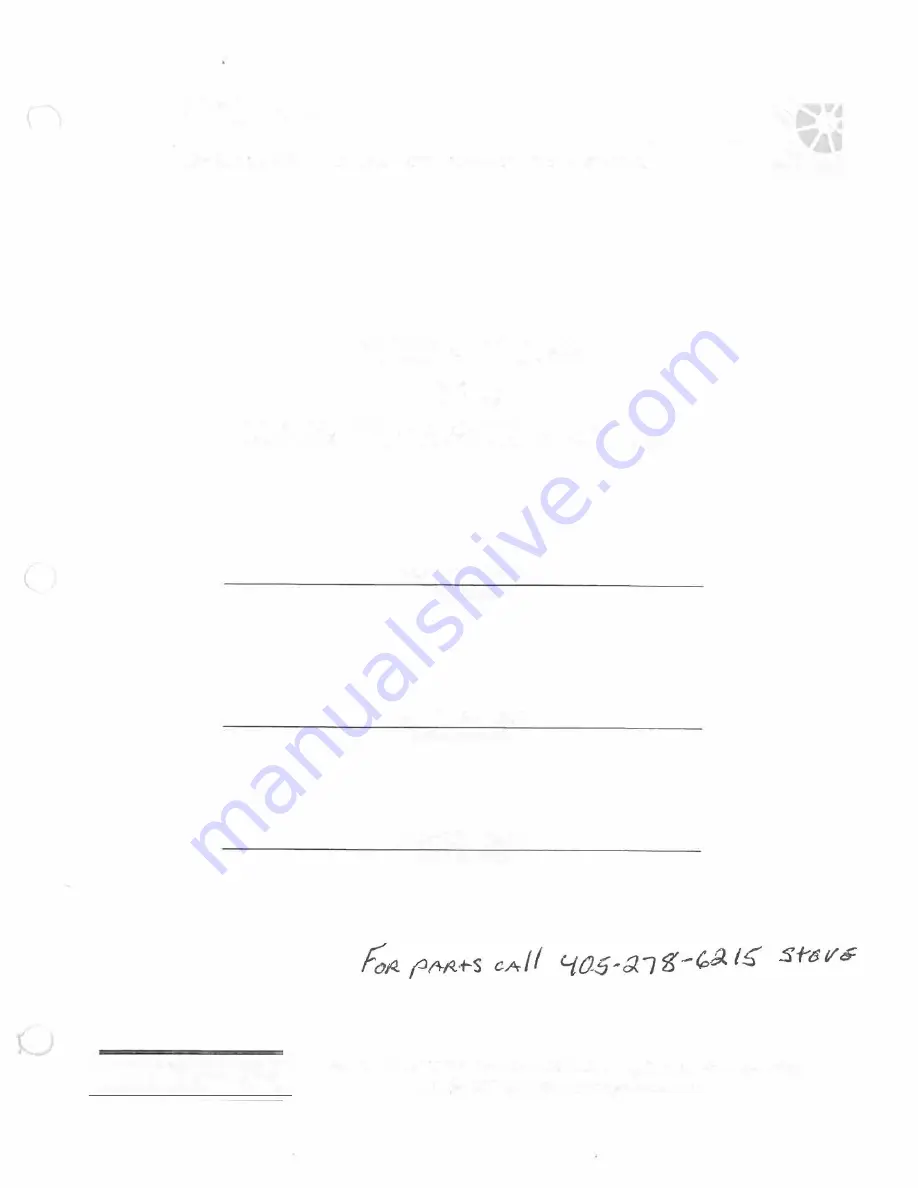
Goff, Inc.
�
--12-2-1 6-NS-35_2_0_*_P_-o-.-Bo_x_1_6 0_ 7_*_S_e_m_in-ol-e,-O-K-74-8 -18---16_0_7 ___ �
OPERATIONS
AND
MAINTENANCE MANUAL
(liDFF:]
2460 SPINNER
MACHINE
07461-50-7220
SERIAL NUMBER
AUGUST2007
DATE SHIPPED
Ph: 405-382-6900 * Fax: 405-382-7013 * Toll Free: 800-654-4633
[email protected] * www.goff-inc.com
Summary of Contents for 2460
Page 6: ...SECTION 1 GENERAL INFORMATION General Description 1 1 Installation Procedures 1 2 ...
Page 15: ...M0I099 CW BLAST WHEEL FRONT VIEW Refer to replacement parts list on page 2 2 2 5 ...
Page 16: ...MOI OO 0 I CCW BLAST WHEEL FRONT VIEW Refer to replacement parts list on page 2 3 2 6 ...
Page 17: ...M0581B BLAST WHEEL SIDE VIEW Refer to replacement parts list on page 2 2 2 3 2 7 ...
Page 18: ...M058IC BLAST WHEEL EXPLODED VIEW Refer to replacement parts list on page 2 2 2 3 2 8 ...
Page 38: ...M01159A 0 0 I 0 FRONT VIEW DETAIL Refer to replacement part list on page 3 1 3 3 ...
Page 39: ...MO 159B L SIDE VIEW DETAIL Refer to replacement part list on page 3 1 3 4 ...
Page 41: ...MOl 159D I I G SPAN SPINNER DETAIL Refer to replacement part list on page 3 1 3 6 ...
Page 42: ...MOl 159E l I CHMHBER E THRUST BEARING DETAIL Refer to replacement part list on page 3 1 3 7 ...
Page 43: ...M01 159F SPAN DETAIL l Refer to replacement part list on page 3 1 3 8 ...
Page 44: ... G M01 159G CHAMBER DRIVE ASSEMBLY DETAIL Refer to replacement part list on page 3 1 3 9 ...
Page 55: ...M01163B 0 9 ELEVATOR BOTTOM ASSEMBLY Refer to replacement parts list on page 4 9 4 10 4 ...