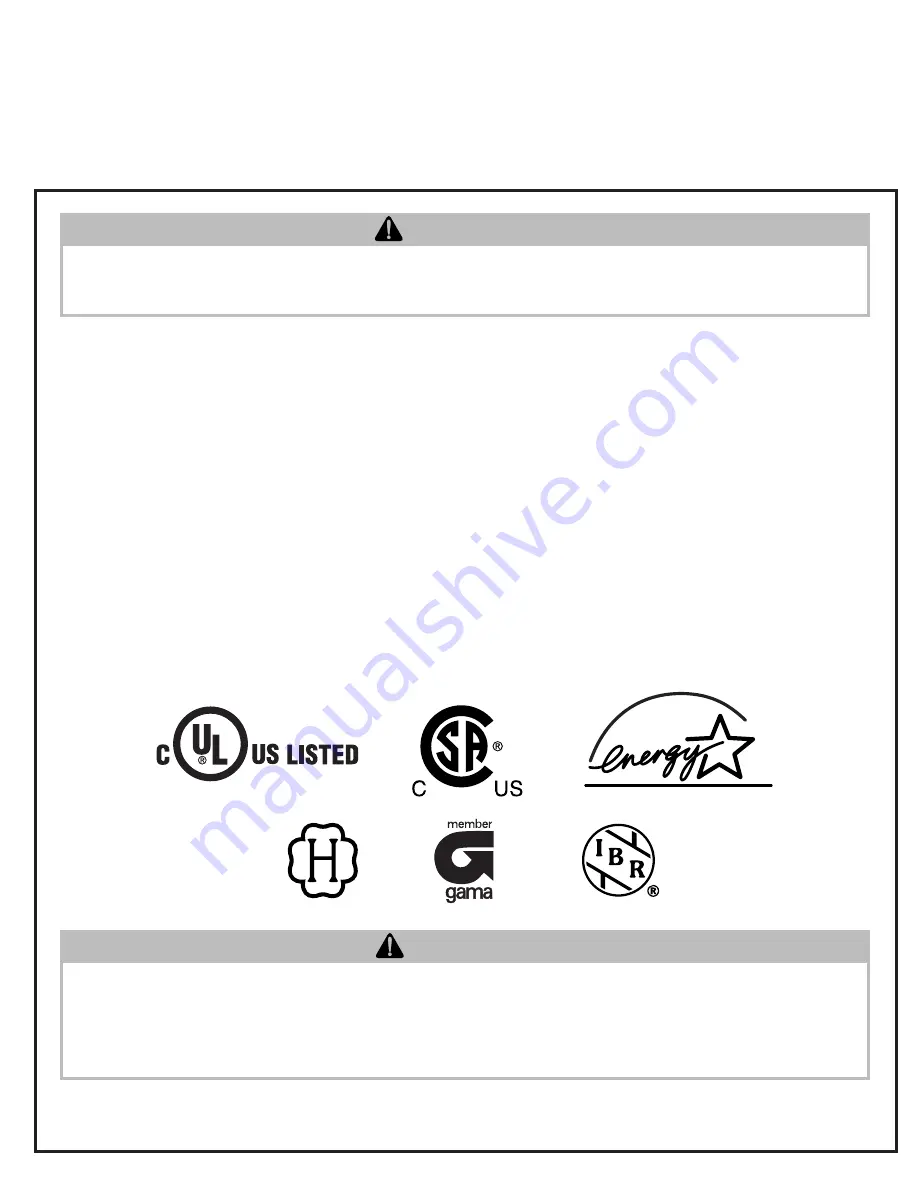
HEAT TRANSFER PRODUCTS, INC.
120 BRALEY RD., E. FREETOWN, MA 02717
Installing, Operating & Maintaining
MUNCHKIN™ HIGH EFFICIENCY HEATER
with the “925” Controller
Do not store or use gasoline or other flammable vapors and
liquids in the vicinity of this or any other appliance.
WHAT TO DO IF YOU SMELL GAS
• Do not try to light any appliance.
• Do not touch any electrical switch: do not use any phone in
your building.
• Immediately call your gas supplier from a neighbor's phone.
Follow the gas supplier's instructions.
• If you cannot reach your gas supplier, call the fire department.
Installation and service must be performed by a qualified
installer, service agency or the gas supplier.
WARNING
If the information in this manual is not followed exactly, a fire or explosion may
result causing property damage, personal injury or loss of life.
WARNING
This manual must only be used by a qualified heating installer / service
technician. Failure to comply could result in severe personal injury, death or
substantial property damage. It is also important to keep these Instructions
with the appliance.
MH27745
CONTROLS