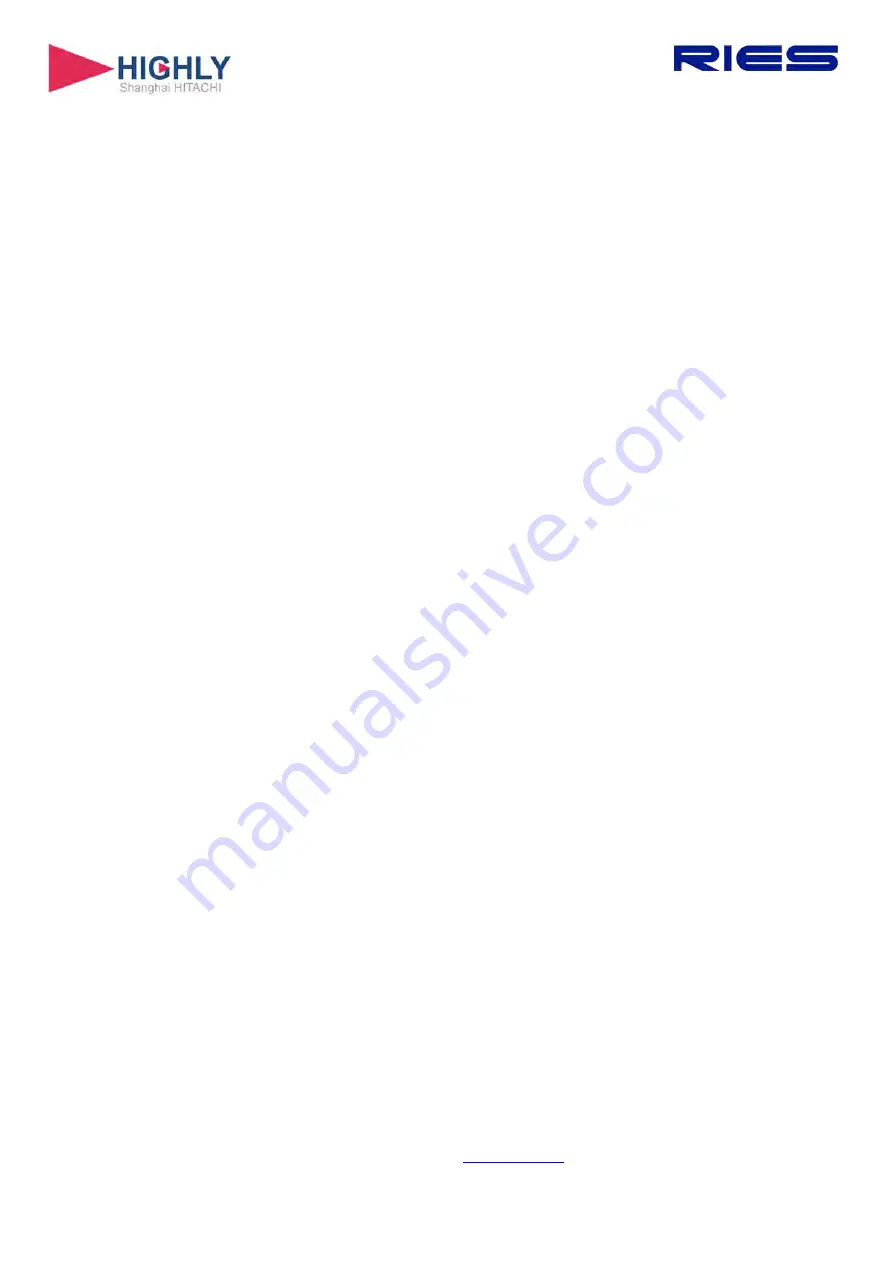
Hitachi
Highly
Rollkolbenverdichter
Rotary Compressors
Spezifikation
Installation Manual
WHP05600VUKQA7JG6
RIES GmbH, Rudolf-Diesel-Str. 10, D 64569 Nauheim, GERMANY
Phone: +49 6152 9741 0, Fax: +49 6152 9741 21, Email:
, Website: www.ries-gmbh.de
R410A/ R454C/ R454B/ R134a
14,1
cm3/rev
10
00 - 7200 min-1
2021-1-19
Summary of Contents for Highly WHP05600VUK
Page 18: ......
Page 19: ...18 29 ...
Page 20: ...19 29 ...
Page 21: ...20 29 ...
Page 22: ...21 29 ...
Page 23: ...22 29 ...
Page 24: ...23 29 ...
Page 25: ...24 29 ...
Page 26: ...25 29 ...
Page 27: ...26 29 ...
Page 29: ...27 29 ...