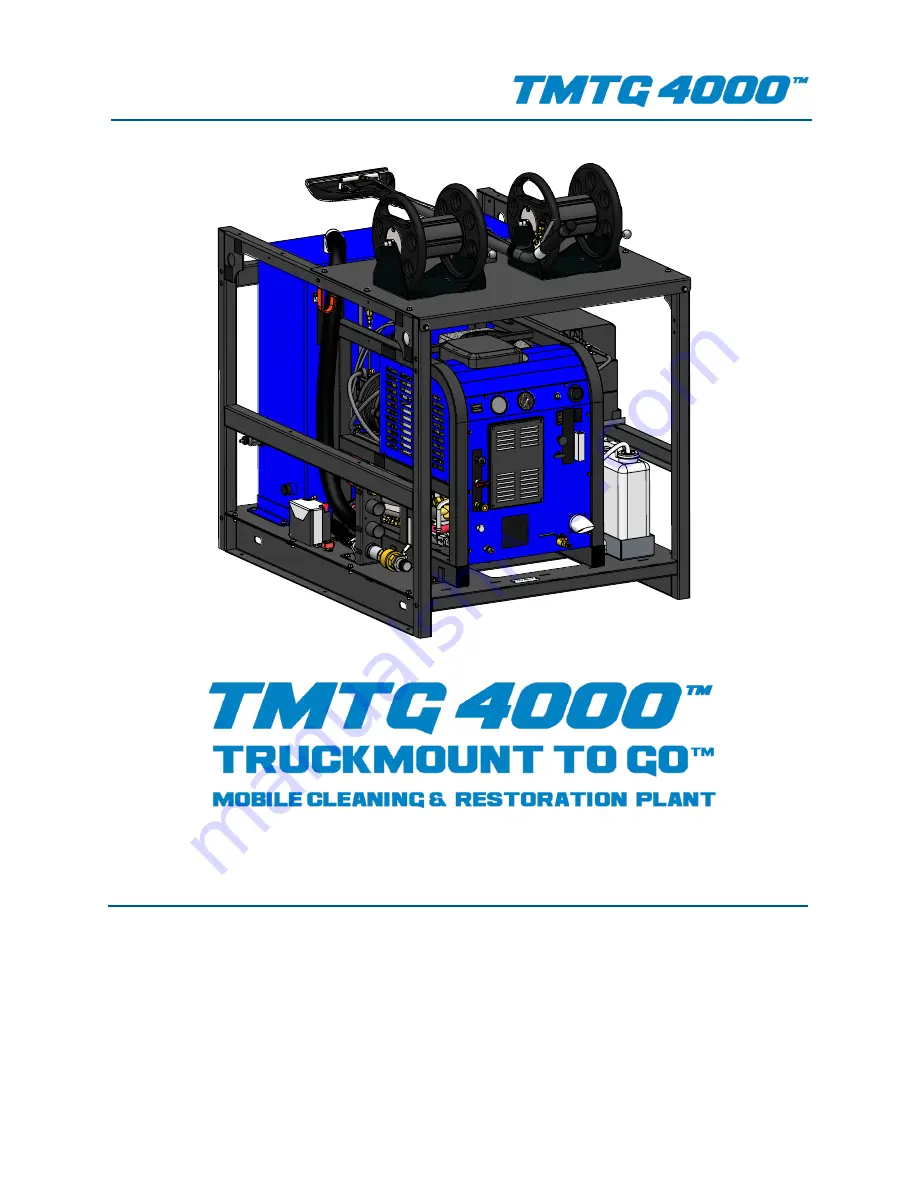
Owner’s Manual
HydraMaster
11015 47
th
Avenue West
Mukilteo, Washington 98275
MAN-47717 Rev. A, June 2019
No part of this manual may be reproduced or used in any form or by any means (i.e. graphic, electronic, photocopying or electronic
retrieval systems) without the express written permission of HydraMaster. Specifications and information in this document are
subject to change without prior notice. All rights reserved. © 2019 HydraMaster
Summary of Contents for Truckmount to Go TMTG 4000
Page 2: ......
Page 5: ...iii TMTG 4000 Owner s Manual ...
Page 31: ...3 5 Cleaning Information ...
Page 33: ...3 7 Cleaning Information 16 2 Evolution Flood Wand Item 000 163 058 Only 6 8 lbs ...
Page 58: ...6 3 Water and Chemical System Figure 6 1 Flow Diagram View 1 of 3 000 179 038 Rev A ...
Page 59: ...Water and Chemical System 6 4 Figure 6 2 Flow Diagram View 2 of 3 000 179 038 Rev A ...
Page 124: ......