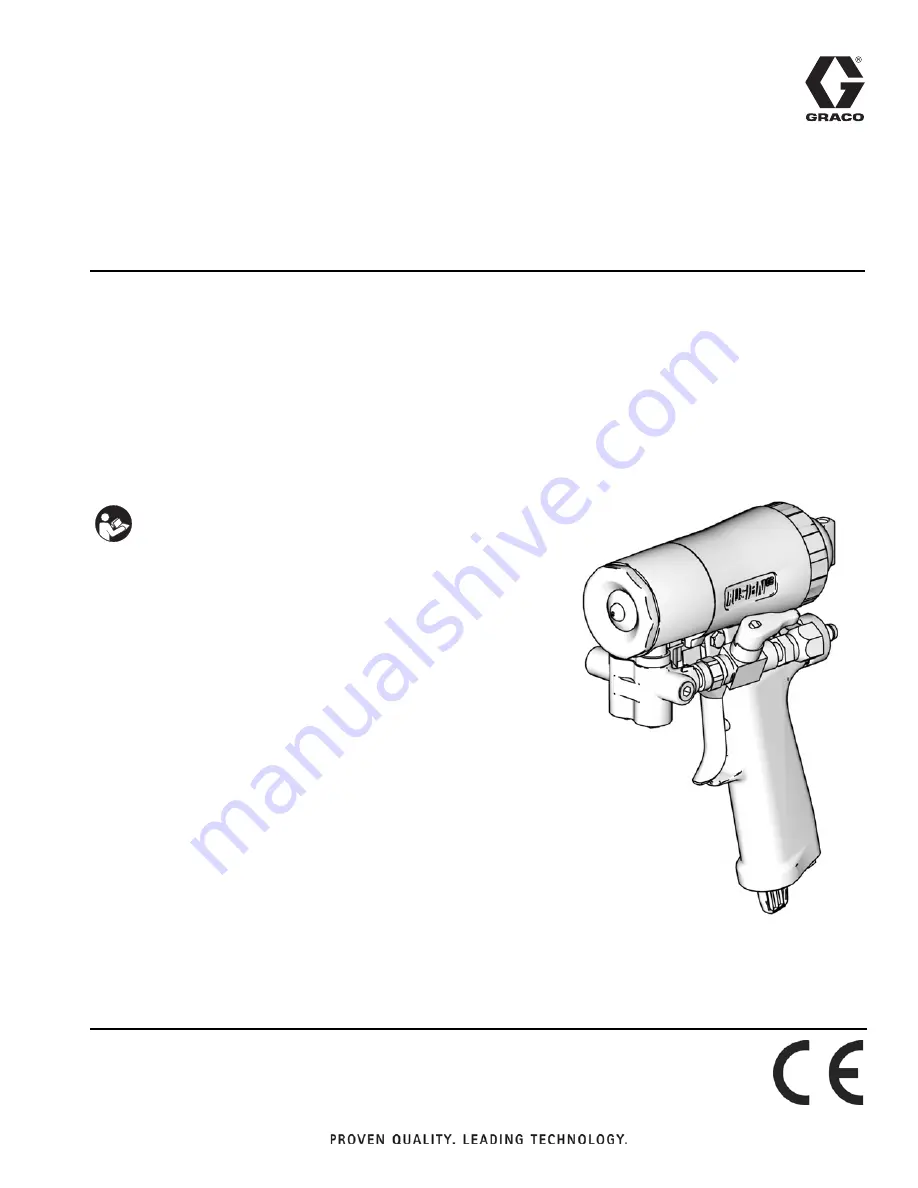
Instructions
Fusion
™
CS
For plural component, impingement mix air purge spray gun with ClearShot
™
Liquid
technology. For professional use only.
For use with non-flammable foam and polyurea. Not for use in explosive atmospheres.
3500 psi (24.5 MPa, 245 bar) Maximum Fluid Working Pressure
80-130 psi (0.56-0.9 MPa, 5.6-9.0 bar) Air Inlet Pressure Range
200° F (94° C) Maximum Fluid Temperature
See page 4 for model information.
Important Safety Instructions
Read all warnings and instructions in this
manual. Save these instructions.
TI11323a
312666W
EN