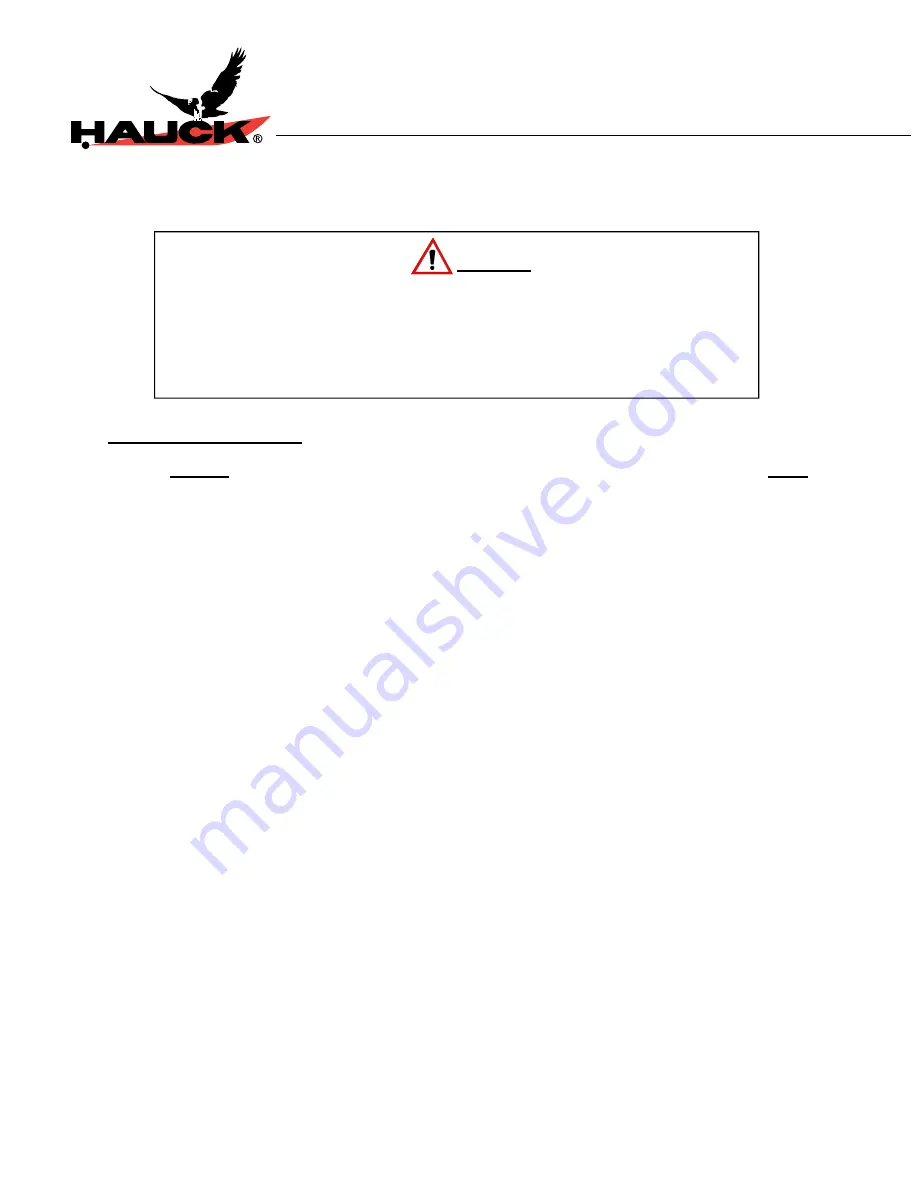
TABLE OF CONTENTS
WARNING
These instructions are intended for use only by experienced, qualified combustion start-
up personnel. Adjustment of this equipment by unqualified personnel can result in fire,
explosion, severe personal injury or even death.
To make changes to the burner or adjust firing inputs: 1. Shut the burner down; 2. Make
changes; 3. Restart the burner.
STAND CLEAR OF THE BURNER UNDER ANY
FIRING CONDITIONS.
INSTRUCTIONS
MEGASTAR
TM
BURNER
MS-50 – MS-150
These instructions are intended to serve as guidelines covering the installation, operation, and maintenance of Hauck equipment. While
every attempt has been made to ensure completeness, unforeseen or unspecified applications, details, and variations may preclude
covering every possible contingency.
WARNING: TO PREVENT THE POSSIBILITY OF SERIOUS BODILY INJURY, DO NOT USE OR
OPERATE ANY EQUIPMENT OR COMPONENT WITH ANY PARTS REMOVED OR ANY PARTS NOT APPROVED BY THE
MANUFACTURER.
Should further information be required or desired or should particular problems arise which are not covered
sufficiently for the purchaser's purpose, contact Hauck Mfg. Co.
MS-9
HAUCK MANUFACTURING CO.,
100 North Harris Street Cleona, PA 17042 717-272-3051
1/15
www.hauckburner.com Fax: 717-273-9882
Subject
Page
A. General
Information…………………………………………………………………… 2
B.
Receiving & Inspection………………………………………………………………..
2
C. Burner
Capacities……………………………………………………………………... 3
D. Dimensions…………………………………………………………………………….. 5
E. Component
Identification…………………………………………………………….. 6
F. Combustion
Flighting…………………………………………………………………. 7
G. Burner
Mounting……………………………………………………………………….
7
H.
Fuel Manifold Installation……………………………………………………………...
8
I.
Natural Gas Fuel Piping System……………………………………………………..
9
J.
Light Fuel Oil Piping System………………………………………………………….
13
K.
Heavy Fuel Oil Piping System……………………………………………………….. 15
L.
Oil Manifold Heat Tracing……………………………………………………………..
18
M.
Heavy Oil Insert Heater……………………………………………………………….
18
N.
Fuel Oil Nozzle………………………………………………………………………… 20
O.
Compressed Air/Oil Atomizer…………………………………………………………
21
P.
Liquid Propane (LP) Fuel Piping System……………………………………………
26
Q.
Liquid Propane (LP) Nozzle…………………………………………………………..
31
R.
Burner Pilot System……………………………………………………………………
33
S. Primary
Air……………………………………………………………………………... 34
T. Burner
Setup…………………………………………………………………………… 34
U. Operation………………………………………………………………………………. 35
V. Adjustments……………………………………………………………………………. 36
W. Maintenance…………………………………………………………………………… 37
X.
Recommended Spare Parts………………………………………………………….
38
Appendix: Field Installation Weld-In Type flights, Y7100………………………..
39
Required Reference: Appropriate Burner Data Sheet
GJ73 Dryer Drum Gas Analysis
GJ75 MegaStar Application Sheet
Summary of Contents for Eco-StarII 100B
Page 11: ...Page 11 MS 9 Figure 3 Simplified Gas and Air Flow Chart Atmospheric Conditions GL86 ...
Page 12: ...Page 12 MS 9 Figure 4 MegaStar Gas Orifice Meters Graph ...
Page 30: ...Page 30 MS 9 Figure 14 Vapor Pressures of Propane Butane and Butane Propane Mixtures ...
Page 39: ...Page 39 MS 9 APPENDIX ...
Page 40: ...Page 40 MS 9 APPENDIX ...
Page 41: ...Page 41 MS 9 APPENDIX ...
Page 42: ...Page 42 MS 9 APPENDIX ...
Page 43: ...Page 43 MS 9 APPENDIX ...
Page 44: ...Page 44 MS 9 APPENDIX ...
Page 45: ...Page 45 MS 9 APPENDIX ...
Page 46: ...Page 46 MS 9 APPENDIX ...