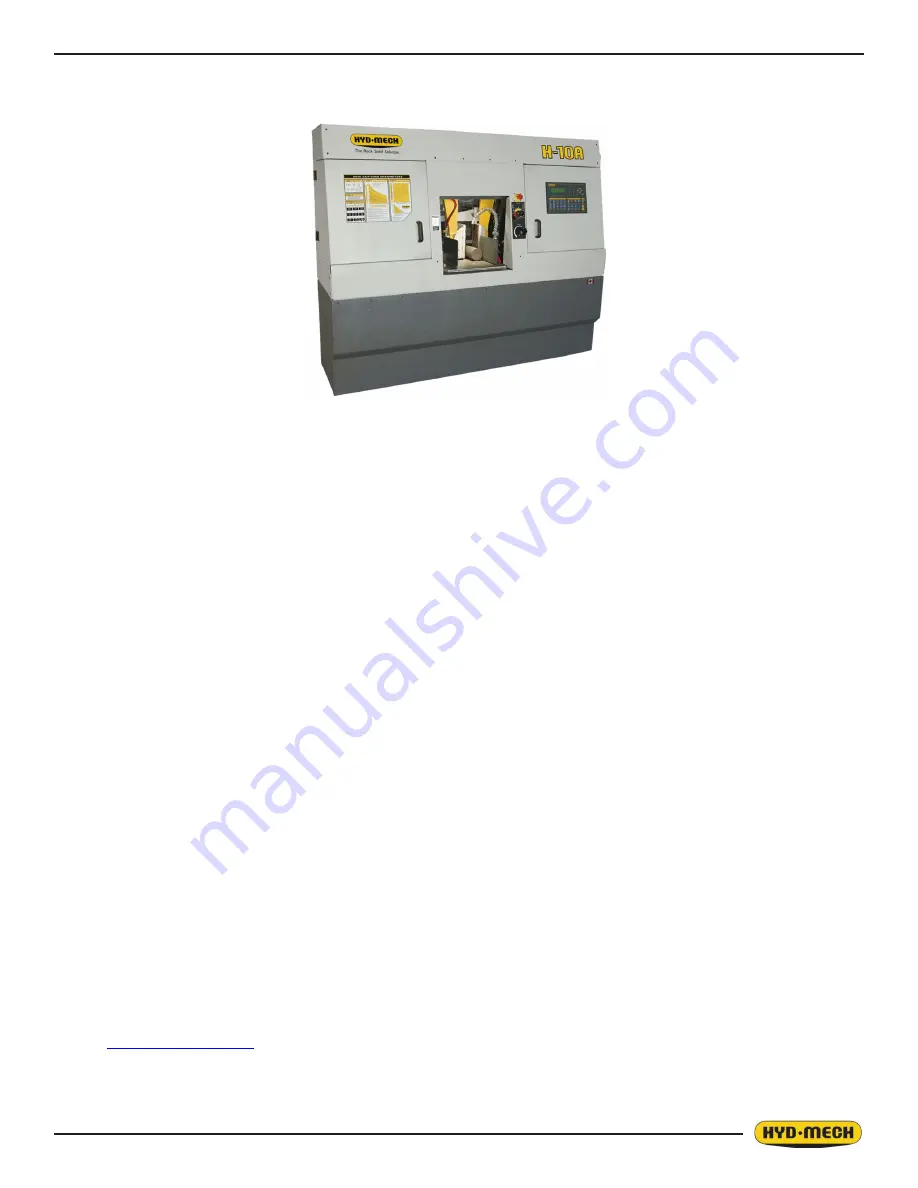
Thank you,
On behalf of everyone at HYD·MECH Group Limited, I would like to thank and congratulate you on your decision to pur-
chase a HYD·MECH bandsaw.
Your new machine is now ready to play a key role in increasing the efficiency of your operation, helping you to reduce cost
while boosting quality and productivity.
To ensure you are maximizing the power and versatility of your new HYD·MECH bandsaw, please take the time to famil-
iarize yourself and your employees with the correct operation and maintenance procedures as outlined in this manual.
We sincerely appreciate the confidence you have demonstrated in purchasing our product and look forward to building a
long and mutually beneficial relationship.
Thank you
Hyd·Mech Group Limited
P.O. Box 030, 079 Parkinson Road
Woodstock, Ontario, N4S 8A4
Phone : (59) 539-634
Service : -877-237-094
Sales : -877-276-SAWS (7297)
Fax : (59) 539-526
e-mail :
H10A
393311
REV A
Summary of Contents for H10A
Page 2: ......
Page 16: ......
Page 38: ......
Page 44: ...3 6 Shuttle Linear Bearings x4 Movable Guide Arm Linear Bearings x2 ...
Page 54: ......
Page 58: ......
Page 59: ...6 1 FOR MECHANICAL ASSEMBLY DRAWINGS SEE PDF ON ATTACHED CD SECTION 6 MECHANICAL ASSEMBLIES ...
Page 60: ......
Page 61: ...7 1 FOR OPTIONAL ASSEMBLIES SEE PDF ON ATTACHED CD SECTION 7 OPTIONS ...
Page 62: ......
Page 64: ...8 2 H10A LAYOUT ...