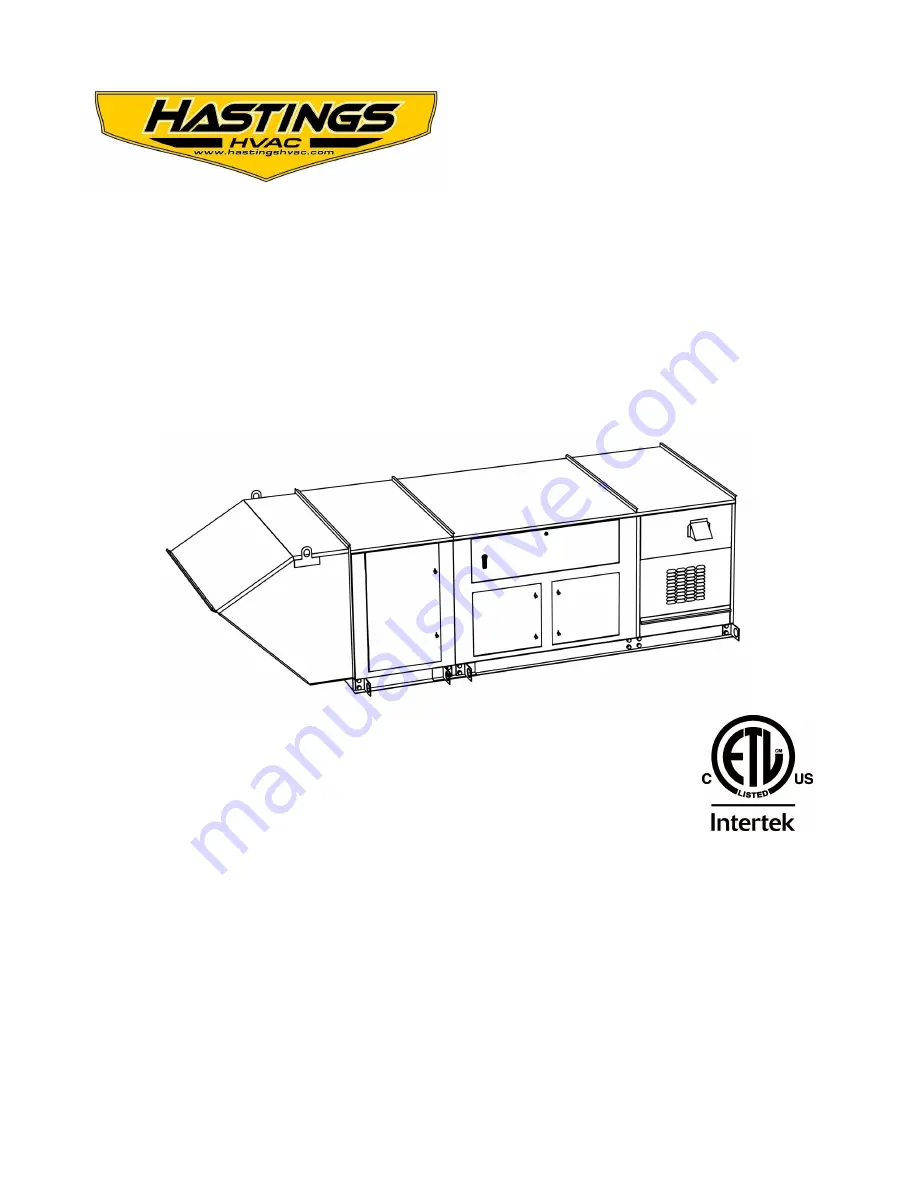
OCTOBER 2016
Installation and Service Manual
Indoor/Outdoor Heating
and
Individual Duct Furnaces
Notice
Read These Instructions Before Installation
RECEIVING INSTRUCTIONS
Inspect unit on arrival for any shipping damage. If any part is missing or damaged, notify the
transportation company.
This unit has been test fired for at least 15 minutes to prove out all phases of operation
IST DUCT FURNACE SYSTEMS