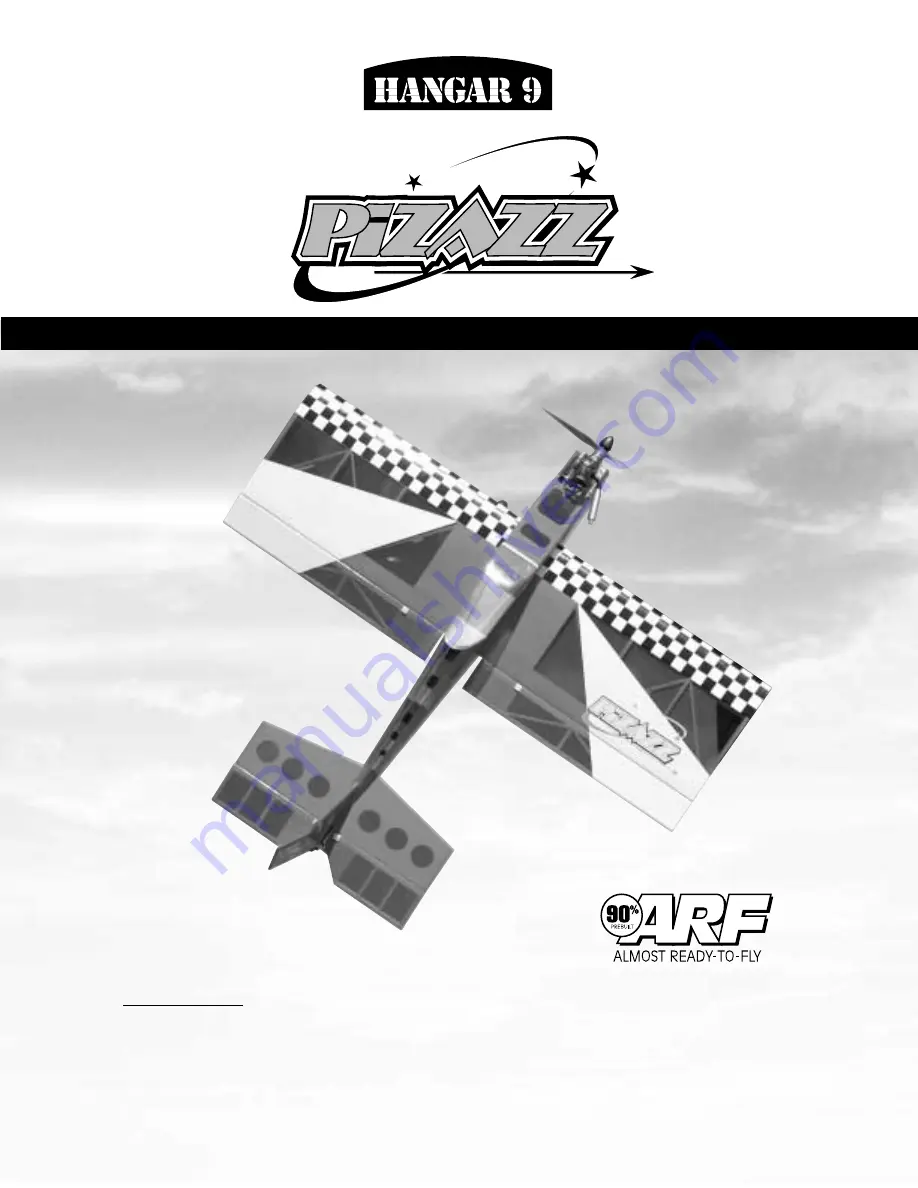
INSTRUCTION MANUAL
Specifications:
• Wingspan: ............................................................................................................ 48 in (1219 mm)
• Overall Length: ................................................................................................... 48 in (1219 mm)
• Wing Area:................................................................................................ 725 sq in (46.8 dm sq)
• Weight (Approx.): ................................................................................. 4.5-5.5 lbs (2.0-2.5 kg)
Recommended Engines:
2-Cycle: .40-.58
4-Cycle: .50-.72
• 90% prebuilt
• Hardware included
• Precovered with Hangar 9
™
UltraCote
®
• Incredible 3-D/fun-fly performer
WE GET PEOPLE FLYING
TM
TM
TM