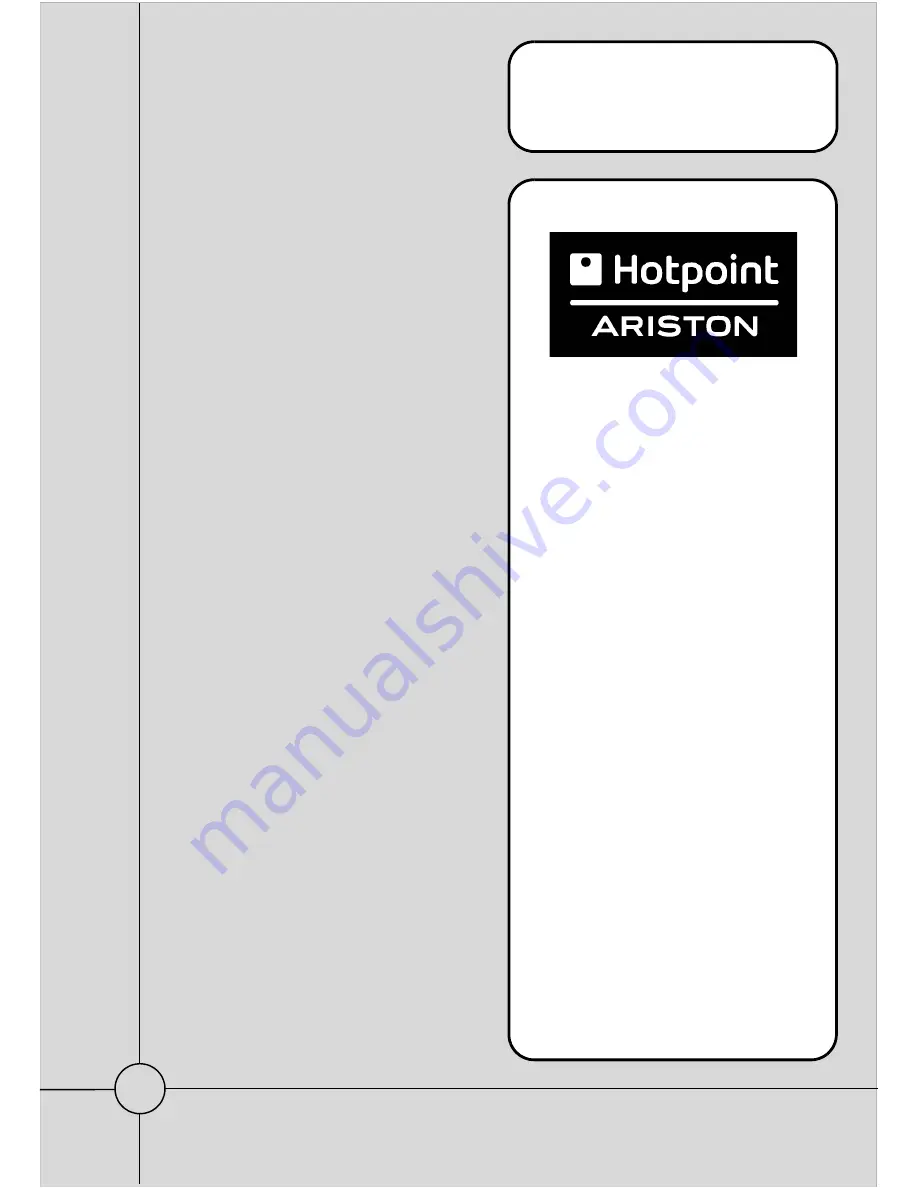
Indesit Company UK Ltd
© 2010 Reg. Office: Peterborough PE2 9JB Registered in London: 106725
Service
Information
Aqualtis
8 Kg
"A Energy"
CONDENSER
ELECTRONIC
TUMBLE DRYER
with
Refrigerant
Condenser System
Models Comm
Covered
Code
AAQCF81U IT
70078
AAQCF81U WE
71832
AAQCF81U UK
71846
5407535 Issue 2 May 2010
..
C00279765