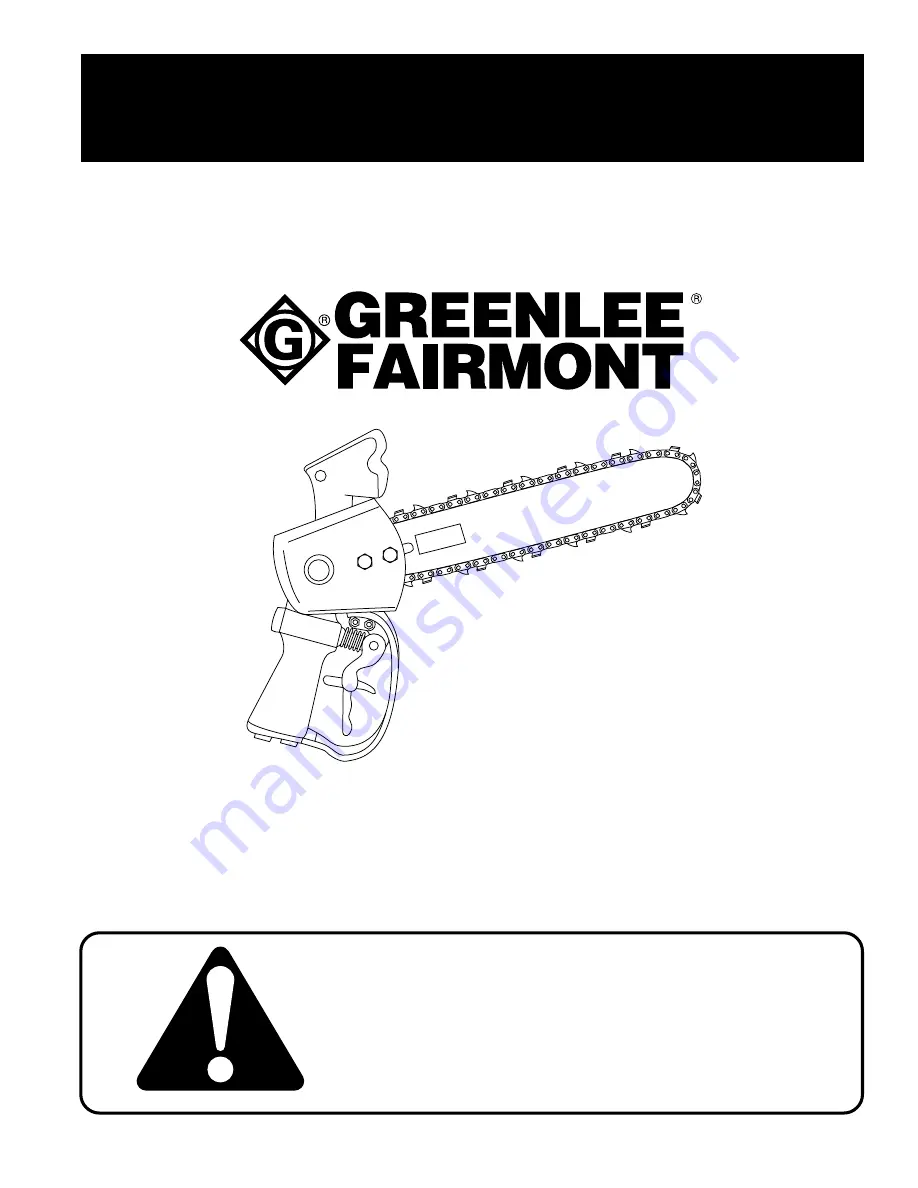
OPERATION, SERVICE AND PARTS
INSTRUCTION MANUAL
999 1304.6 REV 2
©1997 Greenlee Textron
6/97
Read and understand this material before
operating or servicing this tool. Failure to
understand how to safely operate the tool
could result in an accident causing serious
injury or death.
43179
PISTOL GRIP CHAIN SAW
Limb-Lopper
TM
by