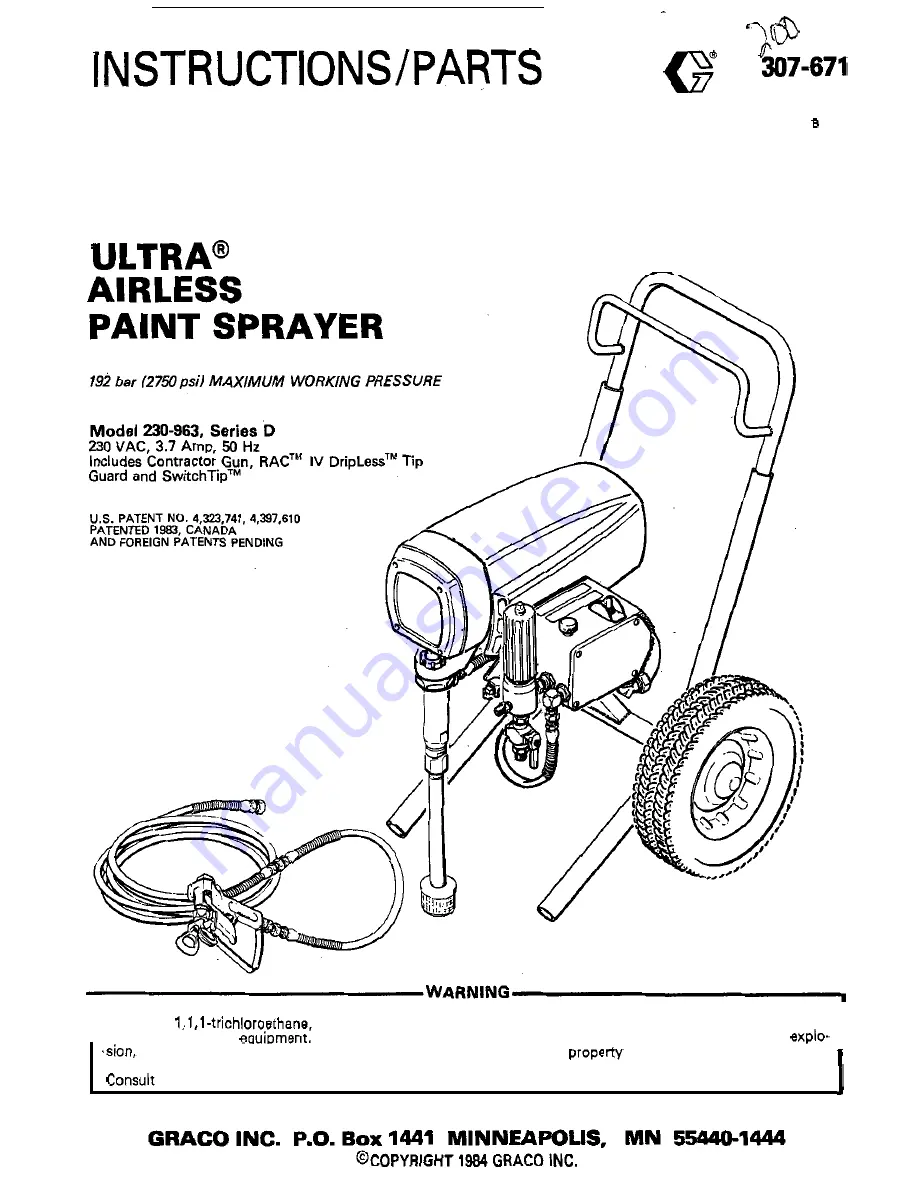
LIST
ORACO
Rev
D
SUPERSEDES
A
and
PCN
This
manual contains
IMPORTANT
WARNINGS
and
INSTRUCTIONS
READ
AND
RETAIN FOR REFERENCE
400
I
Hazard
of
Using Fluids Containing Halogenated Hydrocarbons
such solvents in this
Such use could result in
a
serious chemical reaction, with the possibility
of
Never use
methylene chloride, other halogenated hydrocarbon solvents or fluids containing
I
which could cause death, serious bodily injury and/or substantial
damage.
your fluid suppliers to ensure that the fluids being used are compatible with aluminum and zinc
parts.