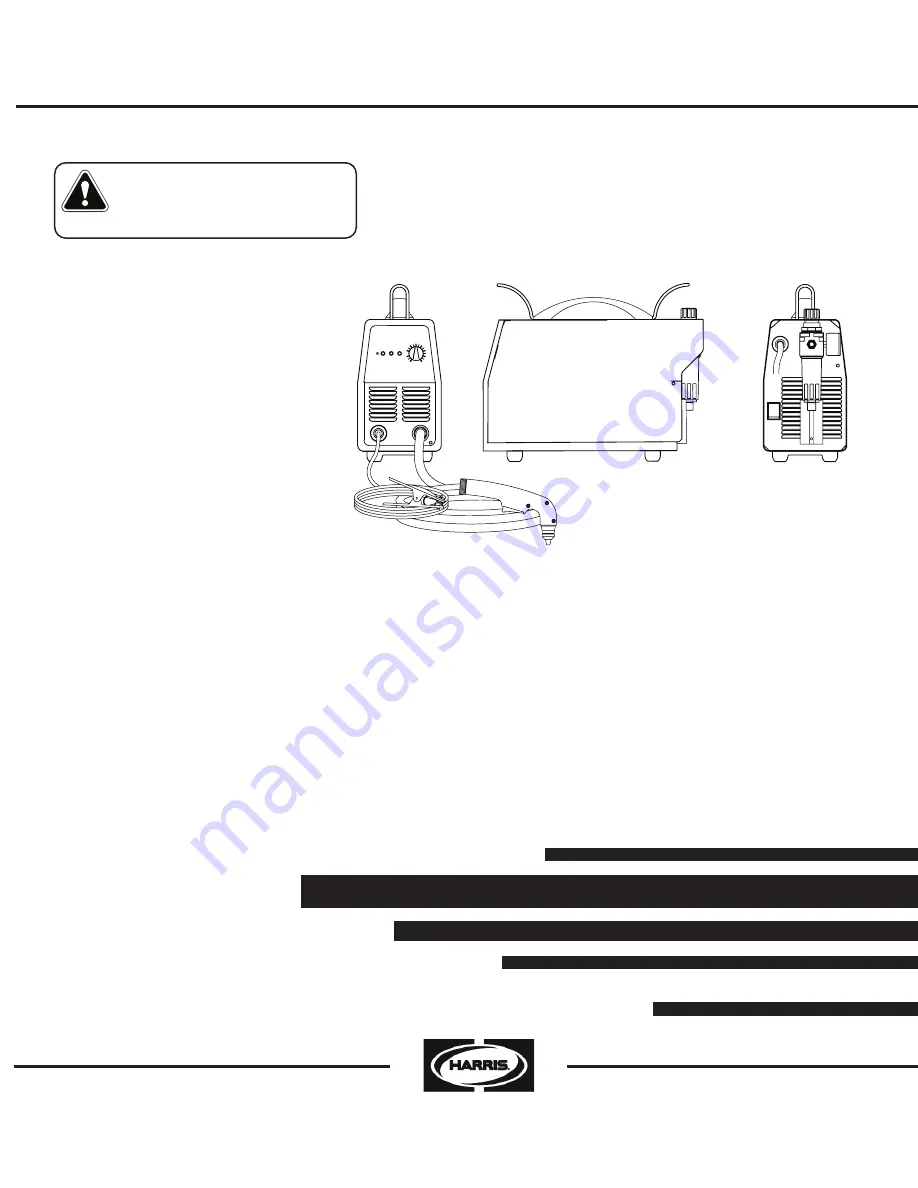
POWERTORCH
™
PLASMA 20
OPERATOR’S MANUAL
IM944
December, 2008
Safety Depends on You
Harris arc welding and cutting
equipment is designed and built
with safety in mind. However, your
overall safety can be increased by
proper installation ... and thought-
ful operation on your part.
DO
NOT INSTALL, OPERATE OR
REPAIR THIS EQUIPMENT
WITHOUT
READING
THIS
MANUAL AND THE SAFETY
PRECAUTIONS CONTAINED
THROUGHOUT.
And,
most
importantly, think before you act
and be careful.
For use with machines having Code Number:
11453
Gainesville, GA 30504-6000 U.S.A. TEL: 866.236.0044 FAX: 800.840.8684
Copyright © Lincoln Global Inc.
This manual covers equipment which is no
longer in production by The Lincoln Electric Co.
Specifications and availability of optional
features may have changed.