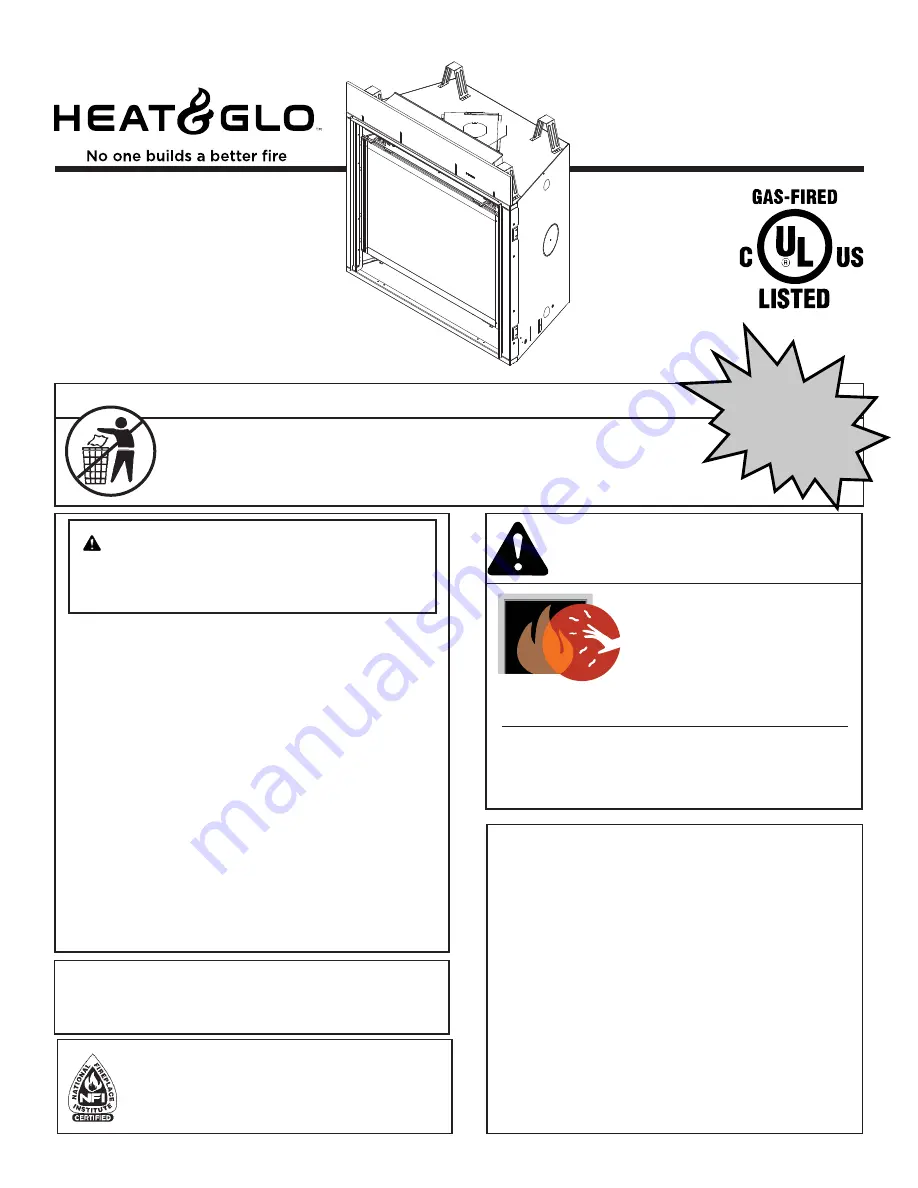
1
Heat & Glo • 6000CL-IPI-S, 6000CL-IPI-T, 8000CL-IPI-S 8000CL-IPI-T • 2165-900 Rev. X • 4/14
•
DO NOT
store or use gasoline or other
fl
am-
mable vapors and liquids in the vicinity of this
or any other appliance.
• What to do if you smell gas
-
DO NOT
try to light any appliance.
-
DO NOT
touch any electrical switch.
DO
NOT
use any phone in your building.
- Immediately call your gas supplier from a
neighbor’s phone. Follow the gas suppli-
er’s instructions.
- If you cannot reach your gas supplier, call
the
fi
re department.
• Installation and service must be performed
by a quali
fi
ed installer, service agency, or the
gas supplier.
WARNING: If the information in these
instructions is not followed exactly, a
fi
re or explosion may result causing prop-
erty damage, personal injury, or death.
Owner’s Manual
Installation and Operation
DO NOT DISCARD THIS MANUAL
NOTICE
Installation and service of this appliance should be
performed by quali
fi
ed personnel. Hearth & Home
Technologies suggests NFI certi
fi
ed or factory trained
professionals, or technicians supervised by an NFI
certi
fi
ed professional.
• Leave this manual with
party responsible for use
and operation.
DO NO
T
DISCARD
• Important operating
and maintenance
instructions included.
• Read, understand and follow
these instructions for safe
installation and operation.
In the Commonwealth of Massachusetts installation must be
performed by a licensed plumber or gas
fi
tter.
See Table of Contents for location of additional Commonwealth
of Massachusetts requirements.
Models:
6000CL-IPI-S
6000CL-IPILP-S
6000CL-IPI-T
6000CL-IPILP-T
8000CL-IPI-S
8000CL-IPILP-S
8000CL-IPI-T
8000CL-IPILP-T
Pour demander un exemplaire en français de ce Manuel
du propriétaire, visitez www.heatnglo.com.
WARNING
A barrier designed to reduce the risk of burns
from the hot viewing glass is provided with this
appliance and shall be installed.
HOT GLASS
WILL
CAUSE BURNS.
DO NOT
TOUCH GLASS
UNTIL COOLED.
NEVER
ALLOW CHILDREN
TO TOUCH GLASS.
This appliance may be installed as an OEM
installation in manufactured home (USA
only) or mobile home and must be installed
in accordance with the manufacturer’s
instructions and the
Manufactured Home
Construction and Safety Standard,
Title 24
CFR, Part 3280
in the United States, or the
Standard for Installation in Mobile Homes,
CAN/CSA Z240 MH Series,
in Canada.
This appliance is only for use with the type(s)
of gas indicated on the rating plate. This
appliance is not convertible for use with other
gases, unless a certi
fi
ed kit is used.