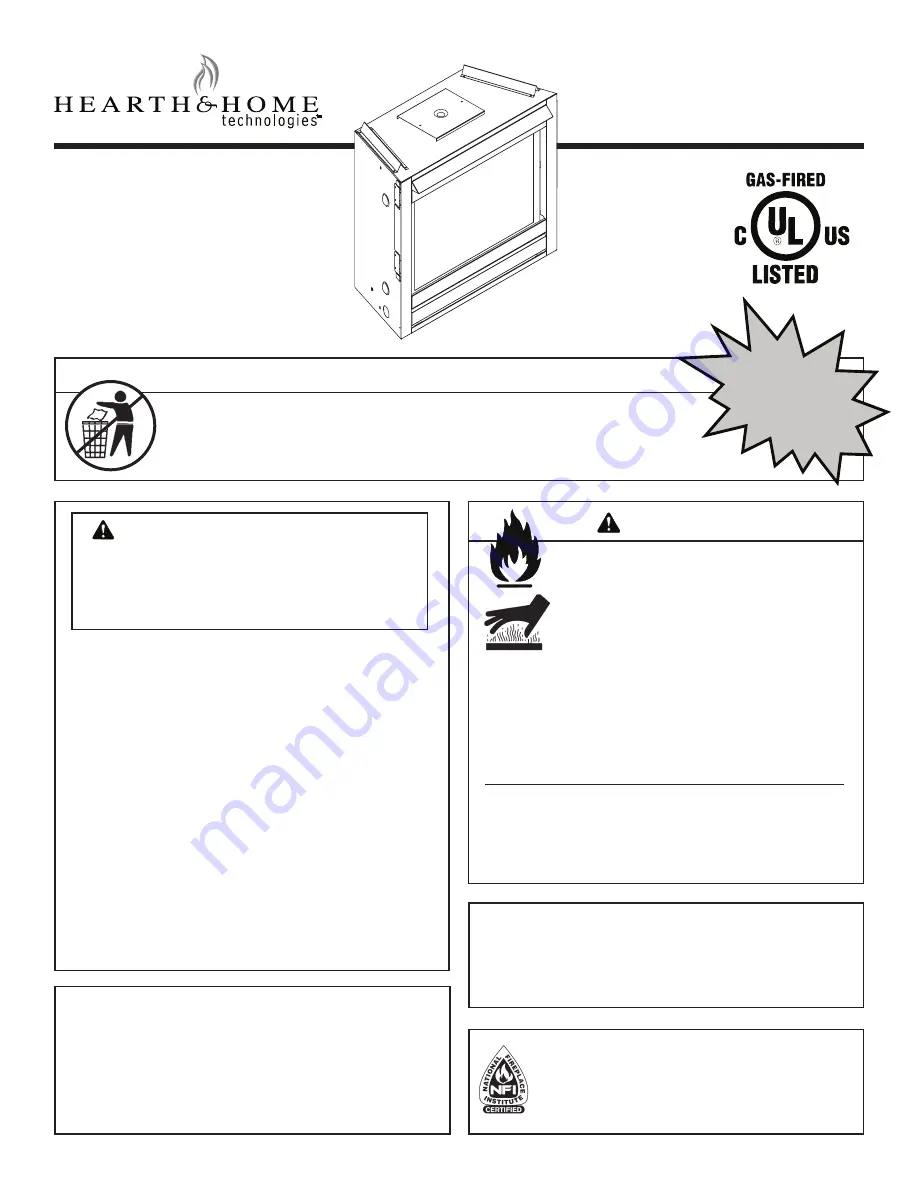
1
Hearth & Home Technologies • BE-36-C, BE-36-CIPI • 397-981 Rev. V 1/07
Models:
BE-36-C
BE-36-CIPI
Owner’s Manual
Installation and Operation
• Do not store or use gasoline or other
fl
am-
mable vapors and liquids in the vicinity of
this or any other appliance.
• What to do if you smell gas
- Do not try to light any appliance
- Do not touch any electrical switch. Do not
use any phone in your building.
- Immediately call your gas supplier from a
neighbor’s phone. Follow the gas suppli-
er’s instructions.
- If you cannot reach your gas supplier, call
the
fi
re department.
• Installation and service must be performed
by a quali
fi
ed installer, service agency, or the
gas supplier.
WARNING: If the information in
these instructions is not followed
exactly, a
fi
re or explosion may result
causing property damage, personal
injury, or death.
This appliance has been supplied with an integral barrier
to prevent direct contact with the
fi
xed glass panel. Do
NOT operate the appliance with the barrier removed.
Contact your dealer or Hearth & Home Technologies if the
barrier is not present or help is needed to properly install one.
HOT! DO NOT TOUCH
.
SEVERE BURNS MAY RESULT.
CLOTHING IGNITION MAY RESULT.
• CAREFULLY SUPERVISE children in same room as
appliance.
• Alert children and adults to hazards of high temperatures.
• Do NOT operate with protective barriers open or
removed.
• Keep clothing, furniture, draperies and other
combustibles away.
Glass and other surfaces are hot during
operation and cool down.
• Keep children away.
DO NOT DISCARD THIS MANUAL
CAUTION
This appliance may be installed as an OEM installation in
manufactured home (USA only) or mobile home and must be
installed in accordance with the manufacturer’s instructions and
the manufactured home construction and safety standard,
Title
24 CFR, Part 3280
or
Standard for Installation in Mobile Homes,
CAN/CSA Z240MH.
This appliance is only for use with the type(s) of gas indicated
on the rating plate.
Installation and service of this appliance should be
performed by quali
fi
ed personnel. Hearth & Home
Technologies suggests NFI certi
fi
ed or factory-trained
professionals, or technicians supervised by an NFI
certi
fi
ed professional.
• Leave this manual with
party responsible for use
and operation.
DO NO
T
DISCARD
WARNING
• Important operating
and maintenance
instructions included.
• Read, understand and follow
these instructions for safe
installation and operation.
In the Commonwealth of Massachusetts:
• installation must be performed by a licensed plumber
or gas
fi
tter;
See Table of Contents for location of additional
Commonwealth of Massachusetts requirements.