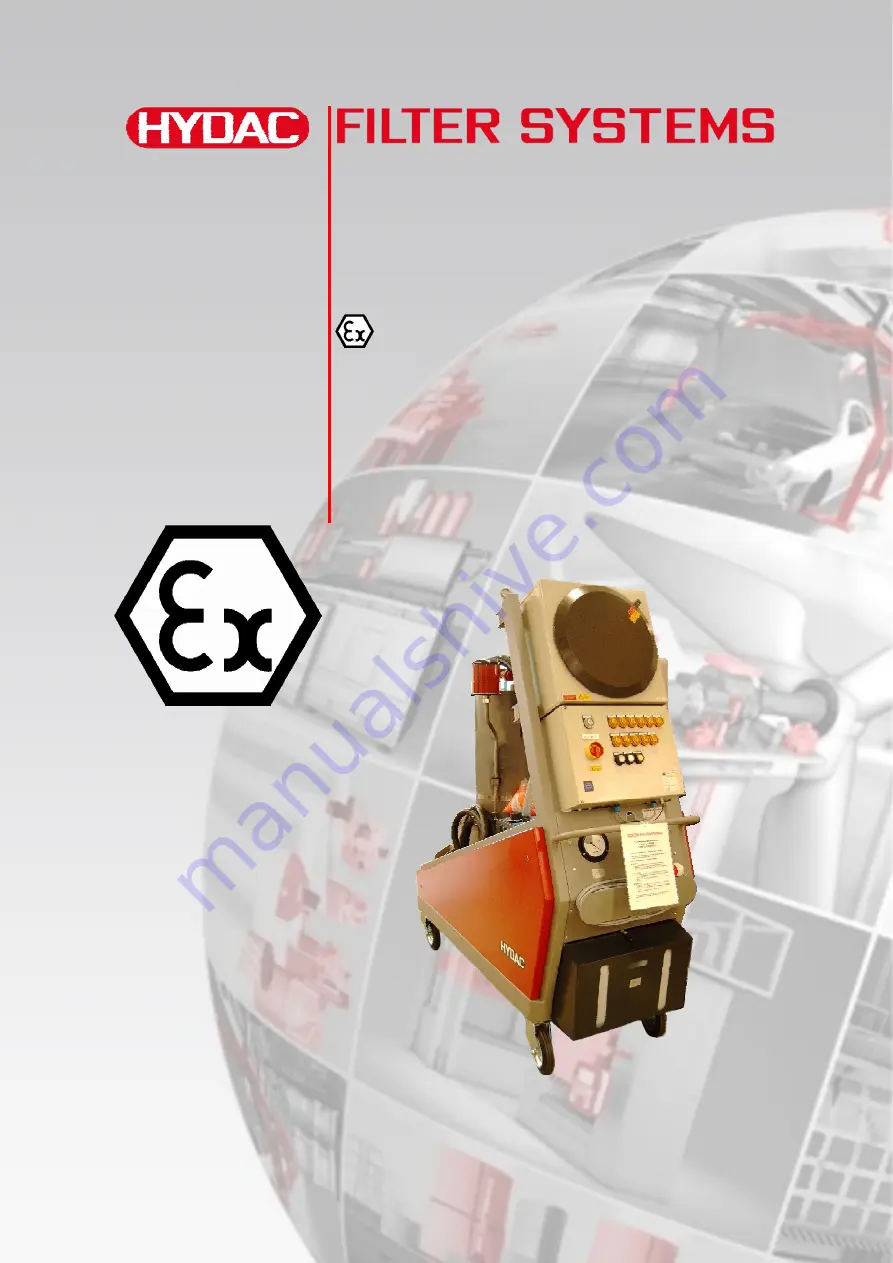
FluidAqua Mobil
FAM 15/30/50/70 ATEX
II 2G IIB3 T4 (+10°C<Ta<40°C)
Operating and Maintenance Instructions
E
E
n
n
g
g
l
l
i
i
s
s
h
h
(
(
t
t
r
r
a
a
n
n
s
s
l
l
a
a
t
t
i
i
o
o
n
n
o
o
f
f
o
o
r
r
i
i
g
g
i
i
n
n
a
a
l
l
i
i
n
n
s
s
t
t
r
r
u
u
c
c
t
t
i
i
o
o
n
n
s
s
)
)
Documentation no.: 3193049h