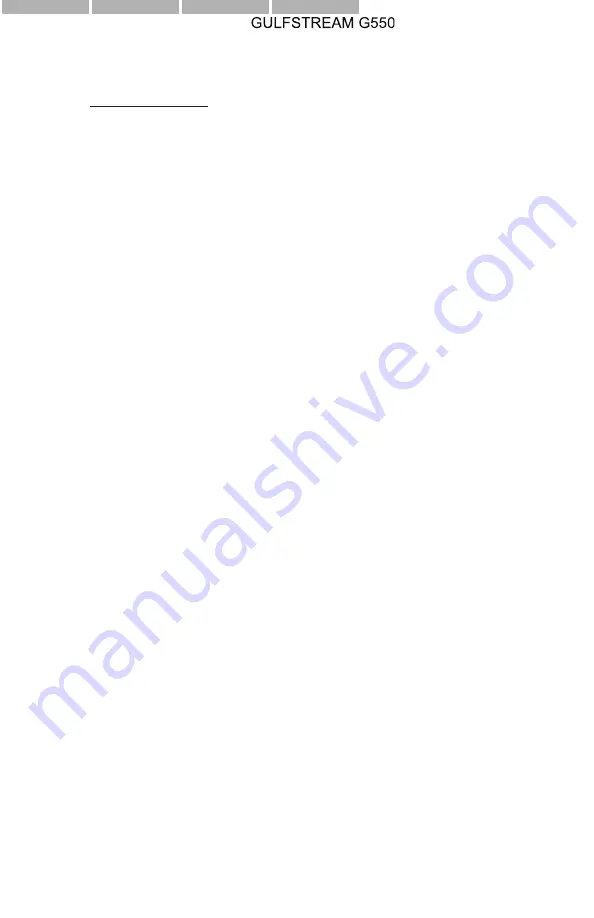
FLIGHT CONTROLS
2A-27-10: General
1. General Description:
The aircraft flight controls allow the flight crew to guide the aircraft in the
longitudinal, vertical and horizontal axes (see Figure 2). The primary flight controls
are:
•
Elevator to control aircraft pitch
•
Rudder to control aircraft yaw
•
Aileron to control aircraft roll
The primary flight controls are positioned by moving the pilot and copilot control
yokes and rudder pedals. Both yokes are mechanically linked together so that
either crew position has full control authority and control inputs are transparent to
both crew members since movement of one set of controls will move the
corresponding set of controls. Each yoke has a dedicated cable connection to the
elevator and aileron control on that respective side, but since the yokes are
mechanically linked, moving one side elevator or aileron will move the flight
controls on both sides. For instance, the copilot yoke is cable-linked to the right
elevator and the right aileron but any movement of the copilot yoke also moves
the pilot yoke that is in turn cable-linked to the left aileron and left elevator. This
system of split control authority and linked yoke movement provides a means to
maintain some flight control movement if one of the flight controls or associated
linkages becomes jammed. If a malfunction prevents movement of either the
elevators or ailerons, the mechanical links joining the two pilot yokes can be
severed, thereby allowing movement of the left or right elevator or aileron that
remains operational by commands using the yoke connected to the side of the
free control surface.
The two sets of rudder pedals are similarly mechanically linked together, but both
are connected to the rudder by a single cable. For this reason, there is no
provision for interrupting the linkage between the two sets of pedals, since each
set does not have an independent route to the rudder.
The cable connections from the yokes and rudder pedals are continuous loop
installations, providing feedback to the moveable controls. The control cables
engage bell cranks that translate cable movement into displacement commands
for hydraulic actuators that boost contol inputs to move the flight controls. Each
hydraulic actuator has a single shaft, but dual piston chambers in order that the
actuator may be driven by both (or either) left and right hydraulic system. (The
hydraulic system power sources for the flight controls are shown in Figure 1.) The
rudder actuator may also be powered by the Auxiliary (AUX) hydraulic system in
the event of dual hydraulic power failure. Each of the hydraulic actuators is
connected to the associated flight control by pushrods and bell cranks to impart
mechanical movement to the control surface. A bungee piston filled with hydraulic
fluid moderates the rate of actuation of the flight control and provides an artificial
feel input to the flight crew through the closed loop cable system. The failure of a
single hydraulic system does not degrade flight control operation - the remaining
system provides adequate power for flight control movement, and the actuator
chamber for the failed system bypasses fluid so there is no resistance to flow. If
both (or all, in the case of the rudder) hydraulic systems fail, both actuator
chambers bypass fluid, and pilot input through the cable connection moves the
OPERATING MANUAL
PRODUCTION AIRCRAFT SYSTEMS
2A-27-00
Page 1
August 14/03
Title Page
Prev Page
Next Page
TOC
Summary of Contents for G550
Page 6: ...Title Page Prev Page Next Page TOC ...
Page 16: ...Title Page Prev Page Next Page TOC ...
Page 18: ...Title Page Prev Page Next Page TOC ...
Page 20: ...Title Page Prev Page Next Page TOC ...
Page 32: ...Title Page Prev Page Next Page TOC ...
Page 44: ...Title Page Prev Page Next Page TOC ...
Page 46: ...Title Page Prev Page Next Page TOC ...
Page 54: ...Title Page Prev Page Next Page TOC ...
Page 58: ...Title Page Prev Page Next Page TOC ...
Page 60: ...Title Page Prev Page Next Page TOC ...
Page 68: ...Title Page Prev Page Next Page TOC ...
Page 80: ...Title Page Prev Page Next Page TOC ...
Page 82: ...Title Page Prev Page Next Page TOC ...
Page 84: ...Title Page Prev Page Next Page TOC ...
Page 86: ...Title Page Prev Page Next Page TOC ...
Page 88: ...Title Page Prev Page Next Page TOC ...