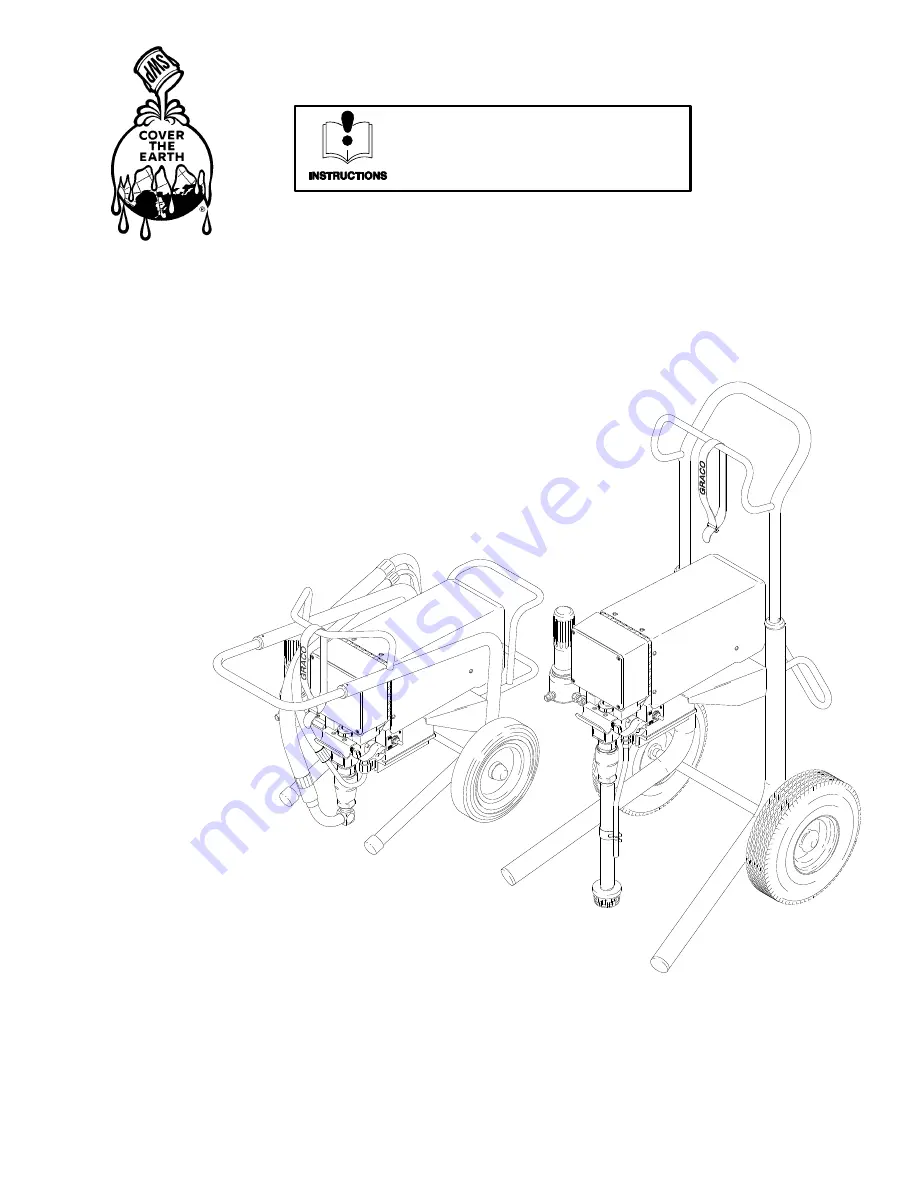
7786A
Model 824–132
Model 824–130
Related Manuals
Displacement Pump
308–815
. . . . . . . . . . . . . . . .
Fluid Filter
308–249
. . . . . . . . . . . . . . . . . . . . . . . . .
7787A
OWNER’S
MANUAL
824–135
Rev. B
Supercedes Rev. A
ELECTRIC, 120 VAC
ULTIMATE
Mx
695
Airless Paint Sprayer
3000 psi (210 bar, 21 MPa) Maximum Working Pressure
Model 824–130, Series A
Upright basic sprayer only
Model 824–132, Series A
Lo-Boy basic sprayer only
The SHERWIN–WILLIAMS COMPANY, CLEVELAND, OHIO 44115
COPYRIGHT 1997, GRACO INC.
This manual contains important
warnings and information.
READ AND RETAIN FOR REFERENCE