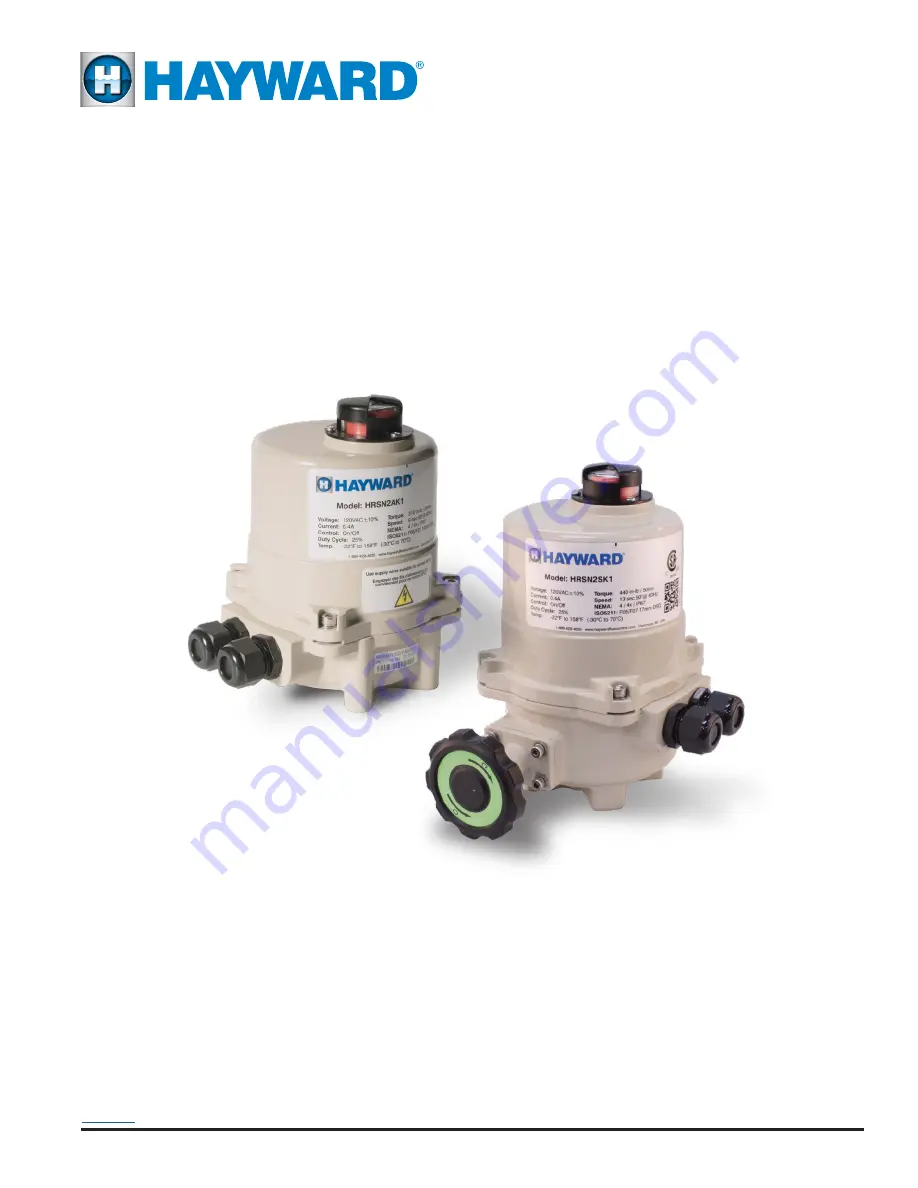
USE ONLY HAYWARD GENUINE REPLACEMENT PARTS
HRSN2IOM Rev D ECR 102V
Page 1 of 36
Hayward Flow Control
1-888-HAY-INDL (1-888-429-4635)
www.haywardflowcontrol.com
TO PREVENT POTENTIAL INJURY OR DAMAGE TO PROPERTY, READ THIS MANUAL CAREFULLY AND COMPLETELY.
INSTALLATION, OPERATION AND
MAINTENANCE INSTRUCTIONS
HRSN2 Series